Remodel – Insulating a permanent wood foundation (PWF)

Background
We recently purchased a log home built on top of a Permanent Wood Foundation (PWF). It’s a ranch style (26’x47′) single story. Built in 1980. We have completely gutted the basement. We are down to the 2×6 stud walls 1-foot on center of the PWF. Previously the house was heated via a wood burning furnace and electric baseboard heat, which have both been removed. We had geo-thermal installed utilizing the duct-work that was in place for the wood burning furnace. It’s a ground source heat pump made by Water Furnace (5 Series).
When we gutted the basement, the walls had wood paneling on top of the sheetrock. The sheetrock was not taped or mudded. Behind the sheetrock was a vapor barrier that was stapled to the studs and the stud cavities had unfaced batt insulation. When removing the batt insulation we could feel it was a little damp near the bottom in a few spots. The batt insulation filled the cavity and there was no gap behind it, or at the bottom. The batt insulation was in contact with the concrete because the concrete was poured over the bottom plate. There wasn’t any mold. The basement did have a very slight damp/musty smell to it. The carpet and pad was installed directly on the concrete which may have been the culprit for the damp smell.
The only time I’ve seen water in the basement was when we had a heavy rainstorm come through in the early spring and the frost had not let up out of the ground yet. Water was coming in through the wood sheeting on the PWF in a few spots and pooling in the bottom of the stud cavities. Which reminds me, the soil where the house is built is all sand. When they dug the 300′ trench for the geo, it was all sand. That trench was 8′ deep, and 8′ wide.
We are in climate zone 6A, Eau Claire, WI area. Onto my question…
We were considering spray foam insulation but it is extremely expensive and we are concerned about the breath-ability of the walls. I have ordered and gone through Joe Lstiburek’s book, “Builder’s Guide to Cold Climates” where he states that the wood wall is warm and will dry to the interior. The book shows how to assemble a wall on new construction and has the rigid insulation on the exterior. I like the idea of the rigid insulation on the exterior… but I’m curious if I would have to install it ALL the down to the footing, or if it could be installed from the top plate to 16-18″ below grade? Then on top of that… how could I make the transition from the logs to the rigid insulation as the rigid insulation will now be sticking out three inches? As I stated in the beginning, it’s a log home, with full logs. So, I can’t carry the rigid insulation all the way up to the roof line. Also, how would you retrofit the rigid insulation around existing penetrations (water faucets, electrical service coming in, windows, etc)?
OR… do I just follow the 2015 American Wood Council (AWC) guidelines for PWF and insulating on page 15? http://www.awc.org/pdf/codes-standards/publications/pwf/AWC-PWF2015-Commentary-ViewOnly-1411.pdf As I type this out and think about it, I’m leaning towards the AWC guidelines because super sealing and insulating the basement isn’t going to “make-up” for the insulating values of the logs. Also, the previous batt insulation was there for 36 years and there wasn’t mold… so, it works. If I go this route, I will just have to spend some time insulating the rim joists with rigid insulation and Great Stuff spray foam..
Looking for some guidance / advice. I’m not afraid of digging in and doing the work. I just only want to do the work once. There will be two bedrooms down there for my kids. I want them to be comfortable.
GBA Detail Library
A collection of one thousand construction details organized by climate and house part
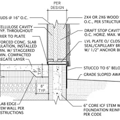
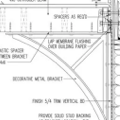
Replies
Jeep,
If your basement gets water entry after a heavy rainstorm in the early spring -- "Water was coming in through the wood sheeting on the PWF in a few spots and pooling in the bottom of the stud cavities" -- then it's not a good candidate to be converted to finished space ("two bedrooms down there for my kids"). Before finishing these rooms, you absolutely have to solve the water entry problem.
This might require re-grading, waterproofing, fixing the footing drains, or changing the backfill to free-draining material. Whatever you do, though, you need to solve the water entry problem before you put bedrooms down there. For more information on these issues, see Fixing a Wet Basement.
Q. "We were considering spray foam insulation but it is extremely expensive and we are concerned about the breath-ability of the walls. I have ordered and gone through Joe Lstiburek's book, Builder's Guide to Cold Climates, where he states that the wood wall is warm and will dry to the interior. The book shows how to assemble a wall on new construction and has the rigid insulation on the exterior. I like the idea of the rigid insulation on the exterior, but I'm curious if I would have to install it ALL the down to the footing, or if it could be installed from the top plate to 16-18 inches below grade?"
A. The best way to insulate your basement walls is definitely to install rigid foam on the exterior of the walls. The second-best way to insulate your basement wall is with closed-cell spray polyurethane foam on the interior side. Ideally, the insulation would extend down to the footing. But if your budget doesn't allow full insulation, the part of the wall where insulation is most needed is the top half of the wall.
Q. "How could I make the transition from the logs to the rigid insulation as the rigid insulation will now be sticking out three inches?"
A. The top of the rigid foam (on the exterior of your building) needs to be finished with metal Z-flashing. This should be installed as close to the bottom log as possible. You'll need to do your best to slide some metal flashing in the crack below the bottom log, and have that metal flashing lap over the top of the Z-flashing.
Q. "How would you retrofit the rigid insulation around existing penetrations (water faucets, electrical service coming in, windows, etc)?"
A. The water faucets (frostproof sillcocks) need to be replaced with new, longer sillcocks, or the existing sillcocks need to be repositioned. The penetrations for the electrical service will need to be flashed. The windows will need exterior jamb extensions and new exterior sills.
