Rigid Foam in between studs

I live and work in south-central Tennessee and Northern Alabama (Zone 3A). I am working on a wall insulation design for a group of houses that my company will build. We are going to manufacture the walls in our facility before they go to the site. We would like to build a standard stick frame (2×4 studs with sheathing). We would tape every seam on the outside and caulk seams on the inside. Between the studs, we are planning on installing rigid foam board instead of spray foam—we can make a very tight fit because of our jig. On the outside we will add 2” of rigid foam. That would bring the R value to around 35 at a much cheaper cost than spray foam, and I think our walls will be comparably tight and still be structurally strong.
In south-central Tennessee, the winters have a few nights in the teens, but the temperature never stays below freezing for very long. We have very hot and humid summers, and I want to make sure that moisture doesn’t collect in the walls. Having a vapor barrier on the outside of the sheathing, but inside of the exterior foam seems like it would keep moisture out in the summer when it is trying to come in. On the other hand, with 2” of foam on the outside, I can’t see the dewpoint causing moisture to develop on the inside of the walls during the winter. If we make the walls very tight (as we can with the jig) and seal them better than can be done on a jobsite, I am wondering if the moisture problem would still be an issue. I am also wondering if an additional vapor barrier is a good idea with foam at all. Maybe there is a better way on a similar budget.
Any input is appreciated. Thanks.
GBA Detail Library
A collection of one thousand construction details organized by climate and house part
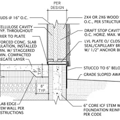
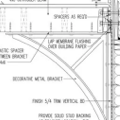
Replies
Is there any way you can put all of the foam on the outside? Seems like you'd save on labor by eliminating the caulking and foam fitting. Not to mention the easy of running electrical and plumbing through empty bays.
Yes. I suppose we could, but the walls would then be 10" instead of 6". I was trying to conform to traditional sizes on doors and windows. But you're right, it might be simpler that way.
In that case could you stick with your plan but replace the sheathing with other bracing?
I love that concept about different bracing. The sheathing--I think--is the whole problem with regard to moisture. One of my goals is to have a wall that can be used to support second stories and roof load points. What could I use to replace the sheathing to keep the rigidity of the walls?
What kind of siding were you going to go with? I recall a riversong truss that used the siding for sheer bracing in addition to some sort interior corner steel cable bracing. You could space the siding away from the studs for a rain screen. Then put a your continuous layer of foam board on the interior of the wall assembly in addition to the foam between the studs. Then strapping, then Sheetrock. Mount your electrical boxes to the strapping. Disclaimer; I am not a pro. Just a thinker. Go with a steel roof to keep it light and easy to transport.
That may be a good model. I'll have to study how to reinforce the walls. What you're suggesting does eliminate that "sandwich effect on the sheathing, which I think is smart. Thanks.
Bradley, cooling climate, A.C., your posted idea and all the rest are IMO no go. If you are prefabbing walls, if you desire in wall foam, I would set up to spray it. Caulk is almost a worthless product that has limited lifespan. But standard construction is another option; using permeable insulation like batts or Spider at site, and using your exterior rigid foam. There are hundreds of prefab companies. If it were me, I would visit a few and use the best ideas of all and add to it.
AJ, why do you think using foam in general a no go? Spray foam in our area is more expensive than the average consumer is willing to pay. Don't get me wrong, it sells, but only to higher-end buyers. I would like to make homes for average buyers more energy efficient. I've used batts and BIBs (like Spider), but never rigid foam. Is the moisture content the issue in your mind, or the labor-intensive process, or something else? Thanks for the input.
Rigid foam's failure point among many is the fact that we assemble it in pieces. Using rigid between studs is the worst case scenario. The frame shrinks, swells, moves. The caulk ages. Air moves past the foam and transports moisture. Moisture is absorbed faster than it is expelled. The stink starts. Your phone then rings. Then your lawyer asks you to write a retainer check for $5,000 but also suuggests settling will in fact be the least expensive way out. Quickly you take in three more down payments, after establishing residency in Panama, you declare bankruptcy.
Haha. Point well taken. I've read some success stories too, though I am not sure of the method of moisture prevention. My productivity goes up with this assembly, and I would like to look for alternatives to spray foam (or 10 inch walls). Good input.