Retrofit to a conditioned attic in WI

I have searched and read as many of these types of articles as I can, keeping in mind the dates of the articles to see what is the most recent information.
I had a blower door test on my 4-year-old 2-story home (2016 build) and found that insulation was done poorly with lots of air leaks. I would like to get my AC unit in conditioned space and tighten up what I can as a result of the blower door test. Based on what I have read, I will list what I have going on.
Located in Milwaukee, WI
Truss attic with blown-in insulation.
Radiant in-floor heat throughout the house.
High-Velocity air conditioner in the attic.
Asphalt Shingles with ridge vent.
Vapor barrier (plastic) was stapled to the bottom of the trusses prior to drywall going up.
25 leaky can lights going to the attic along with 5 ceiling fans.
HVR on the 1st floor.
From what I read, I need to remove the baffles and block the air venting from the soffits. Use closed-cell foam to spray in-between each truss on the bottom side of the roof sheathing. Install rigid foam (size & type?) to the trusses to reduce thermal bridging & use as fire stopper.
Do I need to install a supply & return in the newly conditioned space with all the leaky can lights? No forced air is done in the winter due to radiant floor heating.
Do I do anything special with the ridge vent?
Thank you in advance as I try to get this correct.
GBA Detail Library
A collection of one thousand construction details organized by climate and house part
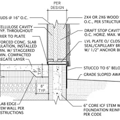
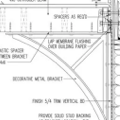
Replies
>"From what I read, I need to remove the baffles and block the air venting from the soffits. Use closed-cell foam to spray in-between each truss on the bottom side of the roof sheathing. Install rigid foam (size & type?) to the trusses to reduce thermal bridging & use as fire stopper."
That can be both risky and expensive, easy to screw up. And an un-vented closed cell foam insulated roof is about the least-green approach to the problem, and could be the most expensive. You're in climate zone 6A (the warm edge), which would need at least half the total-R to be closed cell foam on the underside of the roof deck to have sufficient dew point control on any fiber insulation, and it's really UN-green stuff, even the HFO blown versions:
https://materialspalette.org/wp-content/uploads/2018/08/CSMP-Insulation_090919-01.png
Rigid foam board is not a fire stopper, but it is vapor retardent, and could end up creating a moisture trap if sandwiching fiber insulation between closed cell foam a the roof deck and rigid foam board at the bottom. Half-inch gypsum board would be the usual solution for meeting fire codes.
How deep are your rafters? Are the rafters trusses? If yes, are they an I-joist type or open web?
Any hips or valleys, dormers etc to screw up soffit to ridge venting?
Is there enough headroom to build an air tight platform over the HVAC equipment, lights, and ducts to created a service plenum, putting fluffy insulation on top of the platform?