Radiant heat improvement?

I have an ongoing renovation of my own house but any info will certainly apply to other projects that fall into this same scenario or possibly another job that I or others may encounter.
The current conditions are:
1. Hydronic radiant heat installed under existing 3/4″ board sheathing which is under two layers of wood flooring for half of the area, the second half is tile underway, same build-up thickness.
2. 5 loops cover 925 s.f of first floor area, fairly equally sized loops.
3. The insulation under the loops is 2″ polyiso cut to fit between the joists and meticulously foamed in place with a 2″ gap between tubing and top of polyios…give or take.
To improve performance:
1. I will eventually remove all wood flooring but will have to build back up to the same thickness but the next version of the wood areas will be rips of (Advantech?) or some other 3/4″ material to replace the current full area 3/4″ material to allow more heat to transfer and then the final 3/4″ hardwood. Currently, the heat moves through pretty good, but not as good as in other installations where it doesn’t have to fight so hard…and waste energy.
2. The tile area: This is the tough one. In order to maintain the same floor elevation AND properly install tile, I have full coverage 1/4″ fiber rock as a tile underlayment for my tile to flush up with the final 3/4″ hardwood. (above 1-1/2″ of wood substrate. This weekend I began the floor leveling process and ended up adding about 3/4″ of floor leveler to a 10′ x 10′ area to make the world flat after underlayment. In that area, I noticed a significant difference in the “feel” of the radiant in the areas of fiber rock and leveler….well duh.
So, in the hardwood areas, I can resolve the subfloor issues with providing “slots” in my new underlayment, that’s a no brainer. In the tile areas…..I thought about drilling through the entire assembly that will be below the tile (1/2″ diameter holes, every 12″ or so) to allow the heat to move upwards to the bottom of the tile to allow yhe heat to get to where it belongs…to the room. The are where the leveler is is noticeably cooler than the wood flooring
As a gauge tonight (23 degrees in Portland) I tested how it would react to forcing the loops to raise the temperature quickly. The first floor started at 68 degrees and I set the temperature to 72. After an 1-1/2 hours it was there.
I may be over thinking this (heat recovery was not really that bad) but thought I would put it out there.
Any thoughts are appreciated.
GBA Detail Library
A collection of one thousand construction details organized by climate and house part
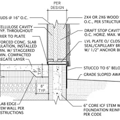
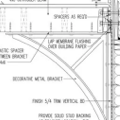
Replies
Robert,
Other GBA readers may have other observations, but here are some thoughts I had:
1. In-floor hydronic heat distribution systems shouldn't be chosen if you want fast response times. There will always be a flywheel effect with these systems. They are slow to heat up and slow to cool. Unless the controls are well thought-out, these systems can easily overheat your house on sunny days.
2. It sounds like you are spending too much time worrying about your "warm toes" experience rather than determining whether your home is comfortable.
3. Once your boiler distributes warm water through the tubing, the heat will be inside your thermal envelope (as long as you didn't make any egregious errors like installing PEX tubing in an unconditioned crawl space). If your thermal envelope is good -- in other words, if it is relatively airtight and well insulated -- then your heat is indoors. Don't worry.
4. In-floor hydronic heat is expensive and has few advantages. As Alex Wilson (or was it Marc Rosenbaum?) has written, "This is a good heat distribution system for a poorly insulated house." Once you improve your thermal envelope, you may prefer a simpler heat distribution system.
I think I was worrying too much after the initial installation of the leveler and tile backer.
I don't think the heat was on all day and when I got home, I was a bit concerned. This morning however, all is good, just took a little while to bring that glob of concrete up to temperature.
Thanks for the other tips Martin. And no, I wasn't worrying about my warm toes but I understand your response. I was using my feet as my thermal imaging camera and noticed a 15 degree difference between the wood and the leveler...had my feet calibrated last week!
My curiosity had to do with removing resistance between the source and the target. One of these days I'll find some time to have it figured out via software as a learning tool for the future.
For now, I'll chalk it up to a knee jerk reaction.
What is your current setup for getting the heat out of the PEX and into the subfloor of the hardwood areas?
There's a large variation in heat-transfer efficiency :
Suspended tube is the worst, with an inch or three of air between the tubing and subfloor.
Staple-up has at least marginal contact with the subfloor providing some conductive heat transfer
Sheet-metal heat transfer plates improve conductive contact with both PEX and subfloor.
Extruded aluminum heat transfer plates will usually better contact with both tubing & subfloor.
Above-the-subfloor tubing approaches like WarmBoard (tm) work pretty well and are very responsive, but expensive to install. Keeping what you have and spending the same cash on reducing the load may be a more effective way of improving comfort AND reducing fuel use, but it really depends on the house, and what's driving the heat load. In your DIY above-the subfloor approach you still have to at least add some sheet metal heat spreaders to get the heat out of the tubing at a higher rate, and distribute it more evenly, otherwise you end up with higher water temp requirements and significant temperature-striping along the floor- hot directly over the tubing and cool elsewhere.
The conducted heat transfer between your feet and tile & wood at the same temperature (and same radiant heat flux) can be deceptive- the tile will usually feel warmer, even if it isn't. Use an infra-red thermometer if you want to know just how much warmer it really is (or isn't.)
Thanks Dana,
The tubing is stapled from below to the bottom of the first layer of subflooring. Between the tubing and the subfloor, there's full joist bay width aluminum flashing (coil stock).
Below the tubing: about a 2" air gap then 2" foil faced polyiso....the basement is always nice and chilly!
The walls need work, heading toward 4" of rigid. I'm not unhappy with the performance, just looking for ways to improve it if possible while my house is still a mess.