Recommendations for permeable wall paper

New home in Zone 7 (West Yellowstone, Montana): We will have 4″ of XPS on the outside of our R-19 fiberglass-insulated 2×6 walls. Because XPS, especially with taped seams, has very low permeability, these walls will need to dry to the inside. Sheetrock and latex paint will work, but what about wallpaper over sheetrock? I understand that vinyl wallpaper has very now permeability. Does anyone have recommendations for a good quality permeable wall paper? One that is durable and will stay up on the wall?
GBA Detail Library
A collection of one thousand construction details organized by climate and house part
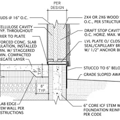
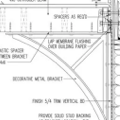
Replies
Hi Ken.
This is a great question and I hope some GBA members who have researched this topic chime in. I have little knowledge of wallpaper except that there are many types of vinyl, which should be avoided in your situation. There is also foil wallpaper that would likely also be a bad idea for you. I imagine you want to look at paper and cloth types of wallpaper, however you may need to look into what they are printed and finished with, as well, to make sure that that aspect of the material doesn't limit permeability.
Please let us know what you learn about this; I'm sure it's a common question.
This has always been my issue with cold climate walls drying to the warm side. The choices for interior finishes is limited. No heavy wall paper, mango mud, etc. How are we to prevent future homeowners from doing what they want with paint and wall coverings? Will there be a disclosure at the time of sale that only permeable latex paint can be used or risk the possibility of moisture accumulation in the walls? Over the lifetime of a house walls are painted over and over again each time lowering the perm rating of the wall. This is a weak building system in my opinion. This house with all the exterior rigid should be fine whatever they put on the walls. Those with standard batt insulation and a low perm cold exterior sheathing is a different calculation. I am all for the variable perm air barriers to limit air movement and keep moisture out of the walls in the first place.
Doug,
I agree. It leaves the house too vulnerable to the types of occupant behaviour we should reasonably expect over time. Walls should be designed to dry to the outside, or both sides. Relying on drying to the inside is risky.
Thanks for the thoughts. I think I will stick with my planned design as I don't know if I can find a spray foam contractor in West Yellowstone. I've been following a number of designs, but mostly CCHRC's REMOTE Building Manual: http://cchrc.org/media/REMOTE_Manual.pdf. Maybe people in Interior Alaska know not to put impervious wall coverings inside exterior walls? We did make the mistake of putting vinyl wall covering inside some of our exterior walls in our current zone 6 home with no ill consequences, but I know zone 7 may be different.
Ken,
Your exterior insulation is more than enough for condensation control in your climate. The only time you would need drying potential is if there are bulk water leaks from windows or doors. If this is a new build and you pay attention to those details, there is very little possibility of this happening.
Permeable interior makes the assembly a bit more robust, but not enough to worry too much about it. My own home is similar with a true interior poly vapor barrier and exterior semi impermeable rigid insulation, no issues at all with it.
Ken,
My interdiction against relying on drying to the inside was too general.
Walls with a lot of exterior insulation behave differently than those we commonly think about. A wall with nothing but exterior insulation doesn't need the cavities to dry in any direction. You could say that as all the control layers are outside the studs, the "wall" is really outside the studs too - or put another way, the wall cavities are just another part of the conditioned interior of the house. That changes when a portion of the insulation is also within the wall cavities. When it becomes a problem depends both on the proportions, and the climate. Your house, with 4" of rigid exterior insulation doesn't rely on any significant drying to the inside. I'd put up whatever wall paper you wanted.
>"We will have 4″ of XPS on the outside of our R-19 fiberglass-insulated 2×6 walls."
Can I convince you to change the insulation spec?
R19s are one of the crummiest insulation products currently on the market. The very low density makes them more like air filters than air retarders- the barely slow down any infiltration leaks that might try to sneak by/ through your exterior insulation. When compressed to 5.5" in a stud bay the density goes up only slightly and the R value drops to R18, more than a 5% hit in performance.
https://s3.amazonaws.com/greenbuildingadvisor.s3.tauntoncloud.com/app/uploads/2018/08/08074629/Compressing%20fiberglass_0-700x310.jpg
By contrast, R20s and R21 "cathedral ceiling" fiberglass, and R23 rock wool batts deliver their labeled R value at 5.5".
