Questions about retrofitting a “slab on grade” in zone 6.

DYIfarm
| Posted in GBA Pro Help on
This is a construction site on hold.
My folks home here on my farm is partially gutted and awaiting insurance monies and planning completion to recover it from a pipe freezing and flooding incident this winter.It is a home built in 3 stages (1950
’s-70’s?) and all of the 3 conjoined pours are “slab on grade”. The home is located on heavy soil (clay) with almost certainly no insulation, vapor locks or drainage under or around on the slab. This home is located in zone 6, the site is known to have a high water table. The western wall slightly below grade due to settling. Up to 75% of the slab has (believed to be asbestos) tile glued to it. The home had carpet as long as we have owned it, except for the bathroom that has tile. The bathroom floor sweat all summer. We are sure the carpet was wicking moisture off the slab elsewhere we just couldn’t see it.
Things we are considering:
Installing drainage and a retention wall on West side of home (multi functioning as a walkway or patio.Installing insulation 4”deep all around building.Sealing (in the asbestos tile) and leveling transitions and filling cracks- prior to the application of a or a liquid vapor lock .Installing an air-gap w/ vapor lock between sealed concrete slab and final flooring.Using foam attic insulation and installing some sort of AC as a way to control moisture as a whole. FYI We have been told, by a roofer that the attic is not designed to vent, but haven’t spoken to contractor about it yet.
Questions:
Do we need to insulate the whole perimeter?
Will that be effective if there is no insulation underneath?
Can a liquid vapor lock (epoxy type sealant) be effective in these circumstances w/ the asbestos inclosed in it?
Is a subfloor critical prior to installing final flooring layer?
How do we know if the moisture is coming from condensation accumulation v/s transmission thru the slab?
Things we are concerned about :
Budget.Trapping vapor in various undesired places and ways.Asbestose management.Energy efficiency.Adding value to home.
GBA Detail Library
A collection of one thousand construction details organized by climate and house part
Search and download construction details
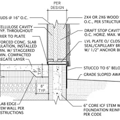
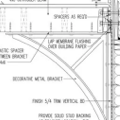
Replies
The usual meaning of "vapor lock" has no relevance to the building assemblies. Do you in fact mean "vapor barrier"?
>"The home had carpet as long as we have owned it, except for the bathroom that has tile. The bathroom floor sweat all summer. We are sure the carpet was wicking moisture off the slab elsewhere we just couldn’t see it."
In a zone 6 climate that is almost certainly due to the temperature of the subsoil being lower than the ventilation air & room air dew points in summer, not ground moisture coming up from below. While a vapor barrier (yes, liquid epoxy types can be effective) is a good idea in general, it's unlikely to resolve the sweating issue. In fact putting a vapor barrier on top of the slab will prevent the slab from being able too take up moisture from the room air. The real answer is insulating the slab.
If digging in an exterior perimeter drain (good idea, in any house built on clay soil) it's an opportunity moment to add slab-edge insulation. In US climate zone 6 the IRC 2018 code minimum slab edge insulation is R10, down to a depth of 4' below grade. But even at half that depth it would still make a difference in how cool the perimeter of the slab itself is, warming it up considerably. That could be done with 2.5-3" of EPS foam board extending all the way up to the foundation sill for the framing.
Putting an inch of EPS and a 6 mil polyethylene vapor barrier under a 3/4" subfloor for the finish floors would be enough to prevent summertime moisture issues in the finish floor & subfloor, and would still be financially rational on a long term basis on energy savings in your climate & deep subsoil temperatures.
The slab-top insulation would be in addition to, not in lieu of slab edge insulation. The subfloor can be screwed to the slab with masonry screws, or if one double-layered some half-inch plywood as the subfloor it could be left floating. Even Type-VIII EPS or Type-II (1.25 or 1.5lbs per cubic foot nominal density) have more than sufficient compressive strength for this application.
Ok great- Thanks!!! I'm so happy to have your input!
SO... It seems you are saying we should do all of the above, so let me clarify.