Q. "Or do I just follow the 2015 American Wood Council (AWC) guidelines for PWF and insulating on page 15? http://www.awc.org/pdf/codes-standards/publications/pwf/AWC-PWF2015-Comm . As I type this out and think about it, I'm leaning towards the AWC guidelines because super sealing and insulating the basement isn't going to 'make-up' for the insulating values of the logs."
A. The choice is yours. The AWC guidelines aren't based on building science. These guidelines are a compromise. The guidelines were developed in hopes of promoting wood foundations without incurring high expense. As you noted, "When removing the batt insulation we could feel it was a little damp near the bottom in a few spots." This type of dampness may not matter for an unfinished basement, but it's not a good idea for a bedroom.
Considering (a) the fact that your basement experiences occasional water entry, and (b) the fact that a robust waterproofing and insulation solution will be expensive, you may conclude that the best use of your basement is as a place to house mechanical equipment. It might be cheaper and easier to build an above-grade addition for the two bedrooms you seek.
I respectfully disagree with Martin, who is openly hostile to PWF! How can he justify the assertions about the origin of the guidelines and their lack of basis in building science, was he involved in their generation, has he even talked to anyone who was? The best way to insulate your basement is NOT exterior foam! I do however agree that the water leaks absolutely must e fixed FIRST. The exterior poly water barrier (it should be at least 6 mil poly from 8" above grade to the granular footings) needs to be "restored" and the site grading and water runoff fixed so it follows the guidelines you obviously have. It may (probably not) also take replacing some of the backfill with free draining material. But the best way to insulate, after addressing the water problem is to follow the PWF guidelines, especially the 2" gap a above the bottom plate, it is there to allow draining of any water that does get into the cavities without wicking onto interior finish materials. Either fiberglass or my preference mineral wool bats will work well. The performance of the insulation will be degraded unless you achieve a good air barrier with whatever interior finish material you use. In other words, the drywall should be air tight.. Even without an air barrier moisture in the insulation or condensation are NOT issues, the design is based on wet wood which will dry out if there is proper drainage. DON'T waste good money on spray foam! Your problem was clearly caused by the builder NOT following the guidelines about the 2" gap at the bottom, fix that and correct the other "mistakes" and you'll have a warm dry energy efficient green basement, far superior to concrete!. FWIW I'm presently in the process of building a PWF basement and have talked to more than one of the authors of the guidelines.
Jerry,
I stand by my recommendations. When warm, humid interior air contacts cold plywood, the result is condensation. Fibrous insulation does not prevent the humid indoor air from contacting the cold plywood. That's why exterior rigid foam is a good idea: it raises the temperature of the plywood to reduce the chance of condensation.
Martin,
And as the proverb says" it the dog hadn't a stopped to take a dumo he'd a eaten the wabbit"
With a reasonable interior air barrier there won't be any warm moist air, what warm air there is will have the outside air's dew-point and not ever condense. The aforementioned guide shows poly (probably no longer the best choice) as an interior air barrier. In any event the wood structure is designed to be wet, so condensation is harmless and will eventually dry/drain out (drain is the more likely as the condensation will first occur within the insulation).. I've previously asked here about the purpose of that 2" gap in the PWF guidelines. Well I finally found the answer, from one of the authors of that guide, it is as I said to prevent wicking and to allow dripping of any condensate into the drainage provisions. Advocating exterior foam on a PWF is nothing more than a blatant attempt to eliminate the clear advantage (low cost insulation) of PWF over concrete. A PWF differs from interior wood walls in a concrete tub in that drainage is available for any condensate which is not the case in a concrete tub.
Deleted
Jeepasarus.
Spray foam 3 inches deep inside cavities 12" OC assuming that it really is r21 only results in an r 12 wall because the thermal path through the studs is only 3 inches. Five and a half inches of mineral wool is also r21 or more but because an additional two and a half inches of stud is the thermal path results in r 15. The lower cost of mineral wool will at least partially pay for a quality interior air barrier and that's were it quits being economically wise, as you have said you have other places to reduce heat loss with better cost/benefit ratios.
Thank you for the links! The Connecticut story sure debunks the myth that concrete is forever!
The actual limit of the life of a PWF is truly unknown but they sure don't crumble even when mistakes were made. The only known degradation is due to fastener corrosion and if the guide was followed those effects are at least 500 years away.
Jerry: The CT crumbling concrete is strictly a rare inappropriate aggregate material issue- the exception that proves the rule. Barring that sort of problem concrete may still not be forever, but long enough from a human or US home lifecycle point of view.
For the ~20,000 homes affected it's a real PITA to fix, but still not always an irretrievable disaster unless it's allowed to go for too long. Hard strapped home-buyers without the means to fix the affected house are facing a financial disaster though (and their lenders are potentially taking a serious hit.)
I got involved with a house in Farmington CT last year where the homeowner was concerned that it was "one of those" houses, but thankfully the symptoms of that house were attributable to other, less expensive things to resolve, and the foundation looked pretty good. The house was the right vintage, and there weren't records as to where the concrete came from, but the foundation walls and slab were in very good shape, despite some minor settling.
I don't see how it can be livable until you stop the water problem. The only real way to do that is to excavate the perimeter to the footer, and once you are at that point, why wouldn't you insulate the outside?
Deleted
Its your call, but I wouldn't be comfortable with anything less than digging down to the footer, and properly waterproofing the out side with a drain layer, gravel, fabric, and a french drain to daylight. wood+water=rot and mold no matter what the supposed claimed life is...
I've seen ptl posts rot, and stainless steel corrode
Deleted
Jeepasaurus,
Most people, particularly homeowners building fences, don't make the distinction between the types of PT wood that are available, and don't use ground-contact rated PT when they should. Hopefully most builders that use wood foundations, and have to go through an approval process, can be assumed to have used the right PT lumber