Questions about air sealing old 1×8 sheathing, housewrap, foam insulation

(zone 4c here)
I’m having a hard time finding much information about how to air seal old horizontal 1×8 board sheathing. House wrap seemed like the clear choice until I realized that you aren’t supposed to tape the bottom seam. That seems like a huge flaw. Perhaps I could instead air seal the sheathing, by using flashing tape on every single board seam. It would be tedious and more expensive, but it wouldn’t leave a huge gaping opening around the whole perimeter of the house. The house is rather small (simple 900sf single story), so the cost/labor wouldn’t be unbearable or anything. The house wrap would then just be the WRB, not the air barrier.
If I’m adding foil-faced polyiso foam over the housewrap, and the wall system is then expected to dry to the interior, what is the purpose of using permeable housewrap at all? Could poly sheeting be used, in principle? (I don’t see any reason to actually use it, just trying to understand)
A final, somewhat strange question: I’ve only seen inside of my wall once, where they opened it to install the mini split head. The cavity was empty (no insulation) and it appeared that there was asphalt felt underneath the sheathing — in other words, when I looked into the hole from inside the house, I saw a black surface. They cut the hole, and then the sheathing was visible in the cut hole. Does this present any problems? Is it OK to have the sheathing sandwiched between external rigid foam (and housewrap) on the outside, and asphalt felt on its inside face? If not, what are my options?
GBA Detail Library
A collection of one thousand construction details organized by climate and house part
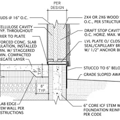
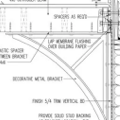
Replies
Nick,
If you are installing foil-faced polyiso on the exterior side of your wall sheathing, then the polyiso is your air barrier. Caulk the perimeter of the wall when you install your polyiso, and tape the polyiso seams.
You guessed correctly: when you install foil-faced polyiso on the exterior of your wall sheathing, the permeance of the housewrap is irrelevant. Make sure that your polyiso is thick enough to keep the stud cavities above the dew point. For more information, see Calculating the Minimum Thickness of Rigid Foam Sheathing.
You may also want to read How to Install Rigid Foam Sheathing.
The asphalt felt will not cause any problems with your wall assembly.
Finally, if you are fixing up your walls, you should strongly consider filling your empty stud bays with dense-packed cellulose insulation.
I don't think you need to tape every sheathing seam. You're creating a new enclosure with the foam, and if you tape the seams in the field there you should have it well sealed in the middle.
I would worry about the top and bottom and around openings (doors & windows). They are tough to seal under the best of circumstances. If you can arrange it, get a blower door test done before you start siding to see if you've got any major leaks at the perimeter you can seal with tape, gaskets, foam, caulk, etc.
Thank you Martin. I'm still not clear about what to do at the bottom of the wall (also, above windows). Should the housewrap be taped at the bottom? It seems that it is commonly advised against, so that any errant water can drain out. Should the foam be caulked to the housewrap at the bottom? This presents a similar concern. If neither are sealed at the bottom, then essentially I am relying on the "squish" of the foam against the house to reduce air leakage through this area. The drainage plane will be at the sheathing and the windows will be innie-style.
I'll definitely be blowing in cellulose, possibly even before I re-clad the walls. We currently have vinyl siding, so it should be very painless to have done.
Nick,
There shouldn't be any water behind your housewrap.
Housewrap is often taped at the bottom. That's what is recommended in the Tyvek installation instructions: "For maximum air leakage reduction (when installing as an air barrier), seal wrap at the bottom of the wall with sealant (i.e. DuPont Weatherization Sealant), DuPont Tyvek Tape, or DuPont StraightFlash."
Thanks for clearing that up, Martin.
Martin, in the October 2013 issue of JLC, Allison Bailes has an article ("Top 10 Building Science Secrets") in which he states (pp.41-42) that housewrap isn't installed to be an air barrier. He goes on to say "To qualify as an air barrier, housewrap would also need to be sealed at the bottom edge, but there's a good reason why this should never be done: You'll trap water inside when it gets behind the housewrap and can't drain out at the bottom of the wall."
