Question regarding unvented roof assembly

I’ve got a question about insulating the roof of a small mudroom addition. The dimensions are 5′ x 8′ with a 6/12 simple gable roof. Because of the size of the project and the relatively low headroom inside, I decided to go with an unvented roof assembly and a cathedral style ceiling with exposed rafter ties. The fascia boards etc have been installed so venting the roof and changing the design is not an option.
The roof is brand new standing seam (galvalum type product) over 5/8″ Zip System. There is no iso board or any other kind of insulation on the exterior. There are no roof penetrations.
I’m in Climate zone 5. There is no heat source currently in the addition and eventually there will be a wall hung electric heater which will only be used when needed. There is no plumbing of any sort in the addition either.
The original plan was to hire a spray foam contractor and let him or her worry about it. However, all of the spray foam companies in my area have minimum requirements and it would have been too expensive to pay their minimum fee for such a small job.
So then I was planning on doing a cut and cobble installation with xps and canned foam. I was planning on firring the rafters out to achieve the desired R value and then going over the rafters with a continuous layer of 1/2 inch xps to prevent thermal bridging. This sounded like a lot of work. I’m sure I would have taken the time to get the details right but since I have now read a bit more on the subject, it seems that this is too risky of a plan.
A couple of days ago I read an article on this website saying that one way to do it would be to spray a layer of foam against the bottom of the roof sheathing. Then I could fill the rafter bays with insulation bats (the article probably stated the preferred material but I can’t seem to find the article). I would most likely go with mineral wool. Then, even though I’ll most likely be installing t&g boards on the ceiling for looks, I’ll first sheetrock and tape, thereby creating an air seal.
The total square footage of the bottom of the roof sheathing adds up to about 40 sq ft. I was thinking of buying the Touch’n Foam 200 kit. If I’m understanding the specs correctly I should get several inches of depth out of the kit. At that point I will see how far I need to fir the rafters to achieve the desired R value with mineral wool and that should do it.
I’m hoping that I’m remembering this correctly. It seems a little weird that there is nothing in the assembly to prevent thermal bridging but I guess the idea is to seal the bottom of the roof sheathing and allow the rest to dry to the interior.
Does all of this sound right? What am I getting wrong? Thanks in advance.
GBA Detail Library
A collection of one thousand construction details organized by climate and house part
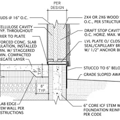
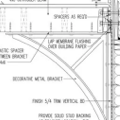
Replies
Hey Joseph,
I'm not sure of the coverage of the froth pack you are considering, but your approach will work if you hit the necessary R-value (R-49 in your climate zone) and get the right ratio of closed cell spray foam to fibrous insulation. This is probably the article you were reading and it should answer all of your questions: http://www.greenbuildingadvisor.com/article/how-to-build-an-insulated-cathedral-ceiling
And here's a FHB article on working with DIY spray foam kits that may be helpful: http://www.finehomebuilding.com/2011/07/14/spray-foam-for-the-rest-of-us
I almost forgot to mention that an airtight drywall ceiling will also help mitigate the potential risks of an unvented cathedral ceiling.
Thanks Brian. You're right. That probably is the article. Thanks for the other links as well. I'm heading out the door right now but will read those later today.
An airtight drywall install would involve adhesive between the framing and the back of the sheetrock, correct? I've read about that method. I'm not sure if that's what you're referring to.
Unfortunately, nothing is that simple, but if this addition is as straightforward as it sounds, getting the ceiling airtight shouldn't be too tricky.
First, I recommend air sealing your addition from the exterior with a combination of caulk/adhesive around the perimeter of the sheathing and taped sheathing seams.
You'll need some sort of blocking above the top plates to spray the foam against, which will also seal any leaks and penetrations in the top plates. Then if you seal the wall drywall to the top plates and if you don't have any penetrations in the ceiling drywall, that should do it.
Of course at this point it's probably worth sealing the perimeter of all of the drywall and the electrical boxes as well.
There are still more air sealing details to consider, like your foundation-to-plate joint, and any wall penetrations to the exterior, but you are getting close to a very tight assembly now.
Thanks for your replies, Brian. This is very helpful.
As far as the perimeter is concerned, that ship has sailed. I've got the house wrap on there, inside corner boards where the structure meets the main house, and the soffits and fascia boards are all in. So it would be a can of worms to slit the typar and expose the osb seams. I don't have access to the foundation/bottom plate joint anymore either.
I do have blocking at the horizontal osb seams. I suppose I could run a bead of caulk or canned foam around all of the wall framing where it meets the inside of the osb. Would that suffice?
The only penetration to the exterior is the box for the outside light which is in the gable. Since I'm doing a cathedral ceiling, that penetration will be part of the wall assembly.
Penetrations through the double top plate of the wall are just a few holes for the romex and they are already sealed with fire retardant foam.
There will be ceiling penetrations where the exposed rafter ties meet the roof framing. I'll probably give myself some nailers around the rafter ties in plane with the rest of the ceiling so the drywall isn't unsupported there.
Beyond that, there are only two single gang boxes to worry about detailing in the walls.
But I guess that brings me to my next question- why do I need an airtight wall assembly? How does that affect the roof?
I've already got blocking ripped to the angle of the rake standing in a vertical orientation in each rafter bay, perpendicular to the top plate at the eaves. It seems like the remaining 4 inches of the top plate could be spray foamed as well, sealing off the roof assembly from the rest of the framing. What am I missing?
Joseph,
It sounds like you are doing all of the right things given where you are at in the process.
