radiant heat in slab questions

I’m in zone 6, and building a garage (32×44′). There are not many people in my area who know much about radiant heat, so I’m kind of on my own. I plan on 3.5″ of EPS on top of 2″ gravel, then poly, then rebar ( with blocks under to suspend bar and tubing into center of slab height), with 1/2 pex zip tied to the re-bar. I haven’t decided on what source for heat yet. My questions are:
1) what type(s) of pex are acceptable/preferred for in slab? Everyone swears their own product is the best.
2) I figured on using 1/2″ spaced 12″ apart. Does this seem like a good plan (or should I change size and spacing)?
3) Do I need to install anything else in the slab, such as thermostats, etc.? I see max lengths from 200-300′ for 1/2″, and I’m not sure what is recommended. Is there a minimum length to use for pressure, turbulence, inefficiency?
4) Are there any precautions to take to account for the slab cracking at some point (other than saw cutting a bit below the surface?
5) for this size, in this zone, is a high efficiency water heater adequate and/or recommended? Tank or tank-less?
I appreciate any guidance you can offer. Thanks in advance.
GBA Detail Library
A collection of one thousand construction details organized by climate and house part
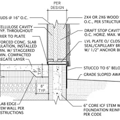
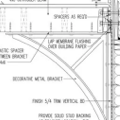
Replies
I would read through one of the radiant design manuals:
https://assets.supply.com/ul_pdfs/712617_ownersmanual.pdf
There is info about spacing, length, dealing with control joints etc.
Tom,
Just a few tips. Akos has pretty much got the technical side for heating details covered.
For a slab of that size, I would guess you are going to pour 5-6". That will give you more grace for placing the pex far enough down to be reasonably secure. You most definitely don't want to cut the pex with a control joint. As I have noted in other threads, I was warned by my cement contractor not to let the pex get any closer than 1" to the surface or the risk of cracking above the pex is greater. My basement slab pour is only 4", so I pinned the pex to the foam then placed the mesh over the pex and then tied the pex to the mesh with zip ties. Yes a big PITA and my labor, but no cracks and no risk of saw dings.
Being under the 6x6 mesh also meant the pex couldn't "porpoise" between ties. If you tie on top of the mesh or rebar the pex will bow and twist between ties. You will find having the pex sun warm much easier to deal with. If it is cold when you work with it, it is pretty miserable. More ties means less bowing, but pick your battles.
If you are really using re-bar not mesh, you might ask about going with fiber in the cement and not doing control cuts later. It is possible to do what I think are called "keyed" joints which are made with what looks like a trowel with a keel. My garage slab (5" - 6x6 mesh) is keyed and has a polyester fiber in it. Roughly 22x23 it is uncracked after five years. Not heavily used admittedly. There are twisted metal fiber as well as polyester and other ones, so check out the properties. I did not go with the metal ones due to cost, but they might be super strong.
Rubber crutch tips fit nicely over the pex ends and duct tape keeps them secure. No random bugs, or dirt to deal with while you set pex and pour. Shark bite fittings helped to simplify connections for pressure testing which you want to do for at least 24 hrs. 1" PVC conduit elbows work nicely for riser guards where the pex surfaces for connection. If you choose to pin first an tie to the bottom side of the rebar, I found landscape pins convenient. I was going into 25 psi recycled XPS which could be a big advantage in holding power.
In regard to the EPS, I do hope you pick the tougher grades, the workers and the process of setting rebar, pex, bar chairs, and pouring all require a lot of stomping around on the foam. I was very grateful for having lucked into the higher psi XPS. Given the climate zone and size of the slab, you might consider more foam thickness. You haven't specified wall and roof insulation or temperature goals, but just remember your floor slab will probably be running above 70F. The ground is pretty much an endless 50F heat sink, so calculate accordingly. If you are planning on multiple garage doors and just tolerable temps then maybe you'll be okay.
Hopefully you mean washed stone, not gravel, under your foam and compacted soils under that. Gravel in my definition is just very course sand with small stone bits. This can hold water in much closer contact to your foam if water gets that far. Not a good gamble in my opinion.
For poly, I found the fiber re-inforced plastic from HD to be a very good and durable plastic to put over the foam and substantially less costly than the fancy ones. Your own call on value and costs.
Do take the time to do one thing I failed to do. Especially if you are going to be bolting down car lifts or other equipment. Make a story tape of the pex line locations based on forever points like support columns or door jambs. I just took pictures and now I am lost. Fortunately nothing in my shop needs bolting down. Anyway, stretch out something like the plastic tapes used for police lines and magic marker the pex positions on the clean side of the tape. Mark them carefully for location and orientation and put them in a box. Someday you might be grateful for being able to roll the tapes out and know for sure that you really are between runs.
If you have natural gas or even propane, you will find that, for the forseeable future, it is the lowest cost way to heat the amount of water you will be pushing about in multiple zones. I would suggest trying to pattern some zones to follow the perimeter in sections as the losses will be greatest there. You might be able to shave the energy and water flow to mid sections. You will likely find discussion of these notions in the pdf Akos provided the link for. I haven't read it yet. On demand water heaters will most likely not be a good match with the temps and flow rates of a radiant system. A reservoir tank and heater tank might be a better way to manage things. I will admit I am speaking above my pay grade at this point. Hope you have some time for planning....
On demand heaters work quite well for floor heat. Officially they should be installed in an open system, but will work just fine in a closed setup (I heat my house with one like this). Most have a pretty low minimum fire, as long as you don't create any mini zones, they won't short cycle.
A condensing tankless, as long you have proper RWT, is also much higher efficiency than a standard tank type water heater.
The one thing to watch is the pressure drop, you do need a beefier pump (Taco 009) or two Alpha circulators in series. You also need to install a larger inlet Y strainer as the built in one is very small and gets easily clogged.