Cutting into Top of Wall to Spray Foam into Cavities

Hey folks – The saga continues on our home (1914 3 wythe brick in Chicago that was remodeled and sold to us by the builder).
The current assembly is: (outside) 3 wythe brick, small gap, 2×4 framing, R13 3.5″ knauff kraft face batt, drywall, (inside).
Our walls are taking on a lot of water, due to bad exterior brick sections, damaged parapet areas, bad fenestration flashing, etc. The walls also see condensation in the winter due to interior moisture in the air driving its way back through the assembly to reach the now cold interior brick face.
We are still heavily leaning towards trying to fix this thing by implementing an exterior insulation retrofit that would include a fluid applied AWB, rigid foam and cladding. If this is not pursued, we would fix and maintain the brick exterior and then somehow reconstruct the interior to follow the retrofit suggestions by Building Science Corporation.
That said, we had a contractor out yesterday that seems to think they could cut a strip in the drywall at the top of the wall, around the entire the perimeter, and then spray in closed cell foam into the cavity. The cut in this location would also give access to the floor joists as well. Has anyone successfully done this? Even if this is possible, it seems very challenging to “guarantee” a consistent application that doesn’t miss spots. If there is a good outdoor to indoor temperature differential, I suppose we could use a thermal imaging camera to try and confirm consistent application? Additionally, from what BSC reports, a ccSPF interior application on a structural masonry wall will only work well if you can cover the entire interior face of the brick continuously to create that air barrier. Really this is best done with full access the brick face.
This method might be easier achieved blowing in dense pack cellulose, but I’m nervous about putting that right up against a brick wall without any sort of fluid applied barrier. It seems like a recipe for disaster if we cannot fully guarantee water won’t get behind the bricks.
Any thoughts?
Thanks,
-Scott
GBA Detail Library
A collection of one thousand construction details organized by climate and house part
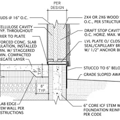
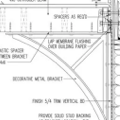
Replies
Hi Scott,
Your project is endlessly fascinating. We actually ended up talking about it on the FHB podcast that we recorded yesterday (episode 414, if you are interested). Chances are good listeners will write in with ideas. If so, I will be sure to share them. I'm anxious to see what GBA experts say about your contractor's idea. Seems a little batty to me (really hard to get right) but I'm no expert, just interested. In fact, I am wrapping up an article now on this project: https://www.brightcommon.com/pickle-factory. It has nearly the same wall assembly as what you are dealing with.
Hi Kiley -
Thanks for the response! It is endlessly fascinating... and equally irritating :)
Do you have a link to the podcast? A quick google search is only showing up to ep 411. Definitely curious to hear the discussion and would be eager to see/hear any of the write-ins.
I tend to agree on the batty comment. It will be hard to execute effectively without completely removing the drywall. And while removing the drywall in some areas is do-able, what do you do in the kitchen and bathrooms where you'd need to be pulling of cabinets, finishes, etc....
I will eagerly await your article. It is a beautiful looking building and interior!
Thanks again,
-Scott
The episode airs next Friday. The best way to find it is on YouTube (enter the episode number in their search function). The warehouse adaptive-reuse article will be in the next print edition of FHB. I feel sure it will be of interest to you. In fact, you and Jeremy Avellino would have much to talk about. He might be a good resource for your project--he is very approachable.
Thanks Kiley.
I’ll connect with you on LinkedIn. Maybe you can introduce me to Jeremy!
> That said, we had a contractor out yesterday that seems to think they could cut a strip in the drywall at the top of the wall, around the entire the perimeter, and then spray in closed cell foam into the cavity.
What happens to the fiberglass batts?
Either way, no, I don't see this being done well. Foam sets up quick and will get in its own way. Some folks claim to have 'pourable' foams, but they seem to be pretty uncommon and also risk blowouts.
Hi Patrick -
The fiberglass batt (air permeable insulation) and lack of true air barrier is contributing to the indoor condensation issue. You can read more about the building science here: https://www.buildingscience.com/documents/digests/bsd-114-interior-insulation-retrofits-of-load-bearing-masonry-walls-in-cold-climates. We opened up a few walls last winter and found the inside face of our brick frozen over. See attached image.
Many sections of the wall has becoming compromised due to wetting. My understanding is you do not want to keep wet fiberglass in your wall.
I think I should have been less ambiguous. :-)
In the scenario proposed by the contractor, what happens to the fiberglass batts when the spray foam is getting installed? Do they get left there? Do they claim they can remove 100% of the batts by pulling from the strip they cut to install the foam?
I believe the intention is to try to remove them from the strip opening in the drywall.
I reread your original question and it wasn’t ambiguous! I just misunderstood.
Sounds crazy indeed. There are companies that will cut access ports into walls and blow in cellulose, have you looked into that? You would still need to figure out the assembly as a whole.
