Rim Joist Area of 1966 home in Cold Climate

Greetings,
I am a fairly new homeowner (2 yrs) of a 1966 house in Southern Ontario, Canada. I recently needed to replace the hvac system and went for an all-electric heat pump system, which has been great, thanks to good advice from members of this forum.
I guess you could say I caught the home efficiency bug because now I’m looking to improve various other aspects of the house. I had an energy audit done and there were a few recommendations for air sealing and insulation, one of which was the rim joist area.
After some research it sounds like the best approach will be to install 2 layers of 1.5″ rockwool comfortboard (https://www.rockwool.com/north-america/products-and-applications/products/comfortboard-80/) instead of the stuffed in fibreglass batts that are currently there.
Here are a few photos of one of the joist cavities, showing the old insulation in place, the joist cavity with old insulation removed, and a detail of what it looks like at the top of the wall. There is a gap between what looks like the wood framed basement wall and the concrete foundation wall. There is thick black paper-like material stapled to the face of what looks like the sill plate. When I pulled out the old insulation, it looked very dirty on the bottom half of the inner layer, I guess from years of infiltration of dirty air…possibly coming up from that large gap at the top of the wall?
Where I am not clear is:
– What are the unique details to look for when insulating this area?
– What to do when I can’t see or access the joint between the concrete foundation wall and the sill plate?
– What is the large gap at the top of the wall assembly – does this need to “breathe” or should it be sealed off somehow?
– Where to do the air sealing and what technique/material to use?
– How to make sure I don’t do things that cause other problems?
Thanks in advance for your advice.
GBA Detail Library
A collection of one thousand construction details organized by climate and house part
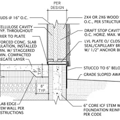
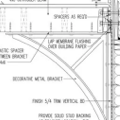
Replies
The black is probably at least partly mold. You should not be using a fibrous insulating material -- batt OR Comfortboard -- against the inside of the rim joist UNLESS you have enough exterior rigid foam over the outside of it for your climate zone, which is doubtful in older homes. You need to insulate this area with something that is not vapor permeable to keep moisture from migrating through the insulation and condensing on the cold surface of the rim joist. In my own home, I use EPS for this, and "foamed in" blocks in each joist bay using canned foam. I used Loctite's TiteFoam here, which I find to be more durable than Great Stuff for applications like this. You can also use closed cell spray foam here, which is commonly done. Both methods work when done correctly. You can beef up the total R value a bit using fibrous insulation over the foam, but you should NOT be using fibrous insulation only here.
The black stuff looks like tar paper, and might be behind your siding. It's difficult to tell for sure from the pic.
Air sealing should get ALL joints and holes, paying particular attention to any joints/holes that are between indoor conditioned spaces and any spaces that are suspected to be connected to the outdoors. Remember that the goal is to block all pathways for air to leak from inside to outside the home (or vice versa). Canned foam and caulk are usually used for this, depending on the size of the gap (canned foam for gaps 3/16-1/4" or so and larger, caulk for smaller gaps).
I'm not sure what the "big gap" you mention at the top of the wall is, since I only see the rim joist area in the pics?
You can be sure to do it right by asking questions about anything you're unsure of on these forums. There is a great wealth of knowledge here between all of the members.
Bill
Thanks very much for the reply Bill! I'm definitely in the research/learning phase and appreciate all the insight I can get.
You're right - there's no exterior insulation on this house. I have read about the approach of using vapour impermeable materials for the rim joist insulation, so your comment lines up with that. I guess the wood would dry to the outside if it ever gets wet, but it shouldn't get wet as long as the exterior grading is done properly right?
The black paper is hanging on the inside of the concrete basement wall which has soil on the other side -- no siding below grade :)
My basement was finished many years ago by a previous home owner and appears to have a standard poly sheet in front of the fiberglass-batt insulated 2x4 walls. Would I be best to try to tie into the top edge of the poly sheet to continue the vapour barrier up over the rim joist space? In that case does the insulation still need to be vapour impermeable?
The big gap can be seen in the 2nd from last pic - the dark space between those 2 pieces of wood. This is where the black paper is hanging down from. The 2x4 wall appears that it was not built directly against the foundation wall, but about an inch away from it...
The rim joist can get wet from condensation too, which will occur whenever the surface of the rim joist is below the dew point of the surrounding air. This commonly occurs in the winter, when the interior surface of the uninsulated rim joist will be just above the outdoor temperature, and that temperature ends up being below the dew point of the much warmer (and often more also mure humid) indoor air. Bulk water, such as splashing rain on the exterior, is a different issue, and not something you usually use insulation to solve.
Regarding the poly and batts, if the stackup is something like block wall/batts/poly/drywall, then you have what we sometimes call a "diaper wall", and the batts are prone to staying moist and growing mold in these assemblies. It's much better to insulation below grade walls with rigid foam between the foundation wall and the interior studwall (or just glue the drywall directly to the rigid foam). I would never use batts below grade like this.
