Raising and insulating floor for four-season room

(Edited to correct some of my numbers and add some diagrams)
We are planning to turn our screened, roof-covered, screened porch (approx. 22’ x 14’) into a four-season room. I would love to hear people’s thoughts on our plans for the different areas of the project. Yet, here, I will address only my doubts about the floor.
ANY feedback, even if not to all of my questions, would be very much appreciated!
The floor will need to be framed, as the current floor (a tiled cement slab) needs to be raised, by approx. 9 inches, to the same level as the adjacent kitchen (currently, there is a 5-foot double, French door between the kitchen and the porch). The floor will be a continuation of the kitchen’s hardwood floor.
For the framing and insulation of the floor, I’d like to follow some of the suggestions given by Steven Bazcek in the Journal of Light Construction (I can give the more precise reference if needed). However, there, Bazcek gives suggestions for a floor that needs to be raised by 5 inches in total. His scheme is:
– a 4-mil cross-linked polyethylene wrap covering the existing cement floor (tiled over cement in my case);
– 2-inch x 4-inch sleepers
– 1 1/2-inch EPS foam board between the sleepers
– 2-inch EPS foam board
– 3/4-inch subfloor on top of the rigid insulation, driving 3 1/2-inch screws through the 2-inch rigid insulation and into the sleepers. The diagram enclosed with the article shows two screws, side by side, which of course work very well when joining two sheets of subfloor.
The questions I am struggling with are quite a few unfortunately:
1) The sleepers option, with 2-inch x 4-inch boards, does not seem viable for me, as I have 4 more inches to make up for, in height. I am not sure whether having 8-inch x 2-inch joists (hence placed vertically) can work, as such joists would be only 1 1/2-inch thick, hence perhaps too narrow to receive two screws side by side, to attach the subfloor. Would using even lower joists, 6-inch x 2-inch (sistered to make them stronger?), and screw 2×4 sleepers on top of the joists, forming a T, be structurally sound? Any other ideas I should contemplate, which would not be cost prohibitive? Incidentally, as the existing floor is slightly sloped down away from the house (by approx. 1 inch), the joists will have to be ripped.
2) For sleepers/joists, should I use pressure-treated wood? Should that be used at least at the perimeter, for the three sides at the outer walls?
3) If any of the framing touching the floor will be in the form of sleepers, I read that, even for a 14-foot length, it would be structurally better to off-set them; that is, to have a 6-foot board from each facing wall, and a 6- or 8-foot board joining and overlapping them in the middle. Is that really better?
4) Steven Bazcek suggests using EPS boards. Yet, in storage I have five brand new 2-inch boards of XPS (pink ones, Owens Corning I think), which I bought years ago. So, it might make sense to just buy five more and use XPS. The compressive strength, if anything, is better. So, using XPS instead of EPS should be OK, right? I know that unfortunately XPS is so much worse for the environment, and I will try to get salvaged boards if possible. Incidentally, Bazcek’s article does not mention whether the board that sits on the sleepers and is then covered by the subfloor should be taped at the seams; yet, that would be good practice I imagine; right?
5) Still on insulation, I should be able to adapt Bazcek’s setup so as to use open-cell spray foam between the rafters. I am thinking of having 4 inches of spray foam between the joists, and then the 2-inch XPS foam board. Are there any drawbacks of doing so? (Incidentally, I am not considering rock wool, which would have even better R value, for any parts of this project because we have too many mice in the area, and anything that is not foam would be way too risky I fear. The current plan is that of using open-cell spray foam in the knee wall which will need to be built, and the ceiling, though we also want to use polyiso boards around the whole structure and, inside, on the ceiling.)
6) Following something like the above approach, I should get to approximately R-35 (indeed, likely a little more) for the floor. Will that be enough for zone 5?