Yes I meant Vapor Barrier. tnx & sry
my current goal is to be able to understand the ideal combination for desired results vs fiscal return. The desired result is to control the moisture so it dosent stink of mildew and we stop experiencing mold blooms on surfaces or sweaty floors in the summer. We however don't expect to make it perfect. I read a US dept of energy study done for zone 6, ( see attachment if u like). It prepared me for the notion that the cost of insulating the homes perimeter would not be a significant energy savings on its own. However it's not the energy savings we are after foremost- it is maximizing the moisture remediation benifit relative to the financial cost of the remediation.
In response to all your good info: numbered by paragraphs as they appear in your reply.
1. I have 2 diff quotes for about 3k each to fill cracks, level where needed, and install a mesh layer for adhesion to existing tile prior to the application of a "liquid vapor barrier". but it sounds like you are both skeptical about its ability to prevent condensation.
2. Perimeter drain and insulation, we were considering drainage on the west side where it is below grade- and is a straight wall with a drainage ditch in line to receive the h20 flow. the rest of the home is not as straight forward. I've attached a drawing of the home. It sounds like you would recommend drainage and insulation on all sides?
3. EPS recommendation ie Sub floor - FYI we were thinking of a sub floor exclusivly to provide an insulated air gap and vapor barrier b4 finished flooring is installed.
My general take away question is if we are ok w/ loosing some height should i just cover the existing tile w/ a floating sub floor. = slab, phisical vapor barrier, 1/2" risers, plywood, insulation , plywood attached to the risers then flooring? skipping the epoxy type vapor barrier? At that point where is the added benefit to adding insulation and drainage beyond the west wall that has surface water running right into it ? I get that we will have less condensation if the slab is entirely insulated from the perimeter, but is it reducing the potential for trapped moisture that would corrupt the lumber that we are avoiding or heating costs? (this home is kept heated in the winter at a maintenance lever and to a greater degree as little as 10 days a month in the winter for occupancy) so cooling costs are of greater concern ( no ac now). Can we get away w/ a sub floor vapor barrier and ac to manage the rest? We are very concerned w/ the clay site and the age of the slab- that we might open a can of worms, damage the grounds/lawns w/ machinery and not get great perk w/o a lot of material replacement (displacing my mothers established gardens all the while). We will move the plants and bushes if we must but- we aren't shooting for perfection here just better. Thanks in advance.
DIYfarm -
You have an awful lot to "unpack" in this post but here goes, hoping to add to Dana's lengthy response:
1. Do we need to insulate the whole perimeter?
Yes
2. Will that be effective if there is no insulation underneath?
It can be, particularly if you "fan out" the insulation per frost-protected shallow foundation details: https://www.greenbuildingadvisor.com/article/frost-protected-shallow-foundations.
3. Can a liquid vapor lock (epoxy type sealant) be effective in these circumstances w/ the asbestos inclosed in it?
As Dana stated, we think you mean vapor barrier. I sincerely doubt you will be able to get any epoxy paint to bond to those tiles; you need to research/investigate this.
4. Is a subfloor critical prior to installing final flooring layer?
Generally, a subfloor is structural and with slab on grade, you don't need a structural subfloor.
5. How do we know if the moisture is coming from condensation accumulation v/s transmission thru the slab?
I would think that condensation on the slab is taking place in the summer, while transmission through the slab is something happening pretty much all the time. In this blog, I discuss how to properly measure moisture content of concrete: "Extending the Reach of Moisture Meters" - https://www.greenbuildingadvisor.com/article/extending-the-reach-of-a-moisture-meter.
Best - Peter
Ok great- Thanks!!! I'm so happy to have your input!
Please see my clarifications /answers and new questions to Dana above incase you see any more input opportunities. So far we have not found any contractors that see the whole moisture picture, only their lil part....so any info is great. I cant open the links w/o subscribing- so I will Look into that. Thanks again.
>"4. Is a subfloor critical prior to installing final flooring layer?
Generally, a subfloor is structural and with slab on grade, you don't need a structural subfloor."
A subfloor is often necessary to have sufficient fastener retention for some types of flooring (such as hardwood.)