Rigid foam on exterior walls.

I’m presently designing a new home for living in a very cold climte. I had thought that the use of exterior rigid foam would be a good way to boost wall performance but I am no longer so sure. Using the method described in “Robust Walls” and an outdoor design temp of -29 deg F to caculate an estimated interface teperature between exterior foam and structural sheathing it seems pointless to consider using interior cavity insulation at all. A 2×4 wall with R-13 cavity insulation requires 8 inches of exterior foam simply to achieve an interface temperature barely above dew point when the interior is at 70 deg F and 35% RH… To embrace a technique like the PERSIST model is something I am unwilling to do for various reasons. My question is: why is there no discussion of foam sheathing on the interior side of conventionaly framed walls? It seems to me that tightly sealed foam interior sheathing in conjunction with a conventional vapor barrier would serve as an even better moisture barrier than vapor barrier alone while still allowing the wall to dry to the outside. It seems there are plenty of drawings detailing this method for vented cathedral ceilings but the same drawings always show the supporting exterior wall with the foam moved to the outside… Am I missing something? Help in understanding greatly appreciated.
GBA Detail Library
A collection of one thousand construction details organized by climate and house part
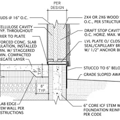
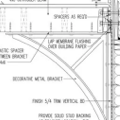
Replies
Lucas,
Plenty of people have done what you propose. I have built several houses with interior foam.
The big drawback is solving the problem of heat loss at the rim joists, as well as intersecting partition walls. With interior foam, you'll never solve the thermal bridge problem as well as you will with exterior foam.
I'm not sure what your source of information is concerning the thickness of exterior foam for climates with a design temperature of -29°F. Here in northern Vermont, we occasionally see -40°F, and we don't need 8 inches of exterior foam. (Of course, 8 inches would be good.) Plenty of people have built walls with 2 in. of exterior polyiso (about R-13 of foam) coupled with 2x6 walls filled with R-19 or R-20 of cellulose. If you choose 2x4 framing, you end up with about R-13 in the walls -- a little light in my book. If you want to frame with 2x4s, why not go with 2 layers of 2-in.-thick polyiso -- about R-26 of foam and R-13 of cavity insulation?
Thanks for your input Martin. Actualy my preferred method of construction would rely on 2x6 framing on 24" centres with dense pack cellulose in the cavities. I had planned to use exterior foam over that but after reading some the articles here at GBA and "Robust Walls" by Ted Cushman, I became concerned that potential moisture problems might occur within such a structure. I used the method in "Robust Walls" to try to figure out how much foam would be required to create the "warm wall" that dries to the inside. It seems that with such a cold outdoor design temp, increasing interior cavity insulation actualy works against creating such a warm wall... ie more exterior foam is required to prevent the dew point temp penetratrating to the structural parts of the wall. The way I calculated it I'd have to go with 8 inches of exterior foam to keep a (meager) R-13 2x4 wall warm enough to dry to the inside... Is this correct? If I were to build a 2x6 r-20 wall with 2 inch XPS exterior foam sheathing and interior (warm-side) vapor barrier how concerned should I be that the wall won't dry properly given inevitable moisture infiltration?
Lucas,
You're correct. At -29°F out and 70°/35% indoors, you would need more than 6" of XPS with R-13 to keep the sheathing above the dew point.
You could use absurdly-thick exterior foam, or interior foam as you're considering, with all the thermal bridge and electrical outlet problems. Or you could build a modified Larsen Truss wall system with air-tight drywall interior with one perm vapor retarder paint as the air/vapor barrier, eliminating almost all thermal bridging, and using a highly breathable exterior skin to maximize drying to the exterior without completely eliminating drying to the interior.
The integrity of the interior air barrier and indoor relative humidity control are far more important than a vapor barrier. Cellulose manufactures discourage the use of polyethylene vapor barriers (some won't guarantee their product if a vb is used). Eliminating thermal bridges and optimizing the whole wall R-value are easier with a double-frame envelope with interior load-bearing walls than by using excessive depths of foam board. And a cellulose insulated envelope is more tolerant of occassional moisture than a sealed envelope with little hygroscopic potential.
If you'd like more infomation on this system, contact me at HouseWright at Ponds-Edge dot net.
Lucas and Robert,
I've seen a lot of different calculation methods and rules of thumb for determining minimum rigid foam thickness. Right now I'm looking at a chart I copied a while back — darn, I forgot to note the source — that shows the minimum ratio between exterior rigid foam sheathing R-values and cavity R-values.