I should mention that, when looking at posts about raising floors by 10 inches or so, I have encountered mostly posts that recommend pouring an additional concrete slab over an EPS board, and install sleepers over the new slab. To me and for my project, it seems a pity to fill with concrete what could be filled with insulation. Yet, the raised floor must be structurally sound, not squeak, etc. So, if the above-described approach is not what I should pursue, I’d love to hear folks’ ideas even if they are very critical.
I am adding a couple of diagrams, one found on GBA, the other from the JLC article. They well illustrate the type of approach I would like to apply to this project.
Thanks!
GBA Detail Library
A collection of one thousand construction details organized by climate and house part
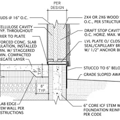
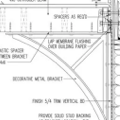
Replies
I would go with 2x10 joists on their edge, ripped to the slope. A 2x10 is 1-1/2" wide which is plenty wide enough to have two pieces of subfloor meet and be screwed in, that's the normal way of doing it. Since it's over concrete I'd use pressure treated joists.
I would fill the joists with fluffy insulation, fiberglass, rockwool or cellulose. I'm a little superstitious about putting fluffy insulation on concrete, so I'd put a layer of foam between the joists. You want the floor to be air-tight, so I would seal the edges of the foam, maybe with spray foam. I don't see any reason why you can't mix XPS and EPS so use up the XPS you have and do the rest with EPS.
Foam is no more mouse-proof than other insulation, which is to say, not at all. You need a physical barrier to keep mice out. Plywood works so long as there are no gaps or holes.
Thanks, DCContrarian!
I am glad to hear that the 1 1/2" thickness of the joists' edge will be enough. That would also apply to 2x8 instead, right? I say that in case I want to go for the approach where the subfloor and hardwood floor "float" over the 2-inch floor.
I will definitely go for pressure-treated wood!
You did not suggest any alternatives to ripping the joist boards to make up for the slope. I suspect that that's the most time-consuming part of the project; yet, most likely there is no way around that.
The alternative to ripping is shimming. If you run the 2x10's in the 14' direction, they only need to be supported at the ends and in the middle to avoid being bouncy, which is what you have to worry about. At the ends you would attach them to rim joists. One end would be shimmed 1", the other not at all. The center would be shimmed 1/2". I would use 3" strips of 1/2" pressure treated plywood for shims. If the joist is resting on the shim at one end and the concrete floor on the other you don't need joist hangers.
It all depends on how even the concrete floor is. If the floor is uneven it's easier to even things up if you have as few points of contact as possible. If it's really bad, shim each joist at its three contact points individually. Plywood comes in 1/4", 5/16", 3/8" and 7/16" so by stacking you can go up in 1/16" increments. Or if you have a table saw you can cut scrap pieces of 2x10 into 1/16" increments.
Note that you will have a 1" gap under the joists at the low end. This needs to be filled or you will be creating luxury housing for mice.
I wouldn't recommend floating the subfloor. Having the subfloor nailed or screwed directly to the joists makes the entire assembly rigid and strong which gives a nice floor that doesn't squeak or bounce. You'll have plenty of insulation under the floor.
(Edited)
Thanks for all these suggestions! My immediate reactions are:
- Better to rip than shim; my floor is fairly even I would say; and I don't want any gaps under the joists, for the reason you're mentioning (that is, the mice!).
- I confess that I had no idea that plywood would not come in 3/4" thickness. That brings up a question about the distance between the joists: 16" or 24". I am tempted to overshoot (if it is an overshooting) and go for 16", even if the article I was referring to indicated a 24" distance (and a 3/4" subfloor, which perhaps was meant to be OSB; I'd like to be plywood, exterior grade plywood - yet, I am a bit confused on the options available: I know we need to go tongue and groove, but I am not sure on what would be an optimal, or even thicker-than-need-be thickness - see below - PROVIDED THAT there are no drawbacks to having too thick of a subfloor).
