Retrofitting exterior EPS on brick veneer home

Hi name is Eric Kas – I’ve been a reader of GreenBuildingAdvisor and have not posted anything yet. However, I thought this would be a helpful time to get some feedback. 🙂Â
I just recently purchased a 1956 brick-veneered bungalow in West Michigan, which is in climate zone 5a (the northern part of it – though its feeling more like zone 6 these days).
Currently the home has zero insulation in the 2×4 stud wall cavities. It has a fair amount of insulation blown into the attic. I’m thinking of first having loose-fill cellulose blown into the wall cavities. There is some type of black asphalt felt in between the 2×4 studs and the brick. I’m unsure if there is an air gap between the felt and the bricks.Â
My plan is this:Â
– Install 4″ of EPS directly over the brick veneer (two 2″ thick 4’x8′ boards layerd so seems are covered) I will use these Plasti Grip Fasteners to mount these: Rodenhouse-inc.com/plasti-grip-pmf
– A tyvek water barrier over that, when I install this I will also be taking out all original windows and will have them all flashed at the same time.Â
– Furring strips to provide a rain-gap, to which the new siding will be fastened to.Â
I’m posting this because of a few things, first there do not appear to be many people who are putting exterior insulation over brick veneers, hence not many resources on this site regarding it. I realize there is an aesthetic depreciation here, but the brick is not in great shape as it is, and I would think it would be the easiest way to retrofit the house. Once done, the wall assembly will be close to a 30R, tight assembly, with some thermal mass from bricks as well – and we’ll be putting in an HRV or ERV after this.
A few questions:Â
– Is the tyvek wrb appropriate over the EPS? Is there a better product that would be more beneficial as a rain barrier and allow the wall to dry from inside/ out? Or do I really need an additional WRB over the EPS?Â
– Should the seams of the EPS be taped for purpose of air tightness? If so, what is best tape to do this?Â
Anything else come to mind regarding this retro-fit?
Thanks!!
Eric
GBA Detail Library
A collection of one thousand construction details organized by climate and house part
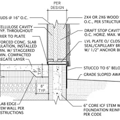
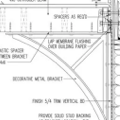
Replies
Why bury the brick? I think fastening to the brick and air sealing around it will be almost as much work as taking it down.
Maybe I don’t understand what part of the original building are you saving? Are you upgrading the exterior cladding, windows, doors, insulation, HVAC, electrical, plumbing what do you have left?
Walta
Walta, I didn't think I'd have to explain this here but these are the reasons:
1. Going from an apprx r 14 to r 30 wall.
2. Creating a very air tight envelope.
3. Keeping brick for thermal mass.
Will be replacing all the windows and doors, not gutting the house.
Ek
I would take the brick down for a couple reasons:
- The airgap between the brick and the wall cladding(felt) could represent a significant thermal bypass allowing convective currents inside the wall that will magnify the effect of an air leakage.
-removing the brick lets you keep your exterior insulation from protruding as much.
-You'll have the opportunity to airseal and deal with any cladding issues properly. Rigid insulation can be your air barrier but I would start with a good job on the cladding.
I have a 1950's brick bungalow, and have had similar thoughts about exterior insulation. My brick is ugly yellow, but it's pretty low maintenance.
The thermal mass and hygric buffering of the brick does add some resilience to the assembly, and Eric can determine whether or not there is an air gap between the brick and the walls from the interior - he's already got some access from his post. Airsealing and waterproofing can be done in one layer by using a liquid-applied WRB directly on the brick. Install and flash the new windows to the brick and treat them like "innies" related to the exterior insulation. With the WRB at the surface of the brick, he doesn't have to tape the seams in the foam or apply another WRB layer at the foam surface - just the furring and siding. There are still the architectural issues of adding 6" of thickness to the walls, but he seems OK with that. Fastening the furring through the foam and anchoring to the brick will be a PIA, but it is certainly do-able.
Its common around here to refinish brick houses with EIFS. Not my favourite look, covering nice old brick always feels wrong.
With EIFS there is a small up-charge for thicker insulation, 1"-3" is fairly common. For zone 6, for condensation control, you need 35% exterior insulation, with R14 walls you should aim for at least R8 exterior.
With EIFS, the WRB goes straight over the brick and the foam is grooved to allow for drainage. The rest of the flashing details are pretty similar to standard exterior foam install with innie windows.
If are doing interior renos, it would be cheaper to either fur out your walls to install R24 batts or go with a layer of rigid insulation over the studs. Both of these would be way less work than exterior insulation and re-side.
I would only cover the brick if it is in really bad shape or one of the ugly 1950's colours. Paying a mason for a couple of days of work to do a bit of tuck pointing and replace some bricks would be much cheaper than an entire re-side.