Rigid foam on the outside – worth it?

I’ve got quite the opportunity to improve my home’s energy efficiency as we need to replace both our siding and our windows which are both original to the house. We had a mild winter here in the northeast this year and our propane usage was way too high. The new windows will be vinyl double pane low-e replacing windows original to the house which were simply popped in without insulation or any regard to energy use. Here are the details of the existing construction, and then some of the struggles I am facing with the different options which are out there.
– 2 story 1800 sqft colonial
– built in 1971
– Coastal Connecticut “zone 5A” climate
– 2×4 construction
– fiberglass insulation was installed during construction, just basic R11
– No plastic mill vapor barrier
– No tyvek on outside
– Entire interior was painted in a moisture barrier shellac (Zinsser shellac primer qualifies as a 0.4 perm) due to the previous owner being a very heavy smoker
– black board/buffalo board/celotex .5 inch exterior sheathing. Plywood at the corners.
Here are my options as I have researched …
Rigid foam on the outside
– Found out that in my climate zone I need at least an R-value of 5 on the outside wall to prevent moisture build up during the winter from condensation. I was thinking of the blue of pink rigid foam as this gets my the 5 r-value in 1 inch. I can’t really go more than that because of cost anyways. However, because both side of the wall now essentially have vapor barrier, will there be rot issues? There doesn’t seem to be a concise decision on this topic as I hunt through the forums and blogs. I would prefer not to install a rain screen as the siding manufacturer prefers a solid surface (also a touchy subject on the forums I see).
Cellulose inside the walls
– Since the siding will be off, put holes in the sheathing and pump the wall with as much cellulose as I possibly can. Is this even possible with existing fiberglass? Fix sheathing holes with spray foam, replace windows, cover in tyvek, put on vinyl siding. No moisture issues from what I can tell but not as tight of an envelope.
– Flash & Batt
-Take down the black board exterior sheathing, remove 40 year old fiberglass, spayfoam the sheetrock, to airseal and vapor barrier, add new fiberglass insulation, replace with OSB/plywood, replace windows, tyvek, then vinyl siding. Most costly solution I think.
Do minimal work
– taking down siding, add tyvek, replace windows, vinyl siding (this is what our town inspector recommended as his thoughts are that the lack of tyvek is really the issue…I’m not really convinced of that)
I would like some experienced thoughts to figure out a cost/benefit/time analysis of doing this work, but also what is going to be the best solution in terms of vapor and moisture issues. A sticking point is the exterior sheathing also, If I do foam on the outside, I will have to be sure I always nail the vinyl on a stud, as the black board stuff doesn’t hold a nail very well. Makes me wonder however if my current cedar shake held up for 40 years this way, why can’t some vinyl siding right ?
Thoughts and assistance as much appreciated, thank you in advance for your help and apologies for the lengthy post…trying to get as much detail as possible.
GBA Detail Library
A collection of one thousand construction details organized by climate and house part
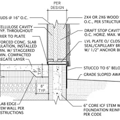
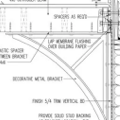
Replies
Paul,
I would install a layer of exterior rigid foam; polyisocyanurate is more environmentally friendly (and has a higher R-value per inch) than XPS.
Pay attention to air sealing. Don't worry about a "double vapor barrier" -- you don't have interior polyethylene, which is a good thing. The shellac is more of a vapor retarder, not a true vapor barrier.