Retrofit rafter insulation

My parents live in a 30+ year old owner-built saltbox house in climate zone 6a. The house has 2×8 rafters which were insulated with compressed 2×10 sized fiberglass batts with no ventilation channel behind them. They recently discovered an extensive mold problem on the roof sheathing. It looks like the problem may extend to the entire roof.
They’ve connected with a mold remediation contractor to take a look, and presuming that there’s no rot, they’re going to reinsulate and air seal their rafters. With 2×8 sized rafters they have limited options to get up to code levels of insulation (R-49).
They’re considering two choices:
1.) Creating a ventilation channel with strapping and then adding two layers of 3″ polyiso boards between the bays, then adding a 1″ layer of polyiso with taped seams on the interior side of the rafters.
2.) Spray foaming the rafters. To get to code, they would either have to fill the rafters, or put in 6″ of foam and add a 1″ layer of polyiso outside the rafters.
They live in a rural area with limited contractors available. There’s a program in our state that subsidizes energy efficiency upgrades, but to qualify, homeowners have to use approved contractors. The program will cover spray foam, but it won’t cover cut-and-cobble.
They’re concerned about potential off-gassing from improperly installed spray foam. They’ve contacted all the approved contractors who service their area and all the ones that are available have had a few red flags (offering to the job in the wintertime, suggesting below-code insulation levels, claiming to use “polyiso spray foam” which to my knowledge doesn’t exist…).
If they go with a cut-and-cobble approach, they would be using canned closed-cell foam to seal the edges of the polyiso layers, adding a sheet of PE over the rafters, then adding another layer of polyiso on top with taped seams, then strapping, then airtight drywall on top of all that. It would be a lot more work than spray foam, but it’s something we could do ourselves, and with the redundant air barriers, it seems to me they wouldn’t have to worry about moisture getting into their rafter bays.
Here’s my questions:
1.) If they go with spray foam, what should they be looking out for to ensure the job is done properly? Can it be safe if installed correctly?
2.) Does anyone see any potential issues with insulating with polyiso in the way that I described? Would a smart vapor retarder be a better option than PE or does it matter considering there will already be faced polyiso covering the bays?
3.) Are there any other ways to get up to code (or close to code) without removing the roof?
GBA Detail Library
A collection of one thousand construction details organized by climate and house part
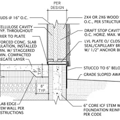
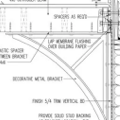
Replies