Cathedral Ceiling Retrofit

cbroda
| Posted in General Questions on
Renovating a Zone 5 cathedral ceiling in a townhouse
Happy New Year all. I am an architect renovating a Zone 5 vacation condo / townhouse with a cathedral ceiling. The original roof is 2×10 exposed rafters, 3″ to 4″ of continuous foam insulation on top (Tectum panels from the 70’s with an exposed surface below), with a cellulose sheathing. This summer the buildings were reroofed with Zip system sheathing and asphalt shingles over the Tectum / cellulose panels (no building paper / wrap, just ice and water shield 3′ up from the eave). At best we have R-5 in the insulation. I need to reach R-60. I want to insulate the rafter cavities and add a finished ceiling.
The question is whether to do a vented ceiling or not. As per Huber, the Zip board is permeable so the sheathing will vent to the outside. The Tectum insulation is definitely permeable.
I’m thinking to add R-30 batts and 2″ of foil-faced polyiso continuously over the bottom of the rafters, giving me a vapor barrier on the warm side, under the drywall. Between the continuous old insulation and the new continuous below I can pass ResCheck.
I’d like to do this without soffit vents, but am in danger of condensation? This home is not continuously occupied so in the winter the temperature of the HVAC is set to 55 degrees except for occasional weekend use, and to 85 degrees in the summer when the family is not there every other weekend. My concern is high humidity in the summer inside the home when no one is there for a week or two.
Is this a good solution? It makes no sense to me to have soffit vents and baffles below the Tectum, unless I just treat it as if it were sheathing. The next layer down is batt, then polyiso and drywall.
I’d rather not do a spray foam. Should I maybe put a foil-faced (facing up) polyiso tight under the Tectum to prevent exterior vapor from coming in? Should I prevent vapor from the outside and the inside?
To recap here are the layers from the top down:
1. Shingles
2. Zip sheathing
3. Cellulose sheathing (part of the Tectum panels)
4. Some kind of old yellow likely open cell foam continuous over the rafters (Tectum)
5. I’d like to add batt insulation between the rafters (24″ o.c.)
6. I’m thinking 2″ polyiso continuous on the bottom of the rafters.
7. Foil face of the polyiso
8. Drywall with latex paint.
Thanks in advance for any suggestions.
Chris
GBA Detail Library
A collection of one thousand construction details organized by climate and house part
Search and download construction details
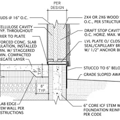
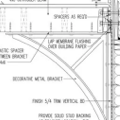
Replies
Chris,
Both practically and by code, a vented roof assembly is one with a continuous air space from eaves to peak below the sheathing, vented top and bottom, not one that relies on the permanence of the insulation to remove moisture.
From what you have said, it doesn't sound like that is an option. I would choose one of these roof assemblies we know perform well and meet code: https://www.greenbuildingadvisor.com/article/five-cathedral-ceilings-that-work
Hi - Thanks for the prompt reply.
I have the opportunity to have a ridge vent and soffit vents but would rather not put them in due to configuration issues (we have a very narrow soffit) and because the soffits are technically owned by the condo association. They will be replacing the fascias in the near future and my concern is they will damage the soffit vent or worse, cover them up (they don't generally hire the most competent people to do this work).
I've looked at these details and the unvented version #3 depicts the continuous rigid foam over the sheathing whereas mine is under the sheathing. #4 & #5 show spray foam which I don't want to use for environmental, cost and IAQ reasons.
If you look at my situation as being (from top down), roofing, sheathing that can dry to the exterior, then two layers of breathable insulation and a vapor barrier (the foil face) over the drywall, then I am preventing drying to the inside, but also preventing interior humidity from reaching the insulation and the sheathing. So maybe I am getting what I need. Trusting the Zip sheathing to prevent moisture from getting into the insulation and preventing interior moisture from entering the cavity.
As it is, if I were to vent, it would have to be between the Tectum insulation and my new insulation. Which means the Tectum insulation is useless to me.
Yet, the real question is, should that combo of the old Tectum panels and batt insulation get vented? Am I vulnerable with no continuous insulation over the sheathing? The Tectum insulation is glued to the cellulose sheathing which is now covered with Zip boards. Maybe I'm worrying too much. The insulation is protected, the sheathing can dry out and the interior humidity is blocked.
Chris,
I agree - there is little point in venting the assembly if that has to occur under the existing insulation. However your assumption that you will get any appreciable drying to the exterior through the Zip and shingles above is unfortunately incorrect. What little drying you do get will not be not enough to rely on to keep the assembly safe if it consists of mainly permeable insulation.
Similar questions come up here on GBA very frequently. The hope is that because the proven assemblies are unpalatable due to the existing conditions, that a risky one can somehow be cured by a good interior air-barrier. Unfortunately it can't. That's why codes don't allow the assembly you are suggesting. The choice really is binary: Use permeable insulation and vent, or don't vent and use impermeable ones.
