Review my Mooney Wall proposal and critique

3 bed/2 bath 1,456 sq ft single story ranch (conditioned walk out basement)
Basement slab R10 underneath, slab complete thermal break
3″ EPS continuous from the footing over rimjoist to under the trusses (2.5′ eave)
Manual J states total Htg load (Btuh) is 17,858
Current HERS rating of 41
Climate zone 5
This is spec’d for a forced hot air unit, a mitibishi heat pump. After some consideration I would prefer a radiant heat option, its what I’ve always been exposed to and don’t like forced air in friends houses. I would like to use a pex aluminum track application under the subfloor. And am trying to work towards a solution that would allow me to use the Sanco2 heat pump water heater as my radiant heat source. At this point I don’t believe there will be capacity left enough for domestic hot water production even with a drain energy recovery device.
Current wall assembly
Anderson 100 casement windows (u.28) window/wall ratio .12
Vinyl siding
3/4″ rain strip
3″ recycled EPS CI exterior
Tyvec drainwrap
1/2″ plywood with Prosocco R guard application for air sealing
2×6 walls 16″ on center with R21 hi dense batts
5/8″ drywall
Vapor permeable interior paint
With the mooney wall, I would be proposing to add a 2×4 horizontally on the interior wall. I would also be considering changing to dense packed cellulose for the cavity insulation.
Given the increased insulation values and decreased thermal bridging is this enough to lower my heating btuh requirements within the realm of Sanco2 possibility for radiant heat source? Using spacepak or arctic solutions I have been told by hvac contractor it will be more costly than the ductwork and air to air heat pump assembly. The Sanco2 is a fraction of the price and I can perform the instal myself.
Last concern is condensation developing on the sheathing. My reading leads me to believe that condensation with this level of interior/exterior insulation may develop condensation issues during the shoulder seasons but should be mitigated with the rain strip and buffering capacity of using plywood vs OSB.
Thoughts? Tear it apart, help me do this right. It won’t be passive house standards but I’ll shoot for the best I can within practicality. Thank you in advance.
GBA Detail Library
A collection of one thousand construction details organized by climate and house part
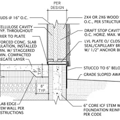
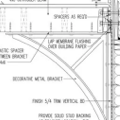
Replies
jmaynard,
Climate zone?
Thank you. Climate zone 5 Western MA. I’ve got to be missing some elements. Lay them out.
Jmaynard,
I'm sorry, I don't know enough to comment on your choice of heat source, but the amount of exterior foam you are proposing in climate zone 5 puts you well into the safe category of walls, and everything you are suggesting for them looks good.
https://www.greenbuildingadvisor.com/article/calculating-the-minimum-thickness-of-rigid-foam-sheathing
That amount of retrofit is simply not worth it. I would also doubt it would reduce your energy use to bellow 8000BTU a single Sanco2 can do.
My $0.02. Install a ducted mini split in the basement and call it a day. With a basement it is easy to run all the ducts there and in the floor joists.
If you must have air to water heat pump, better off getting one that is right sized for your current load than tearing the house apart to get it more energy efficient.
This will be new construction. It was an effort to maximize wall r value while keeping the build as simple as possible while keeping costs as low as they can be. Builder doesnt want to do double wall, already doesn’t like using exterior foam. But he’s willing to work with me on details that are outlined by the hers rater. What kind of performance is gained with the thermal break provided by 2x4’s on edge on the interior to the total wall assembly when using dense pack cellulose?
Your existing assembly is about ~R31.
Adding the 2x4 with R14 batts, would get you up to about R42.
I can't see that making enough of a difference to be worth the effort. A simpler upgrade would be to bump up the studs to 2x8. This would get you to mid/high 30s for not much extra cost/work. In zone 5 with 3" EPS, the 2x8 assembly would still work without any warm side vapor retarder other than painted drywall.
What would be the conditions when you would need a warm side vapor retarder other than painted drywall? Indoor humidity too high in the winter?
When your assembly can dry to the exterior you want to block indoor humidity from entering it.
It depends on your climate zone and the amount of exterior rigid you have.
Take a look at Table 2 here:
https://buildingscience.com/documents/building-science-insights-newsletters/bsi-100-hybrid-assemblies
As long as you have more than the required ratio of exterior insulation, class III VR (ie painted drywall) is fine.
If you have less, the wall will still work but you'll need at least a class II VR (ie faced batts). With these walls it also helps to pick a somewhat vapor permeable exterior rigid such as unfaced EPS/XPS or one of the microperforated ones to allow for a bit of extra drying capacity.
