R40 Foundation in Zone 7a (ext rigid and int spray?)

Hi All,
We are building a well insulated, tight home in Winnipeg Mb. The client has an unrelenting desire to have as close to possible R40 basement poured concrete walls.
We often use ICF, but coming into the winter here, we made it poured concrete so we can water proof and backfill before its too cold to peel and stikc the ICF.
My foundation assembly is:
2″ subterra
Waterproofing tar
8″pour concrete
2″ Closed Cell spray foam (3″ if I can find the vapor permance for it. It’s currently at .97perm for 2″)
2×6 frost wall 1 ” off the concrete
R15 2×4 Batt insulation
I am looking for opinions about the vapor permeance of the spray foam as we have to dry to the inside in a mixed climate and we have exterior foam.
Thanks for your time appreciate it!
GBA Detail Library
A collection of one thousand construction details organized by climate and house part
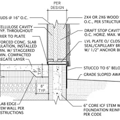
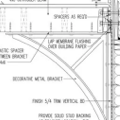
Replies
You don't need any drying ability for the concrete -- concrete is perfectly happy to stay wet forever. Since concrete doesn't need to dry, at all, the perm rating of the insulation on the sides is irrelevant.
I would skip the spray foam here as it gains you nothing, and probably actually complicates things. I would just use rigid foam panels placed directly against the concrete wall. I would absolutely use polyiso here too, as it's a great way to get a lot of R in a relatively small space, and none of the "loses R value in cold weather" stuff applies in this application since you have some exterior insulation and you're mostly going to be below grade too. I would try to put ALL of your interior R value in that polyiso layer, and not bother with batts in the wall -- batts add complexity and risk here.
You can save some space using 2x4's (or 2x3's) "on the flat" against the wall and use 4" square electrical boxes and mud rings to put any electricals in. I'm assuming the poured concrete is the structural wall, so the interior "wall" is just to support interior finishes.
Bill
Thanks Bill. The homeowner is adamant to has a interior frost wall (non-structural) so he can run electrical in the future and make changes easier later on.
Although the conversation has always been to dry to the inside. I’m not concerned about the concrete being wet, I’m concerned about the amount of moisture moving from wet concrete to other materials in a finished basement.
The one caveat is that the foundation under the structural wood basement floor is currently bare, and can dry to the crawlspace. I suppose that should be insulated to the same capacity as above?
Is this not a big conversation as it’s below grade and most recommend only r10-r15 in a Basement?
Seems crazy when we are -40 outside to think that we don’t need to insulate our basements as well as our walls upstairs (taking into account the temperature gradient underground of course).
You can run electrical in a service cavity 1.5" deep the way I described to save some space. If the owner really wants a regular studwall, that's OK (it just wastes some space), but I'd not frame it out any deeper than 2x4s (all that is needed), and I would absolutely not include any batt insulation in it. Put ALL your R value in the foam board, which is a much safer way to go.
If you seal the walls, no moisture will move. There are various ways to do this. You can use a waterproof coating that is also a vapor barrier, then put the foam board over that. You can use foil faced poly iso with the seams taped, and rely on the foil facer as a vapor barrier. You can also put a sheet of poly on the wall with the polyiso over that (which might be simplest from a construction operations perspective). Any of those options will seal the wall and prevent moisture from getting into the interior space. WIth those concrete walls, you should focus on keeping moisture OUT of the interior, and not on allowing the walls to "dry" to the interior.
Once you get below the frost line, the temperature of the Earth is relatively constant, usually up around 50F or so, but always over freezing (which is why it's the "frost" line after all :-). Since the warmer temperature of the earth relative to outdoors means there is a lower thermal gradient, insulation becomes less important. The reason you seen R10-15 listed for foundation walls is because of this, with more R value having less impact since you're insulating against a smaller thermal gradient.
Remember that the purpose of insulation is to reduce the flow of heat from one area to another, not to hit an arbitrary R value target. That means that if the "cold side" temperature is less in one area, than another, you can insulate that area less and arrive at the same amount of energy flow, and it's that energy flow target that you're really after.
Bill