Insulating Basement with Poly Over Sill Plate

I’m in the process of finishing my basement, and trying to figure out if I should remove poly sheeting before adding insulation. I currently have 6mill poly sheeting running from sill plate down to a drain tile in the floor around the entire basement, similar to the attached photo except no stud wall built yet. Purpose of the poly is to channel water down wall and into drain tile. I’m planning to insulate according to the https://www.buildingscience.com/documents/information-sheets/basement-insulation article, but it makes clear that “No interior vapor barrier” should be used to allow for drying to the inside.
I’ve got 2″ xps that’s ready to install over the poly, but thinking I should remove the poly sheeting first. Will I have issues if I leave the poly up? Seems like the interior surface of the XPS should be warm enough to avoid condensation. I’m in NY climate zone 5.
GBA Detail Library
A collection of one thousand construction details organized by climate and house part
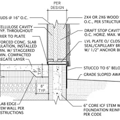
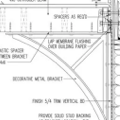
Replies
That poly between the block and the back of your foam insulation isn’t an “interior vapor barrier” in your application. What would be a problem here is if your wall was block, foam, batts, poly, drywall, in that order. The poly is now on the interior side of the stack up, and could potentially trap moisture in the wall.
There is no need for the masonry foundation wall to dry. Your rigid foam would count as a vapor barrier there anyway. I would leave the poly in place, but keep in mind that with it pressed against the wall, it won’t do much to help with drainage. You would need a dimple mat here to help with drainage if that’s important.
Bill
Short answer: assuming that the polyethylene on the wall is doing its job correctly, and draining water into the below-slab gravel, leave it in place, cover it with closed-cell spray foam (or XPS, and don't forget to air seal and tape the seams), and call it done.
Longer answer: I just responded to comments saying that "we can't use a vapor barrier in foundation insulation; keep it 1 perm or higher"--check out that discussion here:
https://www.greenbuildingadvisor.com/question/basement-vapor-barrier#comment-212813
But what you have is basically an interior drained system: it intrinsically involves a Class I (0.1 perm or less) drainage layer, to direct bulk water into the below-slab gravel. These types are assemblies are shown in the links below:
BSI-041: Rubble Foundations
https://www.buildingscience.com/documents/insights/bsi-041-rubble-foundations
BA-1108: Hybrid Foundation Insulation Retrofits: Measure Guidelines
https://www.buildingscience.com/documents/bareports/ba-1108-hybrid-foundations-retrofits-measure-guideline/view
Also, what you're showing is similar to the AVID system shown in BA-1108 (see 3.3 Building Envelope Services, Inc. (2008) AVID System, page 19).
Thanks for your insightful replies! Your comments and the linked documents support my design and give me some assurance I'll be successful. In the 10 years I've lived in this house, I've only had small amounts water coming through the walls (weeping) twice and both were due to clogged gutters in a downpour. I'm now better maintain the gutters, but as a precaution I installed a drain tile and the poly as part of finishing the space since I was replacing the basement floor anyway.
I've attached my wall assembly plan below and some in-process build pics in case others are looking for a similar solution. All XPS joints will get taped or caulked, and the interior wall cavities will not be insulated.
thanks for this detailed explanation of what you did. How is it working out? How did you attach the foam board to the wall? I'm worried about comprimisng the poly? Did you put the foam board in front of the dimple board?
We’ve been enjoying the finished basement for a couple years now and very happy with the results. The space stays warm in winter and cool in summer, and doesn’t smell like a basement or have moisture or humidity issues.
The foam board insulation was attached to the wall using Christmas tree fasteners. Not sure if that is correct name but a google search of that term will show you what they look like. You drill through foam, poly, and into block wall, then lightly hammer the fastener in which pins the foam to the wall. Was concerned that this punctures the poly, but hasn’t been an issue. Wanted to glue the foam up but can’t do that with poly under it.
I did not use dimple board behind the foam. Just block wall, poly, foam. I don’t expect to get bulk water, and the foam could also help in that case, but the poly is like belt and suspenders. Poly is cheap and easy to install, so I figured why not.
Here’s a pic showing the fastener in place. Tried to minimize the amount used. All seams taped or filled w spray can foam.
Plasti-grip makes anchors like that ("Christmas tree anchors"), as does Hilti. I like them too -- they go in quick and easy, and tend to be pretty reliable.
Bill
You could save some money here and use the cheaper foamular 150 version of XPS. The higher compressive strength of the 250 version is not needed here.
Bill