R21s are a significant up charge from R19s, but R20s should be only slightly more expensive now that they're being manufactured in high volume due to more recent IRC minimums calling out R20.
Similarly, 4" of XPS is labeled R20, but is only warranteed to R18 (90% of labeled R-value- a 10% hit). It's early years performance is somewhat higher than at 1 or 2 decades, a temporary boost delivered by the HFC-soup blowing agents used (predominantly HFC134a). At full depletion it's performance is the same as EPS of similar density- about R16.5-R17. If you are still around in 50 years and willing to pay a qualified lab to test a sample you can probably collect on that warranty- save these for your files:
http://insulation.owenscorning.com/assets/0/428/429/464/c8fb7b76-244f-4f88-b3fc-548908c8843c.pdf
DOW's warranty is for "only" a 10% hit at 15 years:
http://msdssearch.dow.com/PublishedLiteratureDOWCOM/dh_098b/0901b8038098ba21.pdf?filepath=styrofoam/pdfs/noreg/179-00022.pdf&fromPage=GetDoc
Worse yet, those HFC blowing agents are extremely powerful greenhouse gases, giving XPS by far the largest CO2e footprint per R of any insulation material in common use today:
https://materialspalette.org/wp-content/uploads/2018/08/CSMP-Insulation_090919-01.png
By contrast, both EPS and polyiso are blown with much lower impact hydrocarbon blowing agents. In the case of EPS the vast majority of the blowing agent leaves the foam while still at the factory and is recaptured, not vented to the atmosphere. With polyiso it's more complicated (facer types make a difference), but the CO2e impact of the blowing agents for polyiso is still less than 1% of the XPS blowing agents. The 2lbs density roofing polyiso is roughly comparable to HFO-blown spray polyurethane on that chart, while 1lbs density foil faced polyiso sheathing about half that of HFO blown polyurethane, comparable to mineral wool.
At 4" Type VIII or Type II EPS will run about R16.5-R17 (the same as depleted XPS), but it's R-value is stable over time, and it's vapor permeance will be north of 0.5 perms, compared to about 0.2-0.3 for XPS- it can still dry toward the exterior slowly/seasonally.
At 4" fiber faced 2lb roofing polyiso will be labeled R22-R23, but will average about R19-R21 average during the winter in your stackup (but higher than labeled during the shoulder seasons). Foil faced sheathing polyiso will be labeled R24-R26 @ 4", but would have a similar R2 hit in wintertime performance, higher than labeled shoulder season performance. It's overall performance will be as high or higher than XPS, even when the XPS is fresh.
As a general rule EPS and polyiso are about 20% cheaper per labeled-R than XPS, but at a given thickness foil faced polyiso is slightly more expensive per inch, but has a ~20% higher labeled-R than XPS.
Thanks for the extensive thought and details. Wow! A lot here to read and think about. The main reason I was considering XPS was to maintain a slightly higher R-value outside the sheathing (to keep the dewpoint outside the sheathing), and 4" of XPS pushes the equation to slightly over 50% outside. West Yellowstone can sustain some pretty cold temps. Good to be doing this now: “The architect’s two most important tools are: the eraser in the drafting room and the wrecking bar on the site.” (FLW)
Dana,
After reading and researching:
1) I can get Type IX EPS, 2", R-8.8, for $$22/board. For 4" all around, that would cost $1600 less than the XPS.
2) I can't find any R-20 fiberglass, but R-21 will add $400 to the total cost.
Therefore, overall, $1200 less in total cost.
I also intend to insulate on the outside of the basement foundation walls with 2" of foam. Would this Type IX be OK in that application?
If so, this would be an easy switch.
Thanks for your thoughts.
Ken,
The IX EPS will work great on the exterior of a basement wall. Type IX EPS is pretty rugged stuff. It's strong enough to insulate a concrete slab. For an Abrams tank.
XPS is a scam and a threat to the environment. The stuff should be banned.