Retrofit insulation and some kind of rainscreen

I read 36231/retrofit-insulation-walls-no-sheathing-or-wrb Our house is very similar (including being in Portland!) – original wood siding, no sheathing, no insulation, then studs that are 16″ OC (variable). Also balloon. But we have made a preliminary hole in the plaster and when it rains hard, the siding gets soaked (the rain hits this side of the house). We plan to strip exterior walls to the studs in order to insulate.
Question: could we ignore the water soaking the siding and just follow option #2 ( Install 1″ by 1″ sticks, etc) to create an air gap. Would this gap protect the rigid foam from water? Or should we install some kind of low-tech rain screen before installing the rigid foam.
Thanks
GBA Detail Library
A collection of one thousand construction details organized by climate and house part
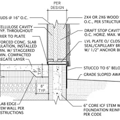
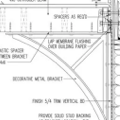
Replies
Given that there are at least a dozen cities & towns named Portland in just the US alone, it might be appropriate to hint as to which Portland you hail from.
https://en.wikipedia.org/wiki/Portland
Depending on which Portland it is it might be worth doing more than just a rainscreen & WRB.
Catherine,
I'm guessing that you were trying to include a link to an old Q&A thread -- apparently this one: Retrofit insulation in walls with no sheathing or WRB?
If my guess is correct, then we are on our way to figuring out the answer to Dana's question -- I'm guessing that you live in Portland, Oregon, just like the author of the earlier post (Ray Sten).
Catherine,
It is unclear from your post whether you are opening up your walls from the interior (by removing the plaster or drywall) or opening up your walls from the exterior (by removing the siding). But I'm guessing that you are working from the inside.
If my guess is correct, and if you intend to install rigid foam between your studs (following the cut-and-cobble method), then you definitely want to install vertical 1" x 1" sticks in each stud bay, up against the siding, to create an air gap between the back of your siding and the cut-and-cobble rigid foam. If you do that, you don't need to install some other type of retrofit WRB -- for example, strips of asphalt felt or housewrap. The rigid foam is enough of a barrier in this situation.
Hi Martin, thanks for your prompt reply, and yes we are removing the plaster and drywall.
Although if it were a good idea, we would consider removing the siding, "improving" it (whatever that involved), and putting it up again. But I am inferring that it is kind of ok for siding to get wet through. (BTW, we will be painting the exterior in the next few years to deal with peeling paint, which will presumably improve things). So we will definitely go with the sticks solution.
Two last questions 1. By "rigid foam", do you mean one of the insulating panels - EPS or XPS or polyiso - or do you mean something lower tech?
2. If we fill gaps in the siding, is it important to make sure the siding can still "move"?
Catherine,
"Rigid foam" refers to any of three types of insulation (XPS, EPS, or polyiso). Green builders prefer either EPS or polyiso; they try to avoid the use of XPS, because XPS is manufactured with a blowing agent that has a very high global warming potential.
What type of siding do you have? If it is lap siding (clapboard), don't caulk the gaps.
Yes, it is rabbetted, fir siding so I guess we will fill the gaps (eg knots that have fallen out) without actually "gluing" anything together. Thanks again.
With variable-spaced studs cut'n'cobbled half-inch foam (any type) with blown fiberglass or cellulose filling the remainder would be the best approach. If you can give up an inch of interior space, use unfaced XPS for the cut'n'cobbled foam (so that the wall can dry toward the exterior) and an inch of continuous polyiso over the interior side, covering the stud edges.
The inch of continuous foam would roughly double the thermal performance of the whole assembly, since it would nearly triple the R value of the framing fraction, which is typically about 20-22% of the total wall area for balloon-framing approximately 16" on center.
While you have the stud bays open, paint the interior side of your siding with a high quality latex primer. The peeling paint problem is primarily a function of different drying rates between the interior & exterior side, which may become even more exaggerated after you insulate with an air-gap. The average siding temperature will be lower, and the moisture content somewhat higher, but with a heavy coat of latex to moderate the uptake and drying of moisture on the side facing the cavity it should be less prone to peeling than it has been to date, or at least not worse off.
I think Dana meant to recommend unfaced EPS for the first layer (toward the exterior), not XPS. Better drying capability and lower climate impact.
Half-inch unfaced EPS isn't stiff enough to hold back higher density blown fiber without cracking, and is not adequate a weather resistant barrier without facers. This is one of those rare instances where XPS is the overall best choice. If the span is more than 14.5" it's probably better to bump it up to 3/4" or even 1". EPS with facers would be fine at 1" from a strength & WRB point of view but the facers become a problem if there is foam on the interior side. Without facers or a separate weather resistant barrier EPS just doesn't cut it in this application .
If there is NOT going to be interior side foam 1" foil faced polyiso would be the right stuff for the cut'n'cobble. But foil faced foam on both sides of the assembly would create a severe moisture trap, which is asking for trouble at some point down the line.
Ah, makes sense. I didn't quite think it through and I'm so used to hearing you tell people to avoid XPS that I assumed it was s typo.
Another option would be to seek out higher density EPS--type II or better, which would work better on both counts, but might be a hassle to procure.
Hi Dana, thanks for the info. You say "if you can give up the space" - not sure what this means. Do you mean to face the inside of the wall with polyiso, as if it were drywall? If this is correct, how would we then attach drywall, given that the polyiso is 1" thick? Just using extra long screws?
Also, we plan to insulate with fibreglass that is kraft-paper-faced on one side. Given that, can we forego the polyiso on the inside? I can see that covering the studs on the inside would improve R value a lot, but we are not super concerned about making the house really tight, given our location. (Famous last words!) We will at a future point be more concerned with doing insulation along the exterior wall for that space between the floorboards and ceiling, so our floors aren't so cold.
The idea about painting the insides of the siding sounds like a good idea and we will make sure to get a good quality primer.
We will also look into getting EPS type II ... but no promises. If we go with only one layer of panel, does the EPS go with foil side in or out? I assume foil in, so the panel can absorb moisture and then release it when it stops raining??
Thx
Catherine
With continuous foam on the interior like drywall, yes you'd have to long-screw or long-nail the drywall to the studs.
Fiberglass batts with or without a vapor retarder such as kraft paper would not be a substitute for the interior foam, since it is still thermally bridged by the framing. It would be fine to install rigid foam over the interior side of batt-insulated cavities (with or without kraft facers), as long as the exterior side foam is at least semi-permeable to water vapor.
Without the interior foam your wall performance would be only a bit better than 1/3 of current code minimum for climate zone 4C (Portland OR), which would be pathetically low performance.
WITH 1" interior polyiso the U--factor of the assembly would still not meet IRC 2012 or 2015 code max, of U0.057, but would bring it up to IRC 2009 code min.
It would take at least 1.5" of interior polyiso to bring it up to current IRC code, but that's very awkward to build, since it would take 3-3.5" drywall screws, and would require more window detailing than just an inch.
If using foil faced EPS for the cut'n'cobble put the foil on the exterior, facing the siding. If using EPS for the continuous interior layer you'd need 1.5" to meet IRC 2009 code performance, 2" minimum to bring it up to something like current code, and it need not have facers. If faced on one side, it doesn't matter which side, but it's actually better if it's unfaced, to allow at least some drying toward the interior.
Sorry for the delay replying. Thanks for all the good advice, we are definitely going to do the sticks and maybe add the extra layer on the inside.