Retrofit of a cathedral ceiling

I am living in a Log Home in Madison WI. (Zone 5-6) with a vaulted Ceiling. (2×6 rafters R-19) I am hoping to redo the roof soon. I wanted to put on a layer or two of Rigid Foam. XPS or EPS. Ideally getting close to R-20 plus the 2×6 insulated cavity. I will then put a standing metal seam roof on top of the foam using furring strips.
My issues are this. I am concerned that I will be trapping moisture between the XPS or EPS and the Vapor retarder or Vapor Barrier that is most likely installed on the warm side of the house. Right behind the sheetrock and before the batt insulation.
Does anyone have any thoughts about this idea? Will I create a double vapor barrier and trap moisture in there. Or is adding the insulation on top better than leaving the what would only be R-19 which has the potential to cause ice dams as well as massive loss of heat.
GBA Detail Library
A collection of one thousand construction details organized by climate and house part
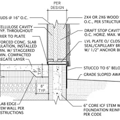
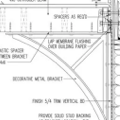
Replies
First, by code, in CZ6, you are required to install R25 min. above the roof decking, or 4" Polyiso R27, and R24 min. under the roof decking, which 2x6s doesn't give you enough space. You should install 2x8 rafters (adding 2x2s to the 2x6s) and then fill the cavities with Cellulose or BIBs for the R24 min. you need. Total roof insulation would be R49-51, meeting code!
Second, you don't use vapor barrier inside the house, you need the cavities to dry to the inside.
User-6884681,
I suggest that you read this article: How to Install Rigid Foam On Top of Roof Sheathing.
Armando is correct: You need to install at least R-25 of rigid foam above the roof sheathing in Climate Zone 6 for this approach to be successful. (If you are in Zone 5, all you need is R-20 of rigid foam). If you can do that, you don't have to worry about the interior polyethylene -- while the polyethylene isn't ideal, its presence is unlikely to cause problems (as long as the rigid foam is adequately thick).
Armando's suggestion to upgrade your rafters and improve the insulation between the rafters makes sense, but it would be quite expensive. If I were you, I would proceed with the rigid foam plan, but I would probably skip the new rafters and new insulation between the rafters due to the high cost of that work.
Madison is in zone 6, not zone 5. You need at least half the R to be foam above the roof deck, and either a total R of R49, or an assembly U-factor of U0.026 (the equivalent of R38.5 continuous insulation, including the R of the air films, roof deck, ceiling gypsum, etc.). You can get there with the existing R19s for less money and better dew point margin than ripping it up and adding depth for deeper or higher-R fluff.
For dew point control purposes polyiso needs to be derated to R5/inch due to it's lower performance when cold than the 75F mean temp at which it is tested for labeling. That means it takes 5", to hit R25, not 4". The pre-existing polyethylene makes it even more important to have some margin on the exterior foam, since drying rates are glacial.
Even though the existing R19s perform at R18 when compressed into a 5.5" deep rafter bay and 5" of polyiso would only be good for ~R25 for a total of ~R43 you'll still meet code on a U-factor basis due the excellent thermal break the R25 foam provides for the rafters.
If using EPS you can up-rate the foam performance to R4.5/inch for dew point control purposes, but it'll still take 6" of foam. XPS should be derated to R4.5/inch too since over few decades it degrades to EPS levels of performance as it's climate damaging blowing agents diffuse out of the foam.
Reclaimed 2"-4" roofing polyiso is pretty cheap and ubiquitous, 1/4-1/3 the cost of virgin stock goods. There are likely to be recliamers and salvage materials outfits in your neighborhood with some in stock (if not immediately, within a few months.) This reclaimer in Kankakee IL probably have something suitable, and may be worth the drive (or freight):
https://milwaukee.craigslist.org/mad/d/used-poly-iso-insulation-sold/6213352529.html
or these Chicagoland location:
https://milwaukee.craigslist.org/mat/d/truckloads-of-rigid-foam/6197718459.html
There are probably other reclaimers closer to you to sleuth out, and it's worth taking some time to find them.
Update,
Thanks for all of the advice.
After further examination of the roof system, i have discovered that my roof assembly looks more like this.
Sheetrock, 4x12 beams ever 4' oc and then perpendicular 2x4 to hold the sheetrock. Space is close to 14-15" and this is filled with what i am guessing is R-35-R-40 Kraft Faced fiberglass insulation.
question 1- is by adding EPS to the top of the roof sheathing will that trap moisture b/c of the Kraft Faced insulation below?
Question 2- in order to keep a ratio of 51% foam to fluffy I would need to put at least R-40 on top of the roof is that right? I really i only want to put about R-10 up there to get me to R-50.
Thoughts
User-6884681,
Q. "Will adding EPS to the top of the roof sheathing trap moisture because of the kraft-faced insulation below?"
A. Whether or not the fiberglass insulation has kraft facing is irrelevant. The kraft facing poses no particular problem (since kraft facing is a "smart" vapor retarder with variable vapor permeance).