- Related to the above, especially given the use this room will have - that is, given that it will be completely integral to the house, lived in 24/7, indeed basically an extension of the kitchen, NO squeaking or bouncing is truly essential. I was hoping that the approach I was contemplating, of having foam boards with adequate compressive strength under the subfloor (and, if need be, a thicker subfloor, and joists spaced at 16" instead of 24", and, for sure now, ripped joists laid on the concrete floor for their entire length) would give me plenty of solidity. But you seem skeptical on that approach. To clarify: my intention was not so much that of adding insulation for added R value, but to interrupt any thermal bridging between the concrete floor and the interior, room floor, through the joists. ALSO, I just saw that there is this "Multiply Flooring Underlayment," which adds solidity to floors; have you ever had any experience with that?
For the subfloor I would recommend 3/4" Advantech. https://www.homedepot.com/p/Advantech-23-32-in-x-4-ft-x-8-ft-Tongue-and-Groove-Aspen-OSB-Underlayment-Panel-1012405/202084475
It makes a good floor. The only thing I don't like is that it's around 80 lbs a sheet! Which is part of what makes it good.
In terms of making the addition integral to the house, here's where a lot of people get into trouble. An exterior wall has four layers: a rain and weather barrier, an air barrier, a vapor barrier, and an insulation layer. All four of those layers have to be continuous throughout the entire house. The adage is you should be able to take a plan of the house, and draw each of those layers on the plan without ever lifting your pencil off of the page. What can be tricky is keeping those layers where the exterior changes direction -- and the intersection of wall and roof, or wall and floor -- and at the intersection of new and old construction.
Having one of those layers that is not continuous is like having a boat that is only waterproof on one side of the bottom.
Thanks, DCContrarian!
Noted on the 3/4" Advantech; I'll go for that!
What you say about the four layers is absolutely what I'll have to worry about next. Since this is an addition, and one that has already been built, I need to learn (and I will likely be posting a separate question or two about those aspects) how to best address the ceiling, the walls, and the intersections between ceiling and wall, and addition walls and house wall. As a "preview" of what I have been contemplating: I am thinking of having Polyiso foam boards on all the outdoor surfaces of the structure, with the exception of the roof, and Polyiso foam boards on the room's ceiling, with ceiling strapping on the inside, most likely to install a beaded board ceiling, and strapping outside to install the siding.
I confess that the different layers you are mentioning still confuse a bit; yet, I'd better defer that topic to separate questions on the forum (if you don't mind, when I post such questions, I might send you an alert).
All that said, if you don't mind, let me ask you: do you remain skeptical on having a floor that, from the top down, consists of 1) strip floor, 2) 3/4" Advantech, 3) 2" XPS board, 4) 2"x8" pressure-treated wood joists, with insulation between them, 5) 4-mil (or 6-mil) cross-linked polyethylene wrap, 6) existing tile-over-cement-slab floor? That is, are you still concerned about the foam board layer making the floor not firm enough?
I really appreciate all the knowledge you're sharing. I am finding it extremely educational, and that despite days and days I had already spent looking for information online! Many thanks indeed!
Ripping joists is not too bad if you use an edge guide, basically a straight piece of wood screwed to the joist that you can run a circular saw along. Support the joist securely on sawhorses.
Thanks! It makes sense. It is also somewhat reassuring.
Another thing to consider is ripping the outside joists and shimming the inside ones. That way the outside ones make a nice seal and you don't have to rip the others. I believe that shimming will be less work than ripping. Use one size smaller for the inside ones than the outside ones.
Thanks! I also think that if, prior to putting any insulation into those joist spaces, I carefully inspect the whole perimeter, I would decide to install some metal mesh at places, and keep any critters out for ever. it will be easy to staple it to the wood while, I guess, I could tape or glue it with caulk to the polyethylene wrap. Just a thought.
Since you've been so kind and helpful with your feedback on my question regarding the floor, I thought I should alert you that I have now posted a question in regards to insulating the ceiling - in case you have the time to look at it. Thanks!