rigid insulation on the exterior of a wall assembly?

Does anyone have experience detailing rigid insulation on the outside of an exterior wall assembly? If so, do you have a solution that locates the rigid outside of the sheathing? I see most of the details here (strategies and details) locate the rigid between the studs and the sheathing. This is a problem for our seismic zone and advanced framing.
Any advice or experience will help!
thanks!
GBA Detail Library
A collection of one thousand construction details organized by climate and house part
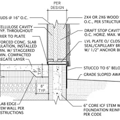
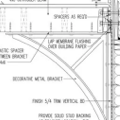
Replies
We have similar racking concerns due to the flying tree problem associated with hurricanes here in NC.
If you scroll down at this website there are some images that may help. In this particular case it is a pole barn dance studio with 1x8 vertical local poplar sheathing that was exposed to the interior and we went over it with foil faced polyisocyanurate foam and taped the joints and ran a rain screen over that of scrap OSB ripped to 3" and then the siding. the windows get built out w/treated wood and taped to the foam in this situation.
http://www.chandlerdesignbuild.com/files/PoleBarnOutbuildingsDetail.pdf
I'm one of those guys who doesn't believe rain screens need to be vented. In my world it's enough to break the capillary contact between the back of the siding and the front of the drainage plane. I seal off the top and bottom of the rain screen with something to prevent bugs from getting in there. This is controversial.
Assuming your house is OSB on studs for racking you would fur out the rough openings the depth of your foam with solid lumber over the OSB, run your drainage plane house wrap on that surface and install deeper trim to accommodate rain screen and siding. I've done it where I wrap the drainage plane out around (through) the rain screen blocking around the windows rather than use the thicker trim but I don't like the shelf that detail makes over the window.
I know this is not an entirely satisfactory response and wish I had some cool drawings for you but hopefully someone else will chime in.
m
Jennifer,
I have the same questions as you...I am looking for good details showing rigid insulation outboard of the structural sheathing.
My opinion is that the details here at the Green Building Advisor tend to show the rigid insulation in the WRONG location.
Lstiburek's concept of placing the rigid insulation outboard of the structure makes so much sense....
Why does this site promote details with the rigid insulation in the middle??
What is the logic here?
John
It seems to me that most of the wall section details here show the Lstiburek-approved foam on the exterior behind only a drainage plain and rain screen under the siding.
I'm interested in seeing more diversity as well as the site evolves to address the regional differences such as hurricanes and earthquakes and other things that don't concern New Englanders and I believe that is happening.
I'm pretty sure the only details that show foam inside of plywood or OSB sheathing are details with cedar shingle siding, in which case you need a solid backing for the shingles.
Most of the other wall sections either omit wood sheathing or place it inside the foam. Like Joe says to.
Dan
Dan & Michael,
I admire what you are doing here.
my apologies....I was basing my observation on just a few "free" details and Jennifer's comment.
I like this site and I will "dig deeper" and join the Pro account.
Michael, your detail here shows horizontal fir outs and that seems counter intuitive. Horizontal won't allow the rain to drain or the air to breath via stack effect behind the siding. The integrity of the exterior cladding seems to be diminished substantially and is compounded by using osb instead of solid wood- osb does not like to hold pooled water. Did I miss a page or is this your recommendation? I'm just trying out this site and want to make sure that the info I get is bullet proof.
I would like to see another detail showing 4"-6" of rigid exterior insulation. The big question is how to attach more than 2" to the studs or rafters/trusses and still be able to apply a fir out for a nailer. Thanks
Michael, having a horizontal rainscreen made of osb seems like a bad idea but I have no data. And for this cavity not venting that seems like a bad idea too, because to rely soley on diffusion seems like it would take a long time and the materials would stay moist longer. I'm not trying to dis I just want to make sure that I give my clients info that holds water, or in this case, doesn't hold water. Let me know what your colleagues think. I don't know if Im using this forum properly... I might have posted another similar answer..
Jim
I realize that the link I put up to my pole barn article is not entirely satisfactory. However, I do believe that wind driven rain penetrating through the siding tot he extent that it needs active bulk water (drip-path) drainage and active stack effect convection drying is extremely rare. The goal of a rain screen in my opinion is to provide first an area behind the siding that is pressure equalized by exterior wind pressure to balance the pressure differential across the siding so as to minimize the penetration of wind-driven rain through the siding and second to break the interstitial contact between the back of the siding and the face of the drainage plane to facilitate drying action after the storm has passed.