As an aside, my dad lives in the house that my great grandpa built in the early 50's. The walls are insulated with sawdust, and my dad wants to increase the insulation by topping up the walls with more sawdust. I think I have him convinced there are better approaches.
Hi Bob -
As I mentioned, I am a bit concerned about blowing in cellulose as I'm not 100% confident that wall will be free of moisture unless we rebuild it properly with all the right control layers. We may be facing the reality that all the drywall does need to come down if we want to try and fix this thing from the inside and not go with the insulated overclad exterior retrofit.
Love the sawdust anecdote! I'd love to see that.
There is a brand of foam called RetroFoam that is marketed to go into wall cavities with existing fiberglass, the sellers claim it will compress the fiberglass and push it out of the way. They claim it has a "Goldilocks" level of expansion pressure where it's just enough to displace the fiberglass but not enough to pop the drywall off the wall.
I have no idea whether it works as advertised but it does exist.
I’ll take a look, thanks for the response !
Chicagofarbs,
Aside from the plan making almost no sense, I can assure you that the foam will not go into those wall pockets very far through a slot. Patrick is quite right about the way the foam sets up quickly. I sincerely doubt the foam would do much toward filling floor joist cavities above either. The sprayed mix hits a surface and expands almost simultaneously if my one viewing of the test outside my house is an indication. I wasn't allowed near the spraying while in progress.
I needed spray foam to provide insulating/air sealing in difficult areas around top plates between rafter tails on a very low pitch roof and a tricky parapet framing detail. The foam produced very good results where spraying into open bays between the rafters along the top plate. The pockets formed by my parapet framing were somewhat less successfully filled. The operator needed to be quite adept to maneuver the nozzle up into the pockets far enough to ensure the developing foam first started at the blocking point in the pocket. This was about 10-12" up in a 14 x 6 pocket. One very poorly filled pocket led me to explore others. There proved to be a half dozen or so that had large gaps behind what appeared to be a solid foam face. I simply filled in the gaps with Great Stuff injected with a very long brass tube.
Short of removing all the exterior wall drywall and batting, I can't see what value foam along the top of the wall would gain you. The interior moisture combined with leaks become frost or icicles inside the walls as you show. Doing a complete spray foam of the brick from the inside may prove to be only part of what you need to do if pursuing that path. Your ceiling and floor framing may be pocketed into the brick and be posing an unpleasant surprise for you. While foam inside will definitely improve your thermal concerns. I worry about the mentioned bad sections of wall and parapets.
I would caution careful planning of any details for encapsulating the brick. The parapet caps would need to extend over any cladding and any new roofing to protect against rain and snow melt migrating around the new cladding and tracking in the brick/mortar matrix. You may find that completer removal of the old parapet blocks will become necessary in order to re-cap the new wall thickness successfully.
Sorry to be such a Debbie Downer.
Thank you for your insight and detailed experience!
After googling a bit, they might have meant they’d drop a hose down or something into the cavity. I’m not 100% certain.
We very much want to overclad the exterior as it seems fixing these issues from the inside cannot be done in a confident manner. Further isolating embedded wood structural members is a concern as well.
We are getting very strange looks from every contractor we’ve talked to, try to explain why and describe how this wold be done.
It’s looking like the parapets will need to be rebuilt with either solution. Roofing as well to tie things back together. If we overclad, it would all wrap up and over in one continuous fashion, per the BSC detail.
There is no proper way to dry up fiberglass walls once they are wet. I've tried with blowers and heaters and did pretty much squat. This was just standard craft faced on both side batts in a ceiling.
Without addressing the wet fiberglass and mold behind, your house will always smell musty, so there is no way to get this issue fixed without removing your exterior drywall.
Once the drywall is off, you can treat the mold. Insulated the walls with closed cell SPF. I would not go overboard on the SPF, maybe 2" max to allow for a bit of drying still. Your triple brick wall is about R4, 2" of ccSPF would bring that up to ~R16. This would get you most of your energy savings in your climate.
You can also stuff some fluffy insulation into the cavity to bring up the assembly R value but that would mean much colder bricks. Sometimes this works, sometimes it causes issues.
Either way, I would not insulate from the outside. Once you cover brick, you loose a lot of the character of the house, it is also very hard to go back. I would only do it if you have some pretty ugly brick.
Hi Arkos,
Thanks for the response.
I hope you can empathize that removing all the exterior drywall and associated finishes (bathroom, kitchen, etc), would be an incredibly large undertaking. These spaces are nice, just recently have been constructed in 2019.
The existing 2x4 frame wall on the interior is not pulled off far enough to get 2” continuous uninterrupted spray. This obviously wasn’t what the builder had in mind.
While overcladding seems unorthodox, it would be much easier to execute in my opinion. It would also lead to a superior assembly and overall performance of the structure.