Risk reduction when insulating rim/sill under suboptimal conditions

Greetings all-
We had an energy audit done back about 5 years ago and I’ve become a bit of an energy/building nerd since then. I’ve read hundreds of hours of articles on fhb, gba, nrel.gov, etc.
Last year there was a question posed about the risk involved with interior insulation on the sill/rim joist areas.
https://www.greenbuildingadvisor.com/community/forum/energy-efficiency-and-durability/57366/insulate-rim-joist-rigid-foam-exposed-concret
When asked about insulating these areas “even when a capillary break is lacking” Martin replied: “How risky is this? Somewhat — because the interior insulation reduces the ability of the sill or rim joist to dry inward, and these wooden components may be damp due to capillarity”.
My house has poor original construction choices related to this that lead me here before I stop thinking/obsessing about, and finally begin this next project.
The house in question is an aluminum sided 1989 2500sf 2 story located W of Chicago, zone 5A with clay soil. Basement is poured concrete, has an interior perimeter drain and no water issues for ten years. 1,000sf is basement and 440sf is a partial basement crawl of sharp gravel covered with torn polyethylene sheeting. The basement has a large Sanidry dehumidifier, a two-pipe condensing furnace and a NG powervent water heater.
In three spots, the builder placed concrete that appears to be directly against the rim joist. Two of these are stoops under doors, the other being a 32×5 NW facing concrete front porch with a roof. One of the stoop areas was completely rotted thru when we purchased the house and was replaced before closing- meaning in just 16 years the wood was destroyed. Unknown if there were contributing factors.
The last pieces of the unfortunate puzzle are that between the NON-pressure treated sill and the foundation is only maybe 1/8” compressed fiberglass, and a grading that has soil up to within 4 inches of the sill.
I’m getting ready to insulate the entire basement/crawl and then later create a finished basement. With all I’ve learned here, I’m worried about the drying potential for the wood if I cover the rim with XPS like cut-n-cobble OR XPS and spray like Martin’s ‘peanut brittle’ method.
My questions are 1) How does one mitigate risk in situations such as these? Especially in those areas that seem high risk? Different insulation types? Redo the grading?- even if it would reduce slope? Replace soil at the top foot of grade with gravel? 2) When it’s time to finish the basement, would different construction types change this risk? Meaning air-tight drywall vs. dropped ceiling vs. no ceiling.
The rest of the plan:
3/4 XPS R-4 with taped seams on the floor topped with 3/4 ply screwed down. Followed on walls by double layer 1” foil faced polyiso R-11ish w/offset taped seams ‘glued’ to the concrete, with 2×4 wall butt against the polyiso and covered with drywall. (IL code is 10/13)
The crawl plan: Cover the sharp rocks with geotextile fabric, followed by polyethylene sheeting that will be adhered to the concrete. Overlapped seams, taped, etc. Followed by the double layer polyiso on the wall like the basement.
It’s entirely possible I’m overthinking this and just need to jump in. But I also don’t want to create huge problems where they don’t currently exist.
Thanks,
Jim
GBA Detail Library
A collection of one thousand construction details organized by climate and house part
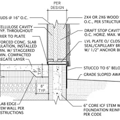
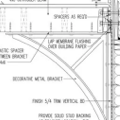
Replies
Jim,
Q. "How does one mitigate risk in situations such as these? Especially in those areas that seem high risk?"
A. Jack up the house and slip a capillary break (metal flashing or EPDM flashing) between the concrete wall and the wooden sill. More information here: "Rubble Foundations."
Also: Remove all exterior concrete placed against wooden components of the building and, where necessary, lower the grade.
-- Martin Holladay
Some observations and a follow up 5 months later:
1) Getting construction workers to agree to give estimates is difficult..
2) Finding one who is willing to do this is impossible. And I don't mean impossible at a reasonable price.
In 5 months I had 4 come out and the basic takeaway was: Removing the concrete basically involves redoing the entire front of my house, and only 1 out of the 4 thought that jacking and replacing the sill barrier would be possible without huge problems stemming from the fireplace, and something about the opposite wall being some sort of special load bearing because the above master doesn't have a regular flat ceiling.
So I'm still stuck where I was before, but with even less options than before.
I realize that this house isn't optimal, or even maybe good. It is what it is. So back to the original question. Is there one way of insulating this sub-standard rim that is LESS risky than the others. Not perfect, but just better.
2 of the guys said that the originally builder didn't care what happened after they built it, so why would I care what happens in 10-20 years when I'm not here.
I don't want to be that guy, but I'm beginning to think there's no option.
Jim,
If you are worried about sill rot and rim joist rot, leave these areas uninsulated. Just perform air sealing work, and check the soundness of the wood every year.
Sometimes, it just isn't possible (or cost-effective) to make an older house as energy-efficient as a new home.