Paul Eldrenkamp expressed it very well in a letter Coastal Contractor magazine when he said "The fact is, if you have so much water getting behind your cladding that you really need significant "drainage," then you've probably got some serious issues that even the best-designed building envelope could have problems handling. A good exterior wall assembly, for the most part, needs to deal with only moderate amounts of water getting where it doesn't belong, and in my experience it deals with that water by giving it a chance to evaporate before the water does any real damage. It turns out water can take a pretty long time to evaporate before it does any damage, if I'm properly interpreting moisture meter readings I've taken over time on a range of projects we've done.
What seems more important than quick drying is even drying. A piece of wood that does not experience wide moisture variations within itself seems to hold a coat of paint much longer than if there's significant variation from one point to another. My experience indicates that the mere fact of a sizable air space behind your wood siding seems to be enough to ensure even drying — whether or not there's significant drainage allowed for (there's always going to be some drainage, planned or not) and whether or not it's vented. This is important because placing an unwarranted emphasis on drainage or on venting will add costs incommensurate with the benefit. I would be keenly interested (and, I have to admit, surprised) if anyone knows of a situation where wood siding failed because it was installed on an air space that was unvented and "undrained."
There are many areas in the building science conversation where consensus is still evolving. Rain screen back drainage and ventilation is one along with air exchanges between living spaces & sealed crawls, legionnaires disease & radiant floors, the taping schedule for sealed crawls, Flash and Batt vs exterior foam, open cell vs closed, the list goes on.
Our goal here is to give definitive information on a complex and evolving field by drawing on the resources of some of the best practitioners in the industry. You can count on us for that but you can also expect regional differences to lead to a variety of recommendations as the field evolves.
I'm speaking for myself here, not the official voice of GBA, for that you need to look to Dan or Peter.
Michael
Michael, et al:
What we're calling a "rainscreen" in low-rise residential applications is a completely different beast from the highly engineered pressure-equalized rainscreen (PERS) which was developed by the metal cladding industry for high-rise commercial buildings. A PERS requires a very open cladding with horizontal and vertical wind baffling to compartmentalize the air spaces for true pressure equalization.
The "rainscreen" that has become popular in residential applications is more properly called a "drainscreen". It does not offer significant pressure equalization, but rather a capillary break, a drainage plane, and an evaporative and convective drying capacity for both environmental moisture driven by wind, gravity, capillarity and solar radiation and interior moisture driven by temperature and vapor pressure differentials.
At a minimum, an effective drainscreen must have vertical furring, screened gravity drainage paths at the bottom and at all penetrations (with well integrated flashings and WRB). Ideally, it would also be open (screened) at the top to allow convective drying, particularly when the cladding is solar heated (which will drive adsorbed moisture inward, and even more importantly with "reservoir" claddings such as masonry or stucco.
As for Jennifer's question about exterior insulation outboard of the sheathing: this is the prefered location both for structural reasons and for the "warm sheathing" approach to controlling condensation at the sheathing plane. Ideally, in a heating-dominated climate, the exterior insulation will have enough vapor permeability to allow some drying to the outside and the WRB will be located outboard of the insulation to protect that part of the thermal envelope from environmental moisture and frost damage.
Jennifer, what appears in many of the GBA wall drawings on the outside of the rigid insulation is actually vertical furring strips for attachement of the siding, that also provides a 'drainscreen'. The sheating layer should be located between the rigid insulation and the studs. It appears that the sheathing layer is missing on many of the GBA wall details - a pretty radical departure from typical construction. What is providing the lateral strength in this wall? There are 1001 variations of siding & insulation thickness but no mention of what is replacing the structural sheathing. Perhaps the creator/reviewer/advisor of the these drawings can respond.
I can't speak to the details on this site, which I can't access, but I've built several superinsulated homes without exterior sheathing.
