Blown-In Fiberglass Insulation Against Roof Sheathing

I have a house in climate zone 7 that seems to be very cold with lots of cold air infiltration. A few contractors have said to address the roof first. I have a cathedral ceiling that consists of:
1. 1/2 inch tongue and groove pine,
2. 1 inch of xps foam board,
3. 2×12 rafters have 6 1/4 inch fiberglass batting
4. 3/4 inch osb sheathing
5. Ice and water shield (unsure how far up the roof it goes)
6. 30 year asphalt shingles that were new in 2016.
The ceiling is penetrated by exposed joists and a large chimney. There are both soffit and Ridge vents.
I have been told to fill the rafter cavities, with blown in fiberglass.
From the research I have looked at my interpretation is I wouldn’t want blown fiberglass contacting the roof sheathing. I am looking for clarification and guidance. Also if there isn’t the easy blown in solution which side should work be done from the, interior or exterior and why.
Thank you in advance,
Pete
GBA Detail Library
A collection of one thousand construction details organized by climate and house part
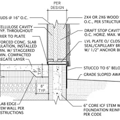
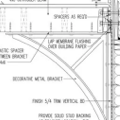
Replies
> lots of cold air infiltration
Your first priority should be air sealing with testing to verify. But OK, maybe not in areas that you know will be torn apart for other reasons.
> I wouldn’t want blown fiberglass contacting the roof sheathing
Correct unless there is lots of foam above the sheathing.
Maybe you have already done these, but building code (eg IRC 806) and the search button in the upper right are helpful.
Thank-you Jon,
We got to where we are now looking to stop the feeling of air blowing in through internal walls. Decayed D log, insect chewed xps, batting in stud bays, and tongue and groove interior finish( no sheathing, no wrap) definitely allows for room for improvement. I have not had the house tested, yet,, as I feel it's a guaranteed fail for many reasons at this point. But everyone that has been out thinks increasing roof insulation is the first step towards comfort.
Thank you for the code. I hadn't been to anything that official, just lots of opinions.
Caveat: I am NOT an industry pro.
The fact that your 2x12 joists are only filled with 6 1/2" of fiberglass insulation suggests the builder was trying to leave room for the airflow to work from your soffit to ridge vents. Do you know if there were any kind of channels installed to protect that path?
For example, on my house I used a product called Accuvent (https://www.brentwoodindustries.com/construction/accuvent/), but your builder could've built a channel out of drywall or rigid foam.
If there aren't any channels, it seems to me it might be bad to fill the entire rafter cavity with insulation.
Also, do you know if the foam board behind the pine was sealed (with tape, for example) to provide a good air-sealed layer?
Thank-you Mike,
There is no vented barrier installed. As for the sealing of the foam board I have not removed any interior finish to examine it other than at gaps and cracks in finish carpentry. I do know it is Dow Styrofoam 40 tongue and groove. However, none of the pictures of the build show taping on the exterior wall foam, there weren't any ceiling photos.
In too few of words I guess my initial question. Was along the lines of would you tear up a Six year old roof and sheathing or tear down 1800 Sq feet of tongue and groove, foam board. And batting to install dedicated vents. Typing it out loud seems like coming In. From the outside would be less hassle. I think the max r value currently would be around 24, assuming 6.25 Owen's corning was r 19 in 1988. Maybe this place was intended as a summer residence only.
Thanks for the link. I believe through one of Kiley's links I ended up at the smartvent website and watched a gentleman tape multiple vents together and insert them up from the soffit end. That would leave a 3 inch void plus whatever compression of the batting the blown in would do. So I guess the next questions would be how much does blown fiberglass compress fiberglass batting and is there any rough guesstimate of what an achievable r value would be doing it that way.
Thank you kindly.
Your thinking is correct for unvented roof assemblies—you don’t want fiberglass against sheathing in your climate zone. As Martin Holladay puts it this article : “Experts usually advise builders that you can’t install fiberglass insulation directly against the underside of roof sheathing. If you want to install fiberglass between your rafters, you have two basic choices: either include a ventilation channel between the top of the fiberglass insulation and the underside of the roof sheathing or install enough rigid foam above the roof sheathing to keep the roof sheathing above the dew point during the winter. These rules were developed to prevent damp roof sheathing.” You said you have soffit and ridge vents. In this article, Five Cathedral Ceilings that Work, you will find a detail for how to insulate with fiberglass in a vented assembly, as well as other types of assemblies.
Thank you Kiley,
I think attempting inserting some sort of rigid channel will be my next step. Though rough math I have the rafter length at 22 ft minimum. I think a trial insertion is definitely warranted and if that doesn't go well at least an attempt to pull an assembly up from the Ridge vent? Thank you for the links. The smartbaffle website was helpful and Thats definitely a missing piece to one of the five ceilings that work. Any thoughts on the current xps in place of the recommended foil faced polyiso? At only one inch that's only semi vapor permeable. Thanks
Installing more fiberglass isn't going to help stop the air leaks. With exposed rafters, a chimney, T&G ceiling, and untaped foam insulation, that assembly leaks like a sieve. To improve thermal performance and comfort, the first step is to stop air leakage. After that, more insulation helps. Consider air leakage like an open window. It doesn't matter how much insulation you put in the roof and walls if you leave the windows open all winter.
Unfortunately, addressing the air leaks in your construction may be very difficult. Regardless, it is a required first step. A blower door test with air leakage diagnostics (smoke pencil, etc.) will help you to quantify your overall air leakage and may help point to some of the easier areas to address. You should start by working with a home energy performance contractor, not an insulation contractor. The home performance guys are usually better at looking at the house as a system.
While I have no experience with the system yet, your house could be a good candidate for the Aerobarrier system. The company says that it can be used in finished construction to seal hidden air leaks. You might want to look up a local vendor if you can find one.