Rigid foam vs. mineral wool in a exterior retrofit

I’ve been reading GBA and FHB articles on how best to retrofit exterior insulation on a wood-frame addition of my otherwise brick and block 1950s ranch. There seems to be some debate about whether or not an exterior layer of insulation should be vapor permeable. I’m debating between the two but leaning toward rigid foam as it seems a bit simpler to construct.
My situation:
I am in zone 5 although I hope to install R10 or more of additional insulation. Framing is 2×4. There is currently no vapor barrier. The existing construction from inside to out is: Drywall, faced fiberglass batts, tar paper, sheathing, house wrap (I think), siding.
My questions:
1) Since there is currently no vapor barrier, my initial thought is rigid foam would be the better approach since I would be both insulating and creating a vapor barrier (while also not creating a moisture trap). Is this a fair assumption?
2) If rock wool panels are preferred over rigid foam A) how (and where) do I then create a vapor barrier since none currently exists? (keeping in mind I do not want to touch the interior drywall) B) where in the heck would I buy these rock wool panels? and C) Are they cost-competitive with EPS or XPS?
3) A friend of mine suggested that the greenest (and easiest) approach would be to keep the entire wall assembly intact (eliminating a landfill-bound dumpster of siding, sheathing, & fiberglass batts). He suggested I simply apply rigid foam over the existing siding (which is sound although weather worn) and then side over that. The existing siding is ~inch thick vertical tongue & groove pine which I suspect would also make it easier to install the rigid foam and new siding. Keeping that siding would mean that my screws will still have a good grip even if I miss a stud. The siding is also essentially flat save for the small vertical indentations where the tongue meets groove. So this leads me to my final question – given the current construction of the walls (noted above), is there any merit to the idea of not touching any of the current wall assembly and simply applying a thick layer of rigid foam over the whole lot, adding vertical furring strips as a rain screen/siding nailer, and finally siding?
Lastly, the new siding will be Hardieboard cement siding.
Thank you,
Brian
GBA Detail Library
A collection of one thousand construction details organized by climate and house part
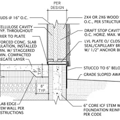
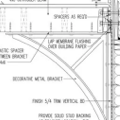
Replies
Brian,
Q. "Since there is currently no vapor barrier, my initial thought is rigid foam would be the better approach since I would be both insulating and creating a vapor barrier (while also not creating a moisture trap). Is this a fair assumption?"
A. Forget about vapor barriers. You don't need a vapor barrier. What you need is an air barrier (attention to air tightness). You also need to make sure that your rigid foam is thick enough to keep the wall sheathing above the dew point in winter. Here is more information on that topic: Calculating the Minimum Thickness of Rigid Foam Sheathing.
Q. "If rock wool panels are preferred over rigid foam, how (and where) do I then create a vapor barrier since none currently exists?"
A. I'm not sure whether mineral wool is preferable. In any case, you don't need a vapor barrier. For more information, see Do I Need a Vapor Retarder?
Q. "Where in the heck would I buy these rock wool panels?"
A. Start with your local big-box store. You can also contact Roxul (800-265-6878) and ask about distribution in your area.
Q. "Are they cost-competitive with EPS or XPS?"
A. For a small residential job -- usually not.
Q. "Is there any merit to the idea of not touching any of the current wall assembly and simply applying a thick layer of rigid foam over the whole lot, adding vertical furring strips as a rain screen/siding nailer, and finally siding?"
A. Yes, that approach has merit. Whatever you do, pay attention to water management issues and flashing issues. For more information, see How to Install Rigid Foam Sheathing.
Mr. Gray,
A couple thoughts...
In general, I have a strong aversion to "abandoning in place". (Once, when inspecting above a 7' high ceiling grid in an old hospital, I found most of two previous ceilings and remnants of two previous HVAC systems. Ugh. How can anyone perform maintenance- or provide good workmanship in such a location? But at least it explained the 7' ceiling.)
My point is that it would drive me nuts to go over existing siding... usually. But you're not talking about aluminum siding over asphalt shingles that are supposed to look like bricks (what do they call that?) over lap siding. (Oops, once again, I've digressed into MY issues.) You're talking about flat, solid, intact T&G over perfectly good sheathing, right?
Removing it adds lots of demolition labor, puts materials in a landfill, requires more new materials (new sheathing), and requires more installation labor (again, the new sheathing). Come to think of it, the T&G is probably good for about R-1, so all that additional work and expense would LOSE a little bit of insulation. And what's the upside? Access to the stud bays? You said the stud bays already have insulation, right? I know what I would do.
As a source for mineral wool boards, you might try General Insulation. They are a distributor of mineral wool products (among other things), and have a lot of locations. They'll have wider product offerings than a big-box store, but also be more willing to talk with a homeowner than a manufacturer will. Full disclosure: I've bought from them, and have a friend who manages one of their locations, but I have no financial interest in this company.
Good luck,
Ben