The ratio increases as heating-degree days increase. For locations with HDD between 8,000 and 8,999 — that's pretty cold, since St. Johnsbury, Vermont has 7,882 HDD — the chart shows a minimum ratio of 0.50. So if your cavity insulation is R-13, your rigid foam must be at least R-6.5. That's just one inch of polyiso.
Every such chart or rule of thumb needs to be balanced by experience and common sense. From my experience, homes in cold sections of Vermont with 2x4 framing filled with cavity insulation will do fine with exterior sheathing rated at R-6.5 or more.
Perhaps the discrepancy comes from Lucas's unreasonable threshold -- his idea that during the coldest night of the year -- evidently -29°F where he lives -- he wants to be absolutely sure than not a single molecule of water vapor will condense against his sheathing. But who said that threshold is reasonable? As building scientists always tell us, it isn't necessary to design a wall that never experiences wetting. What we need to do is design a wall that has a drying rate that is significantly greater than its rate of wetting.
A little condensation won't hurt a wall (or a roof assembly) as long as the wall or roof dries faster than it gets wet.
Martin,
It would be helpful if Lucas would let us know where he lives and what the HDD are. But if the design minimum temperature is -29, that's the 97.5 percentile coldest temperature not the coldest day and that's the basis upon which the design heat load would be calculated and the heating system sized. The HDD for Montpelier VT is 8500 and the design minimum temperature is about 0°. So a climate with a design minimum of -29 is a much colder climate than in northern VT.
But, if Lucus used Cushman's formula from Robust Walls (which is actually Lstiburek's formula), then his design temperature of -29 is the average temperature for the three coldest months (well above the design minimum). Which means he must be in something colder than a 12,000 HDD climate.
If this is the case, then Lucas is looking at normal winter weather not weather extremes. If his normal winter weather is -29°, then it's true he would need R-35 exterior foam to keep an R-13 wall sheathing above the 41° dewpoint for a 70° 35% RH indoor environment.
Seven inches of XPS would have a perm of 0.157 and would not allow drying to the exterior. If, as Lstiburek suggests for very cold climates, he also uses a kraft-paper vapor retarder on the interior, then drying to the interior would also be somewhat limited.
The problem I have with all the "outsulation" approaches (as well as the use of plastic foam or plastics anywhere in the thermal envelope) is that they are antithetical to natural law. Durability in natural ecosystems requires resilience - the ability to respond to challenges flexibly. Rigidity is a liability and leads to catastrophic collapse. The more we hermetically seal our homes against the intrusions of nature (wind, moisture, heat, cold), the more rigid they become in their ability to respond to challenges.
Unfortunately, because we've nearly used up our stores of cheap "ancient sunlight' and have nearly destroyed our nest by their profligate use, and because we demand every higher levels of comfort, we are forced to superinsulate our homes against temperature fluctuations. But we can do that with resilient systems, using natural materials (such as wood and cellulose) or with rigid systems (such as petrochemical products that never existed in the natural world until very recently and will soon have no place in it again).
I live along the North West shore of Lake Superior in Ontario. HDD for my area are 10400. Robert you are correct that the -29F is the design minimum temperature which I (mistakenly) used in Cushman's/Lstiburek's formula. Using the average temperature for the three coldest months (8.9F) it seems I need 4 inches XPS to keep that r-13 wall warm enough to stay dry on that average winter night. A 2x6 wall apparently needs to have about 6 inches of XPS.
My problem with these predictions is that they seem to say that with anything less than that much outsulation, condensation will occur within the structural parts of the wall with nowhere for it go. Not enough foam to create the warm dry wall with no interior vapor barrier, but too much foam to allow the wall to effectively dry to the outside. Having a wall that dries more quickly than it gets wet sounds exactly like what I'm looking for I'm just not sure that's possible with exterior foam sheathing. Am I off base?
I should say that I am going to be building this house myself and so I must stick to construction methods that are logistically practical for the region I live in. XPS in 2 inch sheets is expensive enough and I'm not even sure if I can get polyiso without a special order. Demand for building supplies are for the most part driven by builder's who tend to follow a pretty standard model. With this in mind, maybe some type of Larsen truss system is the best way to go.
Lucas... two builders around my parts build with sheet foam and no fiberglass in the studs. They both do so as not to have moisture issues. They also feel the sheet foam is plenty of insulation since it is continuous R... They put it on in two layers, taping the seems... they are using the foil faced insulations. I think 3-4" on the walls and 4" on the roof.
Check out this website... I have been in two of his designs... both homes were very comfortable... super nice homes.
http://www.aaepassivesolar.com/
aj