Outside of seismically-active or coastal wind zones, building codes allow either let-in wooden bracing or metal T-bracing (such as Simpson TWB). I've successfully used TWB bracing with siding applied directly over framing and polymeric WRB, as a resource-efficient building technique (with a modified Larsen Truss 12" thick wall system).
Details at http://www.builditsolar.com/Projects/SolarHomes/LarsenTruss/LarsenTruss.htm
Not an answer, but a further question - if plywood sheathing is necessary (I live in California) would a housewrap (tyvek, felt, what have you) be needed between the sheathing and the rigid foam? On the outside of the foam if it's foil-faced?
"if plywood sheathing is necessary...would a housewrap be needed between the sheathing and the rigid foam? On the outside of the foam if it's foil-faced?"
Several further questions would help answer this one. What comprisies the weather-resistant barrier (WRB) - foam board and tape? Is that sufficiently durable? How will the windows and flashings be integrated with that surface?
Is the WRB is intended to protect only the structure or the thermal envelope as well? If the latter, is the exterior foam part of the thermal envelope? Or is the exterior foam intented to protect the WRB?
From my perspective, the WRB is the second line of defense after the cladding and should be installed immediately under the cladding. That position also makes it easiest to integrate with windows and flashings. If exterior foam is used (I am not a proponent of it), it is part of the thermal envelope and its long-term integrity must also be protected by the WRB and cladding. The WRB should not be dependent upon tapes and adhesives or caulk for its integrity, as those are unlikely to be durable for the life of the structure. And, in a heating-dominated climate, the WRB and exterior "skin" of the structure should be sufficiently vapor permeable to allow drying to the outside (with potential for drying to the inside as well). The best position for the air barrier in a cold climate is inboard of the thermal envelope.
Robert,
You make some very good points. Your suggested location for the WRB seems to be at odds with Joe Lstiburek's "Guide to Insulating Sheathing"
http://www.google.com/search?sourceid=navclient&ie=UTF-8&rlz=1T4TSHB_enUS292US292&q=guide+to+insulating+sheathing
Joe's paper suggests that locating the WRB interior to the Insulating Sheathing is the more durable strategy.
I would love to read more comments from Robert and Joe concerning this subject.
Come on Joe...Is Robert right?
John points out that "Joe's paper suggests that locating the WRB interior to the Insulating Sheathing is the more durable strategy."
This highlights the paradox of using materials and methods of questionable integrity and durability. Does the housewrap (primary drainage plane) protect the thermal envelope (including exterior rigid foam) or is the foam necessary to protect the WRB from the very same threats which it is intended to protect the thermal envelope from? If this is the case, it seems that the WRB is not effective for its intended function or is rendered ineffective by the application method.
Applying rigid foam exterior to the primary drainage plane requires more problematic (and fallible) detailing, such as Joe's suggested poly flashing gaskets and mastic or tape, or flashings regletted into the surface of the foam.
Ironically, using "advanced" moisture-management techniques, such as the vented rainscreen, might put the WRB at risk of exposure to wind and consequent deflection and fastener tearout. And this might require protecting the WRB with rigid foam and making flashing integration with the WRB/drainage plane next to impossible - or relying on tapes and adhesives to turn the foam into a drainage plane.
It seems that in our quest for "ultimate" efficiency, we've forgotten the KISS principle and created more problems with each new "solution".
As Joe also says, "energy conservation has the potential to destroy more buildings than architects".
Jennifer, We are seeing increasing numbers of builders and architects designing both new and remodels with 2- 4 inches of rigid foam on the exterior of the envelope. Currently, they use HeadLok screws(fastenmaster.com) of suitable length to go through strapping,Typar, the 2-3 layers of rigid foam, through the sheathing and into the studs. They space the furring pretty close together because they are frequently hanging fiber cement siding or panels on the furring. Hope this helps, the HeadLoks are available at your local lumberyard. You can use spikes or other type screws but these HeadLoks are excellent for this task. Email me your address and I will show send you some architectural details and phots of this particular application.
Brice,
The Headlock screws, which don't countersink, might be nice for preventing strapping from splitting, but how do you keep a uniform siding plane over all those screw heads?
Also, FastenMaster specs those screws for minimum 1-1/2" thickness lumber and spacing at least 1-3/4" from edges. It seems using those for strapping is using them outside of their intended function.