REMOTE walls using Roxul products

I’ve been on here previously to gauge everyone’s thoughts on the building plan for our new house, and I was curious about the opinions out there on what we are currently thinking. We’re building in northern Oakland county Michigan climate zone 5. The house is a 2357 sq ft ranch with a walkout basement. We’ve considered just about everything, but here’s where our heads are at the moment:
1) I think we like the idea of doing superior walls for the backfilled foundation walls, with the exposed walls being wood framed (for ease of attaching cladding and framing windows and doors).
2) 2×6 exterior walls with roxul comfortbatt mineral wool in the stud bays and 4 in of Roxul Comfortboard rigid mineral wool on the exterior including on the exterior of the backfilled superior walls. (two 2 inch layers). With 1x furring strips to attach the siding to. http://www.roxul.com/products/residential/where+to+insulate/contractor#/
I like the “greener” aspect of this stuff compared to foam.
I know the 4 in of ext insulation satisfies the minimum thickness suggestions, but I’m not exactly following the REMOTE wall suggestion of having 2/3 of the insulation on the outside of the sheathing – any problems here?
3) For the building wrap, DuPont tyvek commercial D, with a plan to tape the OSB seams with Siga Wigluv tape.
4) foam under basement slab (4 in XPS or roxul comfortboard cis – again I like the idea of the mineral wool better)
5) framed wall on ceiling under the trusses so the exterior building wrap can be continued from up the walls to across the ceiling. (The continuous air barrier service chase idea.)
6.) Weathershield Endurashield fiberglass picture and casement windows.
Any thoughts on the buildability or cost effectiveness of these ideas would be appreciated. Thanks.
GBA Detail Library
A collection of one thousand construction details organized by climate and house part
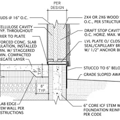
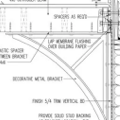
Replies
Brian,
Because your wall sheathing can dry out in both directions, I don't think you have to worry about the 2/3 and 1/3 rule.
I wouldn't use housewrap as your ceiling air barrier if I were you. I think that you will run into buildability issues if you do. If you want a ceiling service cavity under your ceiling air barrier, I would use OSB or drywall as the ceiling air barrier.
I agree with Martin about the 1/3 2/3 rule not applying in this case. It's a very nice plan. The drawbacks I see are the cost of the mineral wool boards, and the fact that putting siding over them is a little more difficult than putting it over foam.
Similarly mineral wool under the slab is less straightforward than using foam, and is probably expensive by the time you get the high compressive strength version. If you want to avoid most of the environmental impact of XPS, EPS is a good alternative--doesn't have the substantial global warming impact of the blowing agents used in XPS, although it still has the fire retardant chemicals. For under the slab, it certainly doesn't need fire retardant--I suppose you could try to work with an EPS supplier to buy some without fire retardant. (Unless you are building over an abandoned coal mine that has ongoing problems with uncontrolled underground fires.) In any case, EPS is cheaper than XPS, per inch and per unit R-value, even taking into account any degradation from moisture underground.
ARTIC wall_REMOTE with variations
This is a wall section that makes a lot of sense to me. I don’t especially care for foam in many designs, bugs (ants and termites) seem like a real threat, and since most walls seem to get wet, I like walls being able to dry, preferably in both directions. Exterior mineral wool helps address these concerns. I'm also interested because I live nearby, and if you find a builder and HVAC designer that understand this design and are willing to build it, I would like to get their names.
You reference the REMOTE wall. There is a version of that named the ARTIC wall by Thorsten Chlupp that you may find worth investigating. There may be other good sources, but you can look up articles Chlupp’s Sunrise house, and there is an extended thread on GBA started by Lucas Durand on 2/25/2011, “The SunRise Home”. Chlupp himself adds many comments, along w/ John Brooks and others.
[There is also a somewhat parallel thread over on JLC about the same time entitled “Outside insulation with cellulose.”]
Ignoring that he uses tons of cellulose in his brutal Alaskan climate, of particular interest (aside from the novel, multi-faceted energy and energy storage systems) is the compact pressure boundary and service core on the ceiling. He ends up with a plywood attic deck that allows the energy heel trusses to be rolled out on top of this deck. The details of how to do this are explored a bit in the thread, but the plywood ceiling is built on top of 2x4s. I can’t tell from your description how you intend to do this part.
I’m no builder, but this approach seems safe and easy. Now just spray the whole box of plywood (four walls and ceiling) w/ a liquid applied membrane and you’ve got something that should easily yield good air sealing and it’s all protected. And you’re set up to put in a robust and cost-effective vented attic w/ blown cellulose as deep as you like it.
As pointed out in one of those two threads, another difference from earlier REMOTE examples: The structural sheathing is no longer OSB, but a more vapor open plywood.
Andrew,
It's worth thinking through whether the service space and separate ceiling make sense from a couple of perspectives.
- If the purpose is as a service chase, what services can be accommodated in the 3" deep space? There is generally no plumbing in ceilings beyond vents which go straight through vertically. It's too shallow for duct work, so is it really necessary just for the few electrical ceiling fixtures?
- The deck to stand trusses on may make sense for DIY builders. It never takes my crew more than a day to stand the trusses. We don't find it a dangerous or particularly complicated task.
- The additional cost around here for the ceiling on a 1500 sf house would be roughly $2500.
- Does the ceiling provide significantly better air sealing than a other approaches such as poly or air-tight drywall?
There may be other benefits I've missed, but it seems like a lot of work for little return.
In Michigan PWF(pressure treated wood) basements are common and well proven. PWF will certainly save many $!. The typical PWF basement uses 2x8 16" OC sheathed with 3/4" PT plywood and is easily filled with mineral wool bats then covered with airtight drywall, some use OSB, (with mineral wool an interior air barrier is necessary) for an r20+ basement. Mineral wool under a slab is EXPERIMENTAL, The highest density mineral wool board is expensive and only offers 7 PSI compression strength. If you are going with "unusual" why not consider Perlite under the slab, it is more economical than plastic foam and offers r3/"+. 4" of mineral wool board stock is a very pricey choice and adds great complexity around windows and doors Consider a double stud system, 2x4 walls with sheathing (air barrier) on the outer face of the inner wall, 2 1/2" space between walls, insulated with mineral wool bats. The bats are the lowest cost mineral wool and about 1/3 the cost/r sq ft of rigid boards.. With the double stud walls exterior sheathing of fiberboard is optional and window/door installation is straightforward.
Jerry, I'm not sure it's fair to say sub-slab mineral wood is experimental anymore.
https://www.greenbuildingadvisor.com/articles/dept/musings/sub-slab-mineral-wool