Retro Vapor Transmission Reduction

Background:
We have 30 year old elevated, 3 level home in Coastal SC. Ground level is 1/3 garage w/ sheetrock ceiling (fiberglass insulation) (pic attached) and 2/3 is storage area (concrete floor, 9 ft clear, vented to outside w/ large 5 ft wide louvers and lattice) w/ closed cell spray foam insulation (pic attached) … foam covers area between joints, but joints are not treated).
Problem:
Installed site finished red oak hardwoods throughout last April. By July the floors main level floors began to cup, now badly cupped. Main level is over ground level… top level (2rd floor living space) did not cup.
NWFA Inspector found main level of house RH at 45%, but ground level ranged from 55% to 90% based on outdoor weather. Wood moisture readings were ~9% interior (finished) surface, ~10% center of board, but under side of plywood subfloor measured 18%. Inspector explained the wood cupped because of high moisture transmission from garage up thru the floor. Area above the garage exhibits worse cupping, area above storage (spray foam) shows minor cupping.
Recommendation:
Inspector advises we must reduce moisture transmission from unconditioned space on ground level. Would be very difficult to encapsulate as it is very open.
Options:
For the garage, is it feasible greatly reduce transmission by sealing the gaps w/ caulk and applying a barrier paint to the surface? If so, what products would be recommended.
For the storage area (w/ closed cell spray foam)… could we paint the exposed joists to reduce transmission?
Other ideas?
Thank you for your input!
GBA Detail Library
A collection of one thousand construction details organized by climate and house part
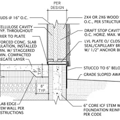
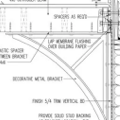
Replies
I would give this a read for a primer:
https://buildingscience.com/documents/insights/bsi-009-new-light-in-crawlspaces