Thanks so much Malcolm. I have read articles that the Zip system is not as good with drying as is claimed. It seems then that I have to vent the roof, because the sheathing will dry to the interior. And since it is right on top of old rigid insulation, that insulation will also need venting.
In the 5 Cathedral Ceilings that Work article, solution #2 may be the way to go, giving me ventilation above batts, then the CI polyiso below the rafters giving me protection from interior humidity.
It doesn't look feasible to me that using foam or a flash and batt non-vented assembly would accomplish what I need because that open cell old insulation layer will likely get wet. Or are you saying that it wouldn't be an issue if I seal it with foam? I can see in a standard assembly with the foam right against the sheathing that moisture has nowhere to go but back out through the Zip boards, even if it is less permeable that desired. But in this case, moisture will sit in my Tectum insulation.
Thank you so much for helping me out with this.
Chris
Chris,
If it were me I would choose between Assemblies #1 and #5
Like you I'm reticent to use spray foam unless it is the only option. Venting does mean you lose the additional R-value of the existing layers directly under the sheathing, but yields a pretty reliable roof.
An un-vented flash and batt assembly means no complications from having to vent, all the work done from inside, but does come with the risks of bad foam batches, which occasionally occur.
Thanks Malcolm. My concern with assembly #1 is that I can't reach my Required R-60 (or U-factor 0.024). If I use #2 I can pass the U-factor with R-30 batts and R-12 polyiso (and ignore the meager contribution of the Tectum). I also feel that in the summer, when no one is there for a couple of weeks, the interior humidity level will be pretty high, so the continuous polyiso will help prevent the insulation from getting wet. I'm going to offer #5 as an alternative for pricing purposes. Not keen on the off-gassing and environmental concerns with ccSPF, but it's not that much area and I need to see which is better in price.
One other concern: since the foam in #5 would not be against the roof sheathing but instead against the old Tectum insulation (likely open cell) which has some sort of coating for a finish, how does the Zip board get to dry? Into that layer and then where? I can't fully trust that the new roof was installed perfectly (the condo HOA president really squeezed the contractor on price, so they moved FAST, and were fairly cranky by the end of the job).
Chris,
Do you still have to hit R-60 in a retrofit situation? Here you wouldn't. I don't follow your codes very closely, but there is also a discussion here on how the new 2024 IRC is dialing back the levels required. https://www.greenbuildingadvisor.com/question/irc-2024-coming-soon
You may also find this a useful explanation: https://www.greenbuildingadvisor.com/article/sandwiching-roof-sheathing-two-impermeable-layers But as you say, the downside of any un-vented roof is how they perform if something goes wrong. They just don't have the extra resiliency to deal with water intrusions.
This is in Massachusetts which is very aggressive in its move to sustainability. The 2021 energy code is in effect in this municipality. This municipality is super strict - the inspector will bust a contractor for not having the proper distance between screws. The existing buildings chapter requires treating all alterations as new construction, with only an exemption for cavities exposed during construction.
While this is a renovation, technically this is a new ceiling in that the existing structure and Tectum panels are already exposed, not being exposed by the alteration.
I suppose I just need to have a conversation with the inspector to see how he interprets that.
That all said, looks like I will get pricing for #2 & #5, then see if I can convince the inspector to reduce it to filling the cavity, in which case I am back to #1.
But even if it's R-49, I still need to come up with something more than batts in a 2X10 roof.
I think if it was me this is what I would do, but take this with a grain of salt as what Malcolm said holds true in that it’s not a tried and tested roof. I think I would add a vapor vent at the ridge of your existing roof and flash and batt the interior side. Maybe even using an intello membrane on the interior as well.
I think the breathability of zip comes down to the limitations of osb.
Thanks for your response. If I have the ridge vent but no soffit vent, would it still breathe?
I just checked doing a standard vented roof with ResCheck and I pass using the R-13 polyiso below, so that would seem the simplest solution. Also trying to keep costs down so I'd rather not do the foam if I can avoid it. It's a rural area and the foam guys need to drive more than an hour to get there - at my client's cost, of course.
A vapor diffuse port is not really a ridge vent and it does not “breath”. It allows for the diffusion of incidental trapped moisture via a high perm membrane at the ridge. Joe Lstiburek has a lot of good information on them and has used them so save failing sip roofs. The are code approved in climate zone 1-3 in place of standard venting (with some requirements). Anyways it would (or should) be allowed in your zone as you would actually using the flash and batt to reach code. But if you are unfamiliar with it, it may not be an ideal solution. I would recommend you research it a bit on building science, there are a bunch of articles.
Thanks. I learn some much from this site. Since I am not familiar with the method and my contractor may also not be, I think I'll stick with the tried and true. Not enough time in the day to read through everything here and on Joe Lstiburek's site, but I'm making my way through. :-)