Given the increased insulation values and decreased thermal bridging is this enough to lower my heating btuh requirements within the realm of Sanco2 possibility for radiant heat source?
I highly recommend doing a room-by-room Manual J or similar heating and cooling load analysis. BeOpt is also good.
This will allow you to see several things. One is what the impact of various substitutions is and you can figure out what is the most cost-effective assembly is and how far to go with enhancements before it stops making sense*.
Second it tells you the total size of your heating system. If you're trying to reach a particular goal -- 8000 BTU/hr for Sanco -- then it tells you how far you have to go to reach it. Third, if you do room by room numbers, and you want to do radiant heat, you can figure out how many square feet of heating you need in each room, and go over the plans to make sure your layout allows for it. It's not uncommon to find that a corner room with lots of windows doesn't have enough floor area and you have to figure something else out.
Two other thoughts: In Massachusetts you're going to need air conditioning. And presumably after doing all of this insulation you're going to seal this house up tighter than a submarine, which means you're going to need ventilation and an energy recovery ventilator. So you want to plan all of this as a system.
One approach would be to install a ducted minisplit and ducts. Use the same ducts for your ventilation air. Size the minisplit for your summer cooling load. Size your radiant heat so that together with the heating capacity of the minisplit you have enough heat. Most of the time in the winter use the radiant for your heating, on the coldest days run the minisplit too. You can automate that just by setting the thermostat on the minisplit a degree or two below the thermostat on the radiant.
The thing to look out for with air-to-water is cold weather performance, the ones I'm familiar with drop off pretty steeply as the temperature gets colder. I'd expect your design temperature is around 10F and you might get half of rated capacity at that. Some of the newer minisplits really keep capacity in cold weather, in particular the Mitsubishi Hyperheat models.
*(What jumps out at me in your description is the Anderson 100 windows at 0.28, I think you can do better there. But it depends on how much window you have and what options are available to you.)
I really appreciate the thought and time everyone is putting into their posts. It is very insightful and helpful information. Building plans with window/door schedule and manual j attached. I went with a casement window for increased air tightness. The whole house will be built with a maximum air tightness goal. Aero barrier if needed. Anderson 100 seem to be a good window. Not great, not poor. The price was attractive. It sounds like mitibishi is coming out with a game changing air to water heat pump next year. Both my hvac and hers rater said maybe just mini splits for now, do radiant at a later time. And make sure that dehumidification is thoroughly satisfied for the entire needs of the building accounting for a radiant only heat source. It’s 1100 feet of elevation in beautiful countryside. I’ve always liked opening windows for fresh air and just doing it morning and evening instead of air conditioning. I don’t know what kind of a dehumidifier would be needed with a radiant only application and also account for bathroom venting moisture. Might not be possible. There’s a higher cost with a 2x8, I was surprised at the jump. Though by the time you factor the time it takes to install a Mooney wall, might just be worth it in the end. I was hoping for some excellent thermal break reduction performance.
Dehumidification is usually only an issue in the summer. You definitely want ventilation which should handle humidity in the winter.
In a super-tight house heat distribution isn't as important as it was in the leaky houses built in the last century, if you have an open plan you can get away with only a few heat sources. Similarly, radiant heat makes the biggest impact in a house that is cold and drafty.
The exception is bedrooms, people tend to sleep with their doors closed and everyone likes to sleep at a different temperature, so you want each bedroom to have individual control. The problem with minisplits is that even the smallest heads are way too big for a typical bedroom. You can get some level of control with a ducted minisplit, you can adjust the airflow to each room with dampers. One of the nice things about hydronics is it handles low loads really well, with an air-to-water heat pump and a hydronic air handler in each room with its own thermostat you can really tune the comfort level. But you might find the price point eye-watering.
Read my reply #5 in this thread for thoughts about floor heat:
https://www.greenbuildingadvisor.com/question/hydronic-heat-underfloor-vs-in-wall
One option is to go for an in-between.
You'll need dehumidification and cooling, so a ducted heat pump is in your future weather you like it or not. If this is a cold climate unit, it can easily handle the bulk of heating load for the house as well.
You can than go for the Senco and use it for combi heat for your DHW and providing localized floor heat. Since the heat pump is handling the bulk of the space heat, now the output of the single unit should be enough to get you that warm toes feel in any high traffic area.
A good setup would be to use a larger dual coil indirect as the buffer tank. Run is a reverse indirect where the DHW goes through the coils and the Sanco unit heats the tank. This would let you use glycol for the space heat which avoids any of the ugly issues of trying to pipe water outdoors.
Another option is to save the roughly $10k to $15k this would all cost and simply go for some staple up resistance mat for the local floor heat and a regular HPWH.