Re-roofing and insulating a shed roof: UPDATED with more questions

Our mid-century modern home in Maryland/DC region has one large room that has a 3:12 pitch shed roof (14′ high on east side, 8′ high on west side). It has 2×12 rafters sitting on the walls on each side (the low side has a 2′ overhang and is vented at the soffit; the high side terminates on the wall and has venting through the rafters and fascia overhanging the wall about 2″). It is currently insulated with fiberglass insulation that was not terribly well installed (in 1977). It is western exposure. Under the rafters is poly sheeting and 1/2″ drywall. The building has 2×6 and 2×8 walls and has poly vapor barrier; everything has been carefully airsealed and the windows are fairly airtight for their age. The heat gain on sunny days above 75 degrees is significant. On the more frequent 90+ days, in the afternoon, I cannot maintain a temperature even with the a/c running constantly. The thermostat is located in this room. I plan to have standing seam metal installed on this section of roof. I’m also considering a solar array which would be on the roof above this room. I want to take the opportunity to add insulation when we re-roof. I see a couple of options and want to hear what others would argue is the proper approach. Option 1) re-roof, add the solar array, and hope that the extra layer of solar array decreases the heat gain in the room. Option 2) remove existing roofing, existing plywood decking, spray foam between the rafters (closed cell?), lay new decking, ice/water and slip sheet of synthetic underlayment (per manu. directions) and then add metal roof (making this an unvented assembly); or 3) remove existing asphalt roofing, add 2″ of foam on existing decking, add second layer of decking, and then ice/water and slip sheet of synthetic underlayment (per manu. directions) and then metal roofing. The third option seems troublesome since the existing venting is going to be right in the middle of the two layers of insulation–will that cause all sorts of potential moisture problems. Can that be solved simply by blocking the venting at top and bottom and leaving essentially a sandwich filling of air? Any other options I’m missing? Thanks for any guidance.
UPDATE 3/29/2021:
We were visited by a 4″ diameter branch that punched a nice hole into this roof last night (I was sitting directly under it when it came out of the 100′ oak–yikes). Anyway, I made a discovery: What I thought were 2x12s are in fact 2x10s. And while there is a soffit vent and a “ridge” vent at the top of the shed roof, the entire insulation cavity is filled with the 9.5″ fiberglass. I see no signs of moisture, but that will obviously not work once I get a metal roof up there. So as I see it, my only option, working from above, is to remove the sheathing, have a company install closed cell into the cavity, resheath it, and proceed with my roof install. If I try to put a 1.5″ vent space and use Rockwool, I just won’t get an insulation level that makes the time investment possible. And I absolutely cannot leave the current insulation as is without a vent chase (so it seems, in spite of 50 years with no sign of problems). Anyone see another way? ** (I suppose I could add 2″ strips onto the tops of the joist to make the cavity 11.5″ and thereby go back to the 9.5″ rockwool + 2″ vent channel plan). Thanks for all the guidance so far.
GBA Detail Library
A collection of one thousand construction details organized by climate and house part
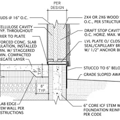
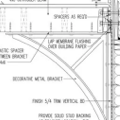
Replies
Hi Michael -
Option 1: Nope, if you have the opportunity to increase your roof insulation, and heat gain from the roof assembly seems significant, add insulation as part of the roofing project.
Opti0n 2: This one seems about right but you could introduce a vent space between the new structural sheathing and the standing seam roof cladding (using diagonal furring to properly support the standing seam panels while also accommodating drainage and air flow).
Option 3: Nope, those closed-off vent chutes will be convective loops up to no good in your roof assembly.
Peter
Michael,
If your 2x12 are insulated with about the right amount of fiberglass (~9"), that is a pretty decent roof. Adding more insulation to it will not significantly reduce your thermal gain.
Those MCM houses usually have a lot of glazing, if you have west facing windows that would be a much larger source of heat than your roof. If this is the case, the 2' overhang helps but usually not enough. A larger sunshade or pergola with plants would be needed.