This is contrary to your comments (post #4). Perhaps you and Dr. Bailes can sort this out for us. In doing so, it occurs to me that which approach to take (seal the bottom of the wrap or not) might depend on whether or not the siding is installed over a rainscreen gap and how carefully any tears in the wrap were taped prior to the application of siding.
Dick,
Can I imagine a failure mechanism or flashing error so egregious that it allows liquid water to pool behind housewrap at the bottom of a wall? I guess. Is such an egregious flashing error likely? No.
Here's how it works. Most wind-driven rain is stopped by the siding.
A small percentage of that water gets past the siding. It is intercepted by the housewrap and flashing. Ideally, there is an air gap between the back of the siding and the housewrap to improve opportunities for drainage and to facilitate rapid drying. But even if the wall has no air gap, the housewrap is still there to intercept any water that got past the siding.
Even though we talk about rainscreen gaps as if they allow liquid water to drain, it's very rare to have so much water get past the siding that you really see any water drip out the bottom of the weep holes at the base of your wall. What really happens is that the water is absorbed by hygrosopic materials (the back of the siding, the furring strips) and slowly dries out.
Now, the situation anticipated by Allison Bailes requires a reverse flashing lap, an enormous quantity of water, and enough of an air gap between the housewrap and the sheathing to allow liquid water to reach the bottom of the wall. Here's my opinion: it's not going to happen.
Even with a reverse flashing lap, the water will be absorbed by hygroscopic materials -- in this case, the sheathing -- and will slowly dry out by diffusion (evaporation). That's why housewrap is vapor-permeable.
So, Martin, you are arguing that Dr. Bailes isn't necessarily correct in his statement about the sealing of housewrap at the bottom edge; I understand your reasoning, and I would in general agree with you. Still, can we invite him to comment on this, given his contrary opinion on sealing the bottom edge? Dr. Bailes, are you tuned in to this one?
I think it depends on the budget and the scope of work. Given the importance of air sealing and how hard is it to seal the number of seam I would consider multiple strategies.
I think putting a house wrap over the sheathing and then rigid would give house 2 layers of protection. The house wrap could be taped and sealed to make an air barrier. Then installing the polyiso over would provide another layer. You would get better performance with them combined. .
The housewrap would not be the WRB rather the polyiso would be.
If you really want to air seal that siding, you can wrap it in a Grace Ice and Water shield type product; there are even some spray based products.
It is not really necessary if you seal that poly-iso well when installing
Bob,
Grace Ice and Water Shield is a vapor barrier, and should never be installed on the exterior of sheathing (unless, of course, you are following the PERSIST method and have no insulation between the studs). And it should certainly never be installed over siding.
I'm still doing research for this project and my main concern now is flashing of the windows. They're vinyl windows. I assume they're the second set of windows on this 1950 house. Everything I've read says it's best to remove them and completely re-flash the rough opening, but this seems like a massive addition of work, adding disruption to the interior of the home, and I wonder if there is some way around it. It seems that plenty of people re-side without removing their windows, but apparently none of them have decided to explain how it's done on the internet.
Nick,
In a rainy climate, windows can leak, allowing water to enter the wall assembly. The two most vulnerable water entry locations are the bottom two corners of the rough opening.
Whether or not your house is vulnerable depends on the annual rainfall in your location, the direction of the prevailing winds, the width of your roof overhangs, and the skill with which the window installers flashed the rough openings. While some homes have disastrous rot, most are fine. It's difficult to predict how vulnerable your walls are to this problem.
Many people who install exterior rigid foam leave their windows in place rather than removing the windows to properly flash the rough openings. If you want to take this route, you have to be willing to accept the risk of water entry -- a risk that might be very small or not so small, depending on the circumstances.
First of all, you need to examine your walls for signs of water entry when you have the siding removed and are installing your foam. If you see signs of moisture, you know that you have to start from scratch with the window flashing.
If your walls are dry and you've decided to leave the windows in place, then you need to install new exterior window sills. These sills must be sloped, and must convey the water that strikes the window to the exterior. Of course, these new sills must cover the new rigid foam. The easiest material to use is painted aluminum flashing. Use a heavy gauge, and try to get the sloped flashing under the windows. Pay attention to water-sealing details at the corners, where the sill meets the jambs, because those are your most vulnerable areas.
Do a good job and keep your fingers crossed.