Revisiting a wall in Climate Zone 5A

Construction is on the horizon in our “pretty good house” in Iowa, Climate zone 5A.
Although I know our wall isn’t perfect, we have chosen the materials for a variety of reasons. Currently from exterior to interior we have:
-Hardi-plank siding
-1×4 furring strips for rain screen
-Tyvek WRB
-2″ rigid insulation, currently XPS
-Sheathing, currently OSB, taped
-2×6 framing, open cell spray foam in cavity
-drywall, with latex paint
My questions after reading and re-reading the prevailing thoughts on this site are:
1. Would I be better served with plywood (or some other sheathing) to avoid moisture issues in sheathing?
2. Would switching to EPS buy me enough permeability to help OSB dry?
3. What other recommendations do you have? (apart from the standard ones made by commenters that are significant departures from this wall assembly like “double stud is the only way to go”, “do only exterior insulation”, or “scrap the entire project and start over”)
Thank you.
GBA Detail Library
A collection of one thousand construction details organized by climate and house part
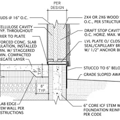
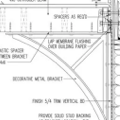
Replies
Thomas,
If you haven't started construction or ordered materials yet, I assume that you can still make changes.
If you can't make changes easily, relax. Your wall is fine (from a moisture and performance standpoint).
You don't have to make any changes to help the OSB dry, because 2 inches of rigid foam is enough insulation in your climate zone to keep the OSB warm and dry all winter. As I said, relax.
Whether or not the upgrade from OSB to plywood is worth it is a judgment call. The 2 inches of rigid foam goes a long ways toward making sure that the OSB should last a very long time. OSB that is protected with an adequate thickness of exterior rigid foam is much less risky, and is likely to last much longer, than OSB that lacks exterior rigid foam.
If you read more here on GBA, you'll discover that most green builders try to avoid the use of XPS, because XPS is manufactured with a blowing agent that has a high global warming potential. So either EPS or polyiso is a greener choice.
For more information on these topics, see:
Calculating the Minimum Thickness of Rigid Foam Sheathing
Choosing Rigid Foam
Wall Sheathing Options
How to Design a Wall
In 50 years the 2" XPS is going to perform about as well as 2" EPS. If you instead of XPS you went with 2" graphite loaded EPS the initial R would be about R1 less, but in 50 years it would higher.
At 2" 1.5lb density EPS (grahite load or other) would run about 1.2-1.5 perms, which is the tight end of Class-III vapor retardency. That's an acceptable amount of drying capacity into the rainscreen even if the interior side was vapor tight. But in your stackup the 3-5 perm interior latex paint and the warmer sheathing temp are high enough that it doesn't much matter. With 2" XPS you'd be looking at 0.5-0.7 perms, with very little drying capacity toward the exterior, but still some. Foil faced polyiso would be less than 0.1 perm, but a higher labeled R, enhanced slightly by the low-E foil surface facing the rainscreen gap. The average seasonal performance would be slightly better than the intial XPS performance, but mid-winter slightly less than EPS in your stackup. But since it's performance rebounds during the warmer temperature late winter days the drying season begins earlier- at 2" it's still just fine from a sheathing moisture perspective at in a 2x6 wall in zone 5A.
If it's any cheaper, damp sprayed cellulose has about the same thermal performance of open cell foam, and has a much lower environmental impact, and lower risk of problems. If the foam installers get the mix wrong or set up with the wrong temperature for conditions there is some risk of long term outgassing and odor/health issues. It's not a huge risk, but it's not zero either. When it's pretty much even-money it's both safer & greener to go with cellulose.
My recommendations:
First stick with OSB. Save the dough. If you have a worry about rotting down by the mud sill, use 1/2 treated plywood for the bottom two feet.
Second, use eps foam. Get it used if you can. Use two inch or two and half inches. Use six inch headLok screws. Screw into the studs. This is easiest to do do before insulation so you can make sure you hit everything. Space your screws two feet apart or closer. But you need not go much closer since the screws cost over fifty cents a piece.
Third, use 3m all weather tape on OSB seams. If you want to go super sealed, caulk your stud bays and where your framing meets inside. You can use the same tape to tape your foam joints, and flash your windows.
Last- use dense pack cellulose insulation and save the open cell foam for your mud sill, above the plate and under second floor, and in corners and shallow bays like where you have headers.
Thomas,
I agree with Dana and Joe that when it comes to choosing an insulation to install between your studs, cellulose is a better choice than spray foam.
My walls, also in zone 5, are what Joe recommended above. I am pleased with them so far (the project is still under construction). The builder and his framing crew resisted the rigid foam at first. They had used rigid foam only once before and it had been an unpleasant experience. On that job, they spent a lot of time standing around the job site trying to figure out how to handle various details. We avoided that problem by working out the details for things like windows beforehand. The only complaint I heard from the crew was that the work of taping seams and installing the foam was tedious.
I used graphite infused EPS with facers. If I had it to do over, I would have skipped the facers. They added cost and didn't really contribute anything. We could have left the Tyvek off and counted the facers as the WRB. That would have added a couple R points for radiant barrier in the rainscreen. The builder would have been comfortable with that in open sections of the walls, but wasn't comfortable with that around the windows. My knowledge of window flashing is too superficial to challenge my builder's judgment on that.
We haven't done the cavity insulation yet. The insulation contractor is uncomfortable using damp sprayed cellulose due to the foam on the outside. His proposed alternative is to use a net and spray in fiberglass. I am not convinced that his concerns are justified. However, since I don't see a problem with his proposed alternative, I am not pushing back on this change.
Reid,
Did you and your contractor discuss dense pack cellulose? I know that in unvented roof assemblies, DP cellulose does a much better job of protecting the sheathing than fiberglass. I can't say for sure that this applies directly to a "tight" wall assembly, but personally I would be more comfortable with the cellulose.
Thank you all for input so far. It's refreshing to hear I won't have to make any major changes to have a durable assembly.
Reid-where did you source your graphite infused EPS? What was the cost (as you recall)?
Jonathan, the way my builder explained it to me is that the fiberglass would be densely packed in the same way the cellulose would be. It won't be happening for a couple weeks so there is still time to change if there is a performance difference.
Thomas, we ordered our foam directly from Insulfoam. In addition to graphite infused (Platinum) for the exterior walls, we ordered regular EPS for the basement walls and under the basement slab. I don't have the cost at my fingertips.
As long as the fiberglass is dense packed to at least 1.8lbs per cubic foot density it's air retardency will be in the same range as cellulose. It won't have the same hygric buffering capacity of cellulose, but with sufficient exterior foam for dew point control at the sheathing that won't matter. It would be able to dry faster than cellulose if it ever got wet.
All-
Thank you again for contributing.
As an update, I have sourced graphite infused EPS from Insulfoam. Can't say enough good things about these guys. Knowledgeable staff, great product. Worked out to a little over 18 bucks a sheet (shipped), which was a huge saving over my XPS bid (28 dollars/sheet), in addition to be an all around better product, save the initial R-value.
Looking into dense pack cellulose now.
Thank you all again.
Don't be surprised if dense packed cellulose comes in higher than open cell foam.
A cheaper alternative would be damp-sprayed cellulose, which is also just fine. The R-value is about the same as dense-packed, and it's not quite as air retardent, but still sufficiently air retardent to prevent convection within a 2x6 cavity with 2" of graphite loaded EPS on the exterior. Moisture activated adhesives keep it from settling over time even without dense packing.