Thanks for this. The problem is it's not well insulated. There is a lot of compression, some areas where animals long ago soiled or tore out parts of the insulation, etc. Using my thermal camera, I can see lots of areas where the batts don't meet for a few inches, and in a few spots multiple square feet are missing. So it's time for the subpar 1977 job to be corrected.
Thanks for the helpful replies. It seems like improving the existing insulation is the way to go (so tear off the decking, reinsulate, reapply new decking. Given the size (16x40), that's going to be more than a day of work (!) and coordinating a spray foam company will be a challenge. Is there any drawback of doing the "cut and cobble" method--put in multiple layers of EPS or XPS (benefits of one or another?) that are cut to fit in the rafter bay; foam seal perimeters using cans. The advantage, too, is that I can leave the vent and make a 1 or 1.5" air channel (use 5 layers of 2" foam).
Cut and cobble is a poor approach overall. It should never be used for an unvented assembly, as it is nearly impossible to get the air sealing right. With a vented assembly, you will have a little more leeway, but it will still perform worse than spray foam. Cut and cobble also involves a large amount of labor, and is only worth considering if you are doing the labor yourself, and don't pay yourself very well.
Replacing the batts seems a better alternative than cut and cobble. If you want air sealing use the airtight drywall approach.
UPDATE: Getting closer to pulling the trigger on this and would welcome and appreciate some more advice. I'd like to remove the existing roof and as much of the decking as necessary and as little as possible to get access to do the reinsulation. I assume I'll need to take off the lower row due to some water damage and the upper row to access, and probably every other row in order to access the cavities. I can work in stages of a few sheets at a time.
I've got 2x12s 16" o.c. and was hoping to put in R-38 Rockwool. I've read Martin's article about cathedral ceilings and preventing windwashing in the vent chute.
Complicating this is that no one in the area seems to be able to get the R-38. They have the unfaced batts for 2x4 and 2x6 walls.
Could I put in one batt for 2x4 and one batt for 2x6, and then put on top of that a 1" piece of EPS (maybe the styrofoam sold for basement walls that are already 14.5" wide?). That EPS would handle the wind washing but still be vapor-permeable. That would be 10" of insulation and allow a 1.5" vent chute. If so, should I spray foam the edges and tape the butt joints? Or just compression fit the EPS? It seems like this does not have to be airtight?
I could pull this all up and just have closed cell sprayed in (and a whole lot less work for me, but with 1/2" ply upwards of $42 per sheet these days, I'm reluctant to rip it all up), and then have an unvented assembly, but there still seems to be a lot of debate about unvented cathedral roofs in our climate.
Any other suggestions welcome. Thanks.
Wind washing is none existent with high density insulation:
https://www.rdh.com/wp-content/uploads/2017/10/Van-Straaten-Windwashing.pdf
I have never done chutes with mineral wool, just do a good job with the install and make sure the vent channel is clear.
You'll have a hard time pushing insulation down along rafters without removing all the roof sheathing, I guess if you are careful it is possible but won't be easy.
I usually go for R14+R24 batts when needing R30+ roof insulation. The R32 or R38 batts are hard to get and are pricey.
Close cell SPF roof would seal up your ceiling quite well but since it is not applied to your roof deck, you would still have to keep the assembly vented. Despite the high center of cavity R value of the ccSPF, the assembly R value would be pretty close to the same roof with HD batts. Open cell SPF would be a cheaper solution in this case.
Assuming it was a plywood deck, if it was my own roof, I would be tempted to dense pack with cellulose over the existing batts and air seal the heck out of the ceiling bellow. Strap out the roof deck and top vent the whole assembly under the metal roof. This isn't as robust as a roof with exterior insulation but can be made to work if the interior permeability is significantly less than the exterior and there are minimal air leaks. You can read about it in section 3.4 Top-Ventilated Deck here:
https://www.buildingscience.com/file/5783/download?token=z_JWop_1