Q. "In order to keep a ratio of 51% foam-to-fluffy, I would need to put at least R-40 on top of the roof. Is that right? I really only want to put about R-10 up there to get me to R-50."
A. Your analysis is correct. Installing only R-10 of rigid foam above your roof sheathing would be (a) a code violation, and (b) unwise, since the resulting ratio (20% of the R-value from rigid foam and 80% of the R-value from fluffy insulation) would be seriously out of whack. This out-of-whack ratio is likely to result in moisture accumulation in the sheathing.
Martin,
Thanks for the direct answers.
I did not know that about Kraft facing. Most of my experience is with vented roof assemblies so all of this is newer to me.
At this point, i will not be installing R-40 in EPS Sheathing. Would it be better than to stick with my current system of R-40 fiberglass?
Or put R-10 up there banking on the sheathing drying to the interior b/c of the smart vapor retarder of the kraft facing.
Also, i have heard that EPS in thin enough sheets do have vapor permeance. would one sheet of about 1.5" t 2" be able to allow moisture to pass through at a good amount?
Thanks
User-6884681,
Q. "I will not be installing R-40 in EPS sheathing. Would it be better than to stick with my current system of R-40 fiberglass?"
A. The answer depends on whether your existing roof assembly has a vent channel between the top of the fiberglass insulation and the underside of the roof sheathing. If it has a vent channel, the existing assembly is not at risk of moisture accumulation. If it lacks a vent channel, the existing roof assembly (like your proposal to add R-10 exterior rigid foam) is at risk of having moisture problems.
Q. "Or should I put R-10 up there banking on the sheathing drying to the interior because of the smart vapor retarder of the kraft facing?"
A. No, you shouldn't do that. As I explained in my last response, that's a risky strategy.
Q. "I have heard that EPS in thin enough sheets do have vapor permeance. Would one sheet of about 1.5 inch to 2 inches be able to allow moisture to pass through at a good amount?"
A. EPS in that thickness range has a vapor permeance of between 1 and 3 perms. That means it is a Class III vapor retarder (slowing but not stopping the movement of water vapor). But why do you ask? You aren't likely to get any outward drying through a layer of EPS installed on the exterior side of your roof sheathing, since most types of roofing prevent water vapor from evaporating to the exterior.
Martin,
I do not have a Vent channel nor a vented, soffit Gable, or ridge.
I ask about the EPS b/c I am installing a Roof underlayment with a perm rating of over 5.0 and then a metal roof overtop of that?
If I created a channel above the roof foam with Purlins or furring strips and then installed my metal roof on top of that would it allow any water trapped in the sheathing to travel through my underlayment and then through the 1.5"- 2" of EPS into the vented channel and out?
This way I would get an extra R-10 plus a better vapor management system than before?
Thoughts?
User-6884681,
I don't suggest that you use rigid foam in the way you propose (because outward drying would be very slow). Note that your proposed approach would violate building codes.
If you want to consider an experimental approach, you could consider adding an exterior layer of semi-rigid mineral wool on top of your roof sheathing. Mineral wool insulation is highly permeable.
If you want to try this, you should know that (a) this approach is very rarely used, (b) local roofers will think that you are nuts, and (c) it would still be a good idea to include ventilation channels between the mineral wool and the roofing.
I've never seen data on just how vapor-permeable vented-external-insulation at less than recommended R values has to be to do more good than harm. The assumptions I've seen are that mineral wool is beneficial at any thickness and foil faced foam insulation needs to be at least the full recommended R value. EPS is at some unknown point in between these extremes.
The vapor permeance of EPS is known, and at least a full order of magnitude more vapor-tight than rigid rock wool. Roxul Comfortboard 80 is north of 30 perms, which is more vapor permeable than some housewraps.
Type-II EPS is between 1-1.5 perms @ 2", which is NOT very permeable at all. Unfaced Type-I EPS would run 1.5-2 perms, though more permeable than Type-II EPS it is still at best only HALF the vapor permeance of standard interior latex paint, and thus a real impediment to drying toward the exterior.
The EPS either has to be an inch or less in thickness to have the vapor permeance of interior latex. Going any tighter (thicker) than that calls for a careful WUFI simulation to get a sense of the risk level, unless it can be taken all the way to the IRC prescriptive ratio.
Venting the roof deck from the top side is in no way equivalent to under the roof deck. With the vent under the roof deck the moisture encounters the dry outdoor air in the vent channel before it reaches the roof deck. Venting it from above means the moisture has to pass through the roof deck first, raising it's moisture content. The roof deck is on the order of 1 perm when dry- it's a real vapor retarder, but a variable vapor retarder that becomes more vapor open as it's moisture content increase.
But it takes mold-risk levels of moisture before plywood becomes as vapor open as interior latex paint.
In this case, there is unspecified kraft paper and at least the potential for vapor retarding paint on the interior side. So, even with 2" of Type-I EPS, possibly more drying to the exterior than wetting from the interior - not accounting for any air ex-filtration. To be clear, I'm not recommending doing this.