Rigid Insulation + Existing Cedar Siding (Medium Depth Retrofit)

Good morning GBA, I’ve got some questions for y’all.
Our summer project(s) this year has been a medium-depth retrofit on our two story house built in 1900. Prior to us, this house had always been kept in the original builders family/descendants. As a result, there are some peculiar design decisions and interesting craftman…ship.
From outside to inside our wall structure consists of asbestos cement siding, asphalt felt, cedar lap (painted with lead paint!), 1×12 rough boards for sheathing (pine?), 2×4 dimensional studs and then lathe and plaster for the interior walls. You read that right, there’s not a lick of insulation on most exterior walls.
Now as it would happen, we stumbled into a couple very good deals on new siding (LP smart side), 4″ polyiso in 4×4 squares, barricade house wrap and various window upgrades/replacements to handle all the rough openings we want to keep. We’ve also managed to remove all of the asbestos cement siding and dispose of it according to the DNR’s guidelines.
Here’s where we’ve hit an unexpected fork in the road – the cedar siding under the cement shingles is in pretty good condition. Actually, astonishingly good condition. The combination of zero insulation + hygroscopic pre-WW2 plaster has meant that any water that made its way behind the cement siding to the cedar (or even back to sheathing) was routinely dried out from unintended airflow x stack effect x relative humidity differences. . We’ve wintered here a few times and it’s *so* dry inside the house in the winter, the only damage to the cedar + rough sheathing that we’ve seen is obvious flashing failures.
So here’s our question – can we replace the asphalt felt with house wrap and put the 4″ polyiso squares over the existing cedar lap? Originally we’d planned to remove the cedar and put up OSB over the rough sheathing, but reading more and more on BSC (and more and more and more and more) gives me qualms about OSB (I do not trust we could install it well enough to avoid potential water issues). Further, *not* removing the cedar means we don’t have to deal with the lead dust hazards (we’re replacing the soil but still) and we don’t have to buy purchase OSB (which is a ~$2k expense we’d be happy to put towards other house projects).
The downsides as I see it are A. not having a clear look at the sheathing for any damage, B. getting a proper seal on the housewrap would be a bit more difficult and C. if for some reason future owners redo the exterior wall structure they’ll want to stab us for leaving leaded paint in the structure.
Am I missing anything? Our polyiso is felt faced, and my understanding is it’s impermeable to pretty much everything, whatever is towards the inside would also be drying that way, and the lathe and plaster should dry whatever condensation we get during the summer time. We had planned on doing outtie windows (I miss having deep window sills), and caulking + taping both sides of the 4×4 polyiso squares.
E: Climate zone 6A
GBA Detail Library
A collection of one thousand construction details organized by climate and house part
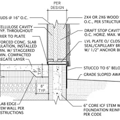
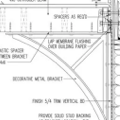
Replies
Hi John,
I surprised no one has given you any guidance on this one. Let me give you a bump. Also... Are you planning to add any insulation inside the walls? How are you dealing with detailing the foam at the top and bottom?
@Steve Knapp
Appreciate the bump.
Insulating the stud bays isn't likely to happen till next year, and then only once we replace the various electrical piecemeal wiring. To our surprise, *some* of the bays have blow in cellulose, but it wasn't the most precise job and most of the insulation has settled in the bottom of the bays. From what I understand, this tends to happen when cellulose gets wet, and that indicates some amount of persistent condensation on the interior of the sheathing. This would happen during the winter months, if I'm understanding the science correctly.
Anyway, exterior rigid insulation *should* clearup that problem, and provide enough vapor permeability that should the sheathing get wet from water penetration, the dry winter air will pull out the moisture (without adding any condensation since the sheathing will be warm enough to prevent that).
Regarding detailing... after reading more it looks like having the WRB on the exterior of the insulation will be the right fit for us. We're not touching the roof, but there's not really a good way to fix the roofs problems without blowing it all up; the soffits aren't vented at all, but the attic itself is vented... yeah it's a mess. For now we're planning on cutting the insulation to match the slope of the current soffit and flash+caulk the junction. Figure behind the frieze board and under the soffit itself shouldn't see much water penetration.
Also reading up more on the rough boards we have, we might remove the cedar (so we don't have an air gap that eventually turns into air ways for perpetual leakage) wrap boards in asphalt felt, then put rigid over that with barricade house wrap on top. Furring strips will be diagonal (to reinforce the horizontal rough cut boards) and the outtie windows will be integrated with the WRB on the exterior of the insulation. Detailing the bottom edge of the insulation, we'll want an insect guard along the bottom with some metal flashing (similar to z flashing?) with a line of tape making sure whatever moisture gets behind the cladding flows down the WRB->tape->custom z-flashing->drip onto the ground.
I appreciate the follow up!
John,
This discussion should be helpful: https://www.greenbuildingadvisor.com/article/how-to-seal-sheathing-boards.
If it were my house, I would remove the shingles.
That appears to be the consensus, from here and others I've talked to.
Are there any tricks to getting a good seal between the polysio and rough boards? The insulation is fiberglass backed, and the suggestions I've seen for bonding rigid insulation to non-uniform surfaces all seem to be applied directly to unfaced foam sheets. The cut-and-cobble discussion mentioned Dow INSTA STIK™ Quik Set Commercial Roofing Adhesive, but I'm uncertain if there's a tangible benefit to applying a varying depth 'squishy' bonding foam between the sheathing and foam boards vs relying on the pressure from the 5" screws + furring strips to maintain a tight seal against the boards.
Related to keeping a tight seal [I]I've been told[/I] that polyiso boards will sometimes pull away from each other at the seams after many hot + cold cycles if there's a wide range. I've experienced both 97° and -35° in the past five years in my neck of the woods, is it recommended to caulk between the seams (eg as mustard on a sandwich) to help prevent that? Or is that just creating another variable and possibly problems down the line?
Thanks again for your help.
No need to use any adhesive between the iso and the sheathing. Your air seal is at the housewrap layer. There might be some advantage to a layer of felt, though. It would act as a bit of an air/vapor retarder. your stackup has some risk of condensation on the back of the tape across the foam edges - meaning there WILL BE some condensation there. It will form frost/ice over the winter, and drain out the bottom of the wall when things warm up. If your bottom detailing allows for that, it may not be a giant issue. Felt would help control that, but not eliminate it. Using low-rise canned foam in the gaps might help more, but if the iso shrinks enough, the foam won't stretch enough to stay stuck in the gaps. This is one of the reasons most sites recommend two layers of foam with staggered seams - it slows the migration of vapor towards the exterior. If you have the time and diligence, I'd recommend leaving 1/4" gap between the foam pieces so that you can get the canned foam straw all the way in, and try to fill the gaps with canned foam. Also, use a very aggressive tape that will stick to the FG facers forever.
Peter, thanks for your response.
Regarding frost/ice on the back of the taped foamed seams - would taping both sides of the seams help or is that simply too impractical? What your suggesting reminded me of this FHB article about SIPs https://www.finehomebuilding.com/2014/09/10/air-sealing-sip-seams and specifically this picture - https://www.finehomebuilding.com/app/uploads/cms/uploadedimages/fine_homebuilding/articles/246/021246088-seal-the-panel-seams_xlg.jpg . I can't find a good argument [I]against[/I] felt between the polyiso and the sheathing and it's cheap for the retarding/wicking action it'll provide.
We can manage 1/4" gaps to foam in, I'd rather have it done right than have it done fast.