Double check if that "black paper" isn't actually "moldy poly".
Bill
Thanks again for your reply Bill!
I have heard about the condensation on cold rim joist issue. I don't see evidence of any of that on my wood framing after decades of only the fiberglass insulation being there. Perhaps the fact that the fiberglass is "vapour open" allows the wood to dry out if any condensation actually occurs? Or maybe the rim joists don't actually get that cold?
I can't imagine bulk water hitting this area. The house is clad in brick, so the wood is simply not exposed to the outside elements. The grade / paving stones outside the house also directs rain water away from the house.
The black paper is definitely not "moldy poly". I found the same material hanging in my laundry room behind the plumbing pipes (see attachment). It's pretty thick and matte in finish - nothing like vapour barrier poly.
I do think the wall build is how you describe it however there appears to be a space between the wall and the batts where this black paper is located. Note that the basement doesn't have a musty smell like some basements do so I don't believe there is mold happening.
I'm not going to be demolishing the basement finishes and redoing it at this time (or ever), but would just like to make improvements where practical, such as any air leakage and insulation issues at the rim joists which the energy auditor mentioned. This area is accessible behind the drop ceiling so I won't need to demolish anything to do it.
You don't want vapor open insulation against the inside of the rim joist unless you have sufficient amounts of rigid foam on the exterior to ensure the interior side of the rim joist doesn't get down below the dew point of the indoor air. You may have been lucky so far, but it's safer to use a non-vapor permeable insulation here (rigid foam or spray foam).
That black paper is probably some kind of tar paper. It looks a lot like the fiber faced polyiso, which is a fiberglass mat facer. I wouldn't be surprised if that's in the gap between the framing and the brick veneer.
Bill
The house is 58 years old, so I guess that's 58 years of good luck :) Not bad! Not saying that cold joists that are open to the interior are good thing but perhaps they just don't quite get cold enough in this climate to cause condensation? Where are you located Bill?
The black paper is definitely between the framing and the foundation wall, which is either poured concrete or concrete block. No bricks below grade on this house.
It IS possible for the rim joist to avoid getting damp and moldy over time, but it IS a risk. Some climate zones are more or less prone to that. I'm in CZ5, outside Detroit. Mine has stayed dry too, but not in all places! Some joist bays showed some mold, others didn't. With rigid foam or (what I used), or spray foam, you're safe in ALL situations.
I'm not surprised it's tar paper. That was a sort of old school WRB. It's probably helping you in terms of dryness, but it's also probably very, very brittle to the point of being crumbly if you mess with it much. Yours does look to be in very good shape, but I'd still try not to move it around any more than absolutely necassary.
Bill
We are in a similar zone as I'm in Toronto.
When I get to work I'll find out if there are any joist bays with mold!
What I don't fully understand is how spray foam means that I'm safe in all situations. The spray foam makes sure that the wood doesn't become damp from the inside. But what about vapour or liquid water that may be coming from the other side, do we care about that at all or is that simply a separate problem to be managed at the outside? My foundation walls do not have exterior insulation and probably aren't well sealed against water or water vapour.
Interestingly, the paper isn't brittle or crumbly at all... But yeah I won't try to move it around.
With all these details now more clear, what do you make of the gap at the top of the wall assembly? This is the gap within which the tar paper hangs. Should that gap be sealed or best left vapour-open? It seems that if I use the comfortboard that it would cover the gap and allow vapour to emanate out. But if I sealed it completely, that any vapour could become trapped inside that pocket.
We're not trying to prevent moist air from coming into contact with the rim joist here, we're trying to prevent moist air *with a dew point above the temperature of the rim joist* from coming into contact with the rim joist. That usually means you don't want intdoor air coming into contact with the rim joist in the winter, since most of us are in heating dominated climates. Ultimately this all means if you insulated the interior side with vapor impermeable insulation you'll be OK. You could also insulate the exterior only, or the exterior with rigid foam and the interior with batts, or both sides with batts. You just need to keep the rim joist warm enough it doesn't become the first condensing surface for moist air, and you ideally want to allow some drying potential in at least one direction.
The easiest way to do things is usually using vapor impermeable insulation on the interior side of the rim joist. That can mean closed cell spray foam, or it can be some kind of rigid foam "foamed in" to hold it in place. Either way works, but spray foam is often less labor intensive to install.
I need more info on that gap to be able to tell you anything. Typical residential construction with brick is an interior framed wall and an air gap between the exterior of the framed wall and the the back side of the brick facade. There will be some metal straps to tie things together, but the air gap should be maintained. My first thought is that that's what you're seeing here, but I can't be certain from your pics.
Bill
Thanks again Bill!
I understand what you're saying about the dew point and temperature of the rim joist vs. temperature and RH% of the indoor air.
