Rigid insulation and fiberglass batts in a wall cavity

I recently completed a full renovation of one bedroom in our home located in Central PA. When I had the room completely gutted i found that the house had been framed with rough cut (true) 2×4 studs. Because I had a full four inch cavity my father in law suggested that I install a layer of 1/2″ blue board against the exterior sheathing for additional r-value and then install 3 1/2″ fiberglass insulation. I followed his suggestion and closed the wall with 5/8″ drywall. I just recently came across some information that has me now questioning whether or not this was a wise idea as the rigid insulation may act as a vapor barrier and allow condensation to collect inside the wall cavity.
I am worried that I may have moisture build up within the walls. Is my concern legitimate or am I worrying for nothing. If it is a potential issue, is there a minimally invasive way to go about checking the wall cavity such as probing the cavity with a moisture meter?
Any comments or advice would be greatly appreciated.
Thanks in advance.
GBA Detail Library
A collection of one thousand construction details organized by climate and house part
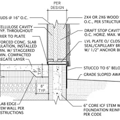
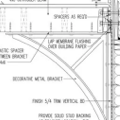
Replies
Austen,
The vapor permeance of 1/2 inch of XPS varies by brand, but it is probably about 2 perms. That's not very permeable, but it's not a total vapor barrier.
I think that your wall will probably be OK, especially if you took steps to make sure that the drywall layer was as airtight as possible (ideally, using airtight electrical boxes). If your drywall layer is leaky, do what you can to tighten it up; these steps will lower the risk.
In general, if you want to install rigid foam on the exterior side of fluffy insulation, thicker foam is safer than thinner foam. Don't do this again.
The sheathing will still be able to dry toward the interior. The only moisture issue would be how much accumulates at the foam/fiber boundary over the course of a winter. In climate zone 4 having R2.5 foam on the exterior side of R13-15 fiber would be sufficient dew point control, per the IRC chapter 7 prescriptives:
http://publicecodes.cyberregs.com/icod/irc/2012/icod_irc_2012_7_sec002_par025.htm
Central PA is zone 5 or zone 6, so it's not exactly ideal, but since neither the fiberglass nor the foam is damaged by moisture, and neither are particularly good mold-food you'll probably be just fine.
Homes that were built with full-dimension 2x4s are typically sheathed with planking, with a lightweight asphalted felt or rosin paper between the planks & siding. These stackups allow a decent amount of drying toward the exterior as well, even with the 1/2" foam- even more drying capacity than 1/2" OSB would, since 1/2" XPS + planking together are still more vapor permeable than 1/2" OSB (!).
If you installed any sort of vapor retarder (even kraft facers on batts), the vapor retarder will limit the rate of wintertime moisture accumulation (assuming it's reasonably air-tight toward the interior.)
If you have reasonable roof overhangs to limit rain wetting of the siding & sheathing, that too is big plus for the overall resilience. Bottom line- it's going to be OK, despite being sub-optimal.
The additional R-value of the half-inch foam is really negligible, but it may have improved the air tightness, assuming you caulked or can-foamed the edges to the framing, which is worth it. Compressing an R19 - R23 batt designed for 2x6 framing into that cavity or filling it fully with cellulose would deliver about the same R-performance, but not the same air tightness as what you did. Batt widths are also designed for 14-1/2" wide cavities, not the 14" you get with full dimension studs 16" o.c. but as long as they don't buckle from the excess side compression forming thin spots it's OK. (That's another reason to use oversized 2x6 batts , to guarantee a compression fit with minimal voids.)