Rainscreen advice

I live on Cape Cod and on the waterfront. We are about to start a strip and reside project due to sheathing damage from water intrusion. My question concerns Rainscreen systems. We will be residing the home with cedar clapboards. Originally, I was planning to use 3/8” thick plastic furring strips. I find them pricey and would like to know if it is my best option. If they will outlast other materials then they are worth the extra cost for me. Other design elements I plan to implement include: no venting above and below windows, an aluminum J-channel at the bottom of the water table, above the J-channel I plan to attach a strip of Delta Bug Screen, the house wrap will be a double staggered layer of 30lb felt, sealing around existing flanged Anderson windows/doors and intergrating the felt will use Prosoco R-guard. Prosoco Joint and Seam Filler will be used to fill voids and seams and to intergrate flashings to the sheathing. Lastly, My plan is to provide a small ¼” vent space at both the bottom and top of my walls.
I have devised this plan from my web searching and may be information limited. I’m seeking your advise before starting this costly project. Thanks in advance for reviewing my question and any advice you may offer.
Normal
0
GBA Detail Library
A collection of one thousand construction details organized by climate and house part
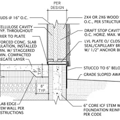
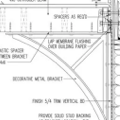
Replies
SteK,
You plan sounds good.
- I wouldn't spring for the plastic battens unless you were installing them horizontally. Use strips of plywood, or if you can afford the depth, 1"x3"s. Wood battens will not deteriorate in the cavity.
- Keep your battens below the window staggered, or dropped a bit, to provide path for air movement to both sides.
- Rather than a 2 stage approach to the bottom of the cavity with flashing and bug screen, consider instead using a perforated U channel as your base. Size it so that your battens fit inside the U. Makes everything easier and more durable. That gives you an opening the full depth of the cavity, rather than the 1/4" you suggested. Something like this:https://www.menzies-metal.com/vent-flashings/perforated-j-channel-rain-screen-low-back
- Because you are on the waterfront, I'd leave out the ventilation gap at the top of your walls, unless you can detail it to make sure no wind-blown rain will get in.
Malcolm & Peter, thanks for the responses. My vent space I’m referring to is in height not depth. I should have stated that this gap at the bottom is lifted above a floating wood deck above a rubber roof. Things are not entirely straight-forward. I don’t want to penetrate the rubber membrane, as it wraps up the sheathing, at the base of the water table. At all deck locations, there are three, I plan to attach the J-channel to the water table trim board (prior to installation) and not the house. At the water table I’m using the Menzies J-channel with the addition of the delta bug screen just above. I don’t think that 0.120 diameter perforations would keep smaller bugs from entering.
If I vent the top of the wall will I still have a problem if the vent is overlapped by the freeze board by a good amount, say ¾”? I will also add the Delta Bug Screen.
With regard to the windows, we plan to cut back the existing Typar (maybe leave a 4” flap) (we'll see when we open it up) and paint it down with the Fast Flash prior to installing and intergrating the felt paper. We will make sure the window/door flange is properly sealed to the Typar initially, Typar sealed to the sheathing, and then integrated with the felt. The trim in the home is custom milled Butternut so window removal is not possible. What options do I have?
Sounds like you are doing what you can in a pretty thorough way. I worry about the top vent getting water in through capillary action, but if it is close to the overhangs it should be fine. Leave more of the Tyvek at the window sill so you can overlap it with the new building paper. And good luck with the project!
Malcolm,
Should I overlap the building paper at the sill with the Typar?
You want all your joints between layers to lap. The existing Typar can be overlapped by the new building paper at the head and jambs, but at the sill you want the existing Typar to overlap the new building paper. You can get an idea of the sequence in this video at around 1:20 onwards: https://www.youtube.com/watch?v=SqP4liutJFs
To add to what Malcolm is saying about overlapping layers, You want to think how shingles work, and make sure the water is always directed away from the sheathing. Anything high on the wall should be on the outside of things lower on the wall so that water running down the surface doesn’t ever get trapped and directed behind a layer of WRB material. You want everything to direct the water to the outermost face of the outermost layer of WRB material.
Bill
Hi Normal -
You are in a tough spot, with the windows. It sounds as though you will be relying on sealant to tie in your new vented cladding to existing windows. That means that while your cladding system is drained and vented, your window installation is not. In such an exposed location, building new, you would flash and drain your rough opening prior to installing your windows.
Prosoco makes great sealants but a face-sealed system is still just that: sealed rather than drained. If you can't afford to reinstall your windows, integrating their drainage with your vented cladding, then just be sure to use backer rod as part of your sealant system.
I did review the Prosoco RGuard steps for application/installation but the 2-page doc I reviewed was not terribly clear on beaded sealant and use of backer rod. You should be careful about the difference between a mastic flashing material and liquid sealant applied as a bead; see this resource: https://www.buildinggreen.com/blog/breaking-bonds-bad-sealant-jobs.
Peter
Malcolm, you recommended that the ventilation gap at the top of the wall should be omitted. In the article Efficient Walls on a Budget on this site Dana Dorsett provides a link to a study documenting how walls react to moisture based on the types of venting used in the rain screen design.
http://www.energy.wsu.edu/documents/AHT_ComparingTheMoisturePerformance%20Of%20Wood%20Framed%20Wall%20Systems.pdf
The study says in the conclusions: "A fully ventilated cladding that includes openings to the exterior both high and low on the wall is critical."
This appears to be especially true in a marine environment.
Scott,
There is a hierarchy of rain-screen cavities. Roughly I'd say it goes like thIs:
- Mesh behind cladding
- Battens behind cladding
- Ventilation at the bottom
- Ventilation at the bottom and top.
They start as just providing a capillary break, a gap for vapour diffusion, a drainage plane - and finally ventilation to aid drying. How many of these features you need depends on climate and the wall assembly. There is no doubt that a cavity ventilated at both the top and bottom performs the best, however so far the evidence here in BC's marine climate seems to show that a rain-screens without top ventilation don't experience any issues, and adding top ventilation may be unnecessary. What I don't know is how the colder climate on the East Coast affects that decision. maybe others with more experience there can chime in.
The Cape Cod waterfront is about as bad as it gets. High humidity during most seasons, hurricane force winds (and actual hurricanes) from all directions, salt air, etc. You need to use pretty much all best practices to survive. I would go for top and bottom venting, with large overhang/counterflashings built into trim to reduce windblown rain entry.
I have some familiarity with Prosoco products. They've got liquid flashing/WRB materials and joint sealants, among other things to make a system of drainage plane products. Very durable. My concern is whether they adhere to and are compatible with felt products. I have not done any research on this subject, and I have had negative experiences with many products sealing to felt layers. Be careful there.
Top venting it is then. Maybe liquid flashing isn't the right choice here? A wide border of peel & stick membrane around the windows, over the old Typar, might work better.
Check out this video:
https://www.youtube.com/watch?v=G8W654jX5h0
The Prosoco rep proposed my solution.
I'm not building a new house, and I don't have any overhangs on several gable walls that face extreme weather.
If I vent the top of the wall using a covered/overlapped vent design, and I want to block capillary water entry into the wall cavity, is there a water break detail that could be implemented and attached, hidden by the overhang, that would redirect the water downward? Thanks.
If you have a sketch it would be helpful.