I've been reading up on spray foam technique for rim joists and came across a document (https://www.energystar.gov/sites/default/files/asset/document/BSC%20Information%20Sheet%20408%20Critical%20Seal%20%28Spray%20Foam%20at%20Rim%20Joist%29.pdf) that states "For air barrier purposes, spray foam must connect from foundation wall, up rim joist, and to floor
sheathing". This makes sense. The seal has to be complete otherwise any surface left exposed could be where condensation could still occur. Looking at my basement rim joist area, it's hard to see the foundation wall - I need to move the tar paper back and point my phone camera in there to see it. Without being able to freely access that joint, how would I be able to properly spray foam or foam board the jim joists?
Re: the gap in the wall... I did some more investigation and was able to pull back the tar paper enough to see what's behind it. Most of that gap is actually occupied by the concrete foundation wall protruding inward beyond the sill plate, so it doesn't seem that there is much of an air gap in fact. I found that there is a black plastic layer (gasket) between the top of the foundation wall and sill plate which I think is good news, but not sure what it means when it comes to my technique for insulating the rim joist. It's now pretty clear that my wall assembly (from inside to outside) is: drywall, clear poly, wood framing (I think filled with fiberglass batts), black tar paper, concrete wall. Accessing this area is super hard due to the finished wall going right up to the bottom edge of the joists. Hopefully this description and images is enough for you to provide some advice. Thanks!
I can't really see the "gasket", but it's probably some sort of sill seal, which is good -- that stuff usually makes a pretty good capillary break, which adds safety for your rim joist when you seal things up.
The spray foam would normally need to connect all the members that make up the air barrier of the home. There are drawings on here that show this, but basically you're trying to tie the inside wall of the crawlspace, the entirety of the rim joist, and the underside of the subfloor together. That's usually what is necassary to ensure a good air seal in that area. There are other ways to do it that will work, but you need to make sure there are no air leaks. In my own home, I foamed in EPS panels against the rim joist, which tie the subfloor, rimjoist, and sill plate together. I intentionally left the edge of the sill plate and the edge of the fiberboard piece under the sill plate exposed in some areas for drying, because I had no way to put a capillary break in some places. In other areas, the crawl space membrane wraps around and seals to the upper face of the sill plate. The exposed areas were intentionally left to aid drying, but they're further in from the exterior, so not as cold. It's a tradeoff there for me.
I think you have the usual finished wall that we recommend against here, which is fiberglass batts and poly. You appear to have a layer of tar paper between the back of the batts and the foundation wall, which could be helpful, but isn't a cure all. Rigid foam would be better here, but it sounds like you're stuck. My only concern is that sealing up the top of that gap MIGHT introduce moisture/mold issues behind those batts. Right now you have some air movement.
Bill
Thanks for staying with me here Bill!
This is a full 8' tall basement btw, not crawl space.
I don't think it'll be possible for me to seal right down to the concrete, since it's barely visible and basically inaccessible. Sounds like you left yours unsealed on purpose but I'd have to leave mine unsealed due to access. Either way is it OK to not seal this point?
Regarding the gap at the top of the wall. I measured 2" from the rim joist to the start of the gap. In other words, there's 2" of sill plate available. If the gap should be left open then I can put about 2" worth of insulation there while still keeping the gap open. Thoughts on that? What about using something vapour permeable like comfortboard as a second layer after foam board, or even just some batt insulation?
In the summer, the basement humidity goes up a fair bit. I have to run a dehumidifier to keep it down in the 50-55% range, otherwise it'd probably go up over 70%. In the winter I have the opposite problem... super dry.
Did a bit of googling and I think the black paper is "tar paper". See this video: https://www.youtube.com/watch?app=desktop&v=HpHblI_pp4I. Perhaps the tar paper is what's keeping my basement framing and insulation dry and mold-free?
Seems to me the easiest (although a bit tedious) & most effect approach would be ...
Get a 2" rigid, foil-faced poly iso board (R13)
Cut it to create a "baffle" with 1" space on all sides to fit into the space.
Buy a single component, closed cell than is minimally expanding (for windows & doors)
Put a bead of foam around/near the outside edge of the "baffle" to adhere this foamboard into the rim joist area (bead sticking to wood) - use a 1" wood shim at bottom if necessary to keep it in place ...
Let this harden & then go back & fill in with foam all around the 1" opening of the "baffle"
https://sprayman.co/products/sprayman-window-door-low-expansion-spray-foam
https://www.youtube.com/watch?v=Y7KrhGdPnmk
former spray/inject foam contractor VT
Thanks, I have definitely heard of this and similar approach and think I could definitely handle it. Would you caulk the gaps in the cavity before inserting the poly iso board?
What about the space at the top of the wall, would the board cover over that, and is there any concern with moisture being trapped inside that space?