Yes, sealing around the stud bays with caulk or spray foam will be helpful.
As far as the walls are concern, just think about paths that air could take. For example, if your electrical boxes are leaky, air can infiltrate we walls. If you haven't sealed penetrations in the top plate, that air can get into the roof assembly.
In general, the idea is to keep conditioned air in conditioned space and outside air, outside, unless the exchange of air is thoughtfully controlled with ventilation.
Keep doing what you are doing and I don't suspect that you are going to have any problems.
Sounds great. Thanks again.
One more question. There are a couple of romex runs in the ceiling assembly. Is it a problem if they become encased in spray foam? Should I worry about the wires overheating?
That should not be a concern provided that the circuits are not overloaded.
Thanks, Lee. That's what I thought, but I was second guessing it after seeing some people posting concerns in a home inspection forum.
> Would that suffice?
When it comes to air sealing, don't guess about what will be effective. Use a blower door (or even a DIY window version) to find the leaks. Use multiple air barriers if you can.
Code (R806.5) requires R20 or ~3 inches of closed cell spray foam. But I wouldn't believe their R value (de-rate it some) or build to code minimums. 200 bd ft applied to 40 sq ft sounds good.
UPDATE- So I applied the spray foam to the underside of the roof and I found both the coverage and the consistency to be pretty disappointing. I ended up with a "B Heavy" mix. I know this because I ran out of the B compound and there is still some A compound left.
I read all the directions. The air and surface temperatures were right in the optimal range. Since I didn't have a good way to measure the temperature of the tanks themselves, I allowed them to sit and acclimate indoors in rooms that I was able to monitor the temperature of.
When I did my first pass (after following all the setup directions) there was a portion that was A Heavy (yellow and runny), but that seemed to even out pretty quickly and I didn't think I was having anymore issues. After that, I guess it was all a little B heavy throughout the procedure since that compound ran out first.
I also did not get the thickness that I had hoped for. I definitely got a full seal against the sheathing, but since the compound was not quite the proper mix.... who knows?
I would have been better off with a layer or two of XPS glued to the underside of the sheathing and foamed around the edges.
What I have now is something more similar to a "flash and batt" application. I plan on filling the rest of the bays with mineral wool, but I won't have the ratio between foam thickness and fluffy insulation that I had been shooting for. I will still do the airtight drywall installation.
I can't afford to buy another spray foam kit. And I can't afford to do a blower door test either. This project's budget is already blown (no pun intended).
Any advice would be helpful. I'm thinking about just buying 8 or 10 cans of Great Stuff canned foam to try and fill the low spots and even it all out to something like 2 1/2 inches. It's as low as 1" in spots. Is Great Stuff closed cell? Is it compatible with this other product (Touch and Seal) that I just spent $350.00 on?
I've attached a couple of photos below. The perimeters of the bays are a pretty good thickness for the most part but there are a lot of places in the middle of the bays that are pretty low.
Also- Thanks to Jon R for jumping into the conversation. I hadn't seen your reply until this morning. This is a great website and all the feedback has been very helpful.
Photo #1
Photo #2
Around here, several libraries loan out thermal cameras. Combined with a fan in the window and some cool weather, this makes air leak detection cheap and easy.
> better off with a layer or two of XPS glued to the underside of the sheathing and foamed around the edges.
I'd say EPS (vs XPS), but since the DIY spray foam didn't go on evenly or meet the coverage specs, you make a good point. I notice that DOW kits rate much higher on Amazon (and cost is close).
Thanks for the reply. All due respect- I'd like to set the idea of the blower test aside for the moment. I'm going to have to finish this job before the cool weather arrives. Additionally, there are no roof penetrations and this small addition is only going to be heated by a wall mounted (sometimes on) electric heater. It's a slab foundation as well. So there really shouldn't be major moisture issues unless there's something I'm not thinking of.
Having said that, I want to get it right and I was very frustrated with the way the spray foam kit performed.
My two major problems are as follows-
1) I didn't get a consistent thickness of spray foam before I ran out. I have 3 inches in some areas but less in others.
2) Also, I'm concerned about the integrity of the foam itself because I ran out of one canister before the other. I had some "A" compound leftover so that means what I installed was a "B" heavy mix.
I'm planning on installing airtight drywall over the Roxul once that goes in. I'm prepared to compress the Roxul a bit to get it to conform to the uneven surface of the spray foam.
But I need advice on how to proceed here. I didn't get any indication from the many articles that I read that the spray foam was going to be so hard to work with.
I was thinking about buying 10 or 12 cans of Great Stuff and trying to fill the low spots knowing that I could trim other spots if they ended up being too high. I'm sure that sounds kind of crazy but I really don't want to buy another Touch n Seal foam kit. Cost is becoming a bit of an issue at this point. At least I can control the cans of spray foam a little easier. Also, it's worth remembering the size of the job- it's only a 5ft by 8ft mudroom addition. There is a door separating it from the rest of the house. It does not share any plumbing or heating with the main house.
My concerns are more with performance/moisture issues and less with code enforcement.
Update 9/2/19- I did a little research and discovered that there is a fan shaped nozzle attachment for spray foam cans that should make the touch ups easier. I ordered a 12 pack. We'll see how it goes. Also, after reading some more reviews of the touch n foam kit, I realized that my experience was not that uncommon in terms of consistency and yield.
Joseph,
sorry about this situation. I've never used the touch and seal but I have used Tiger Foam several times. I can tell you that I have never had an issue but I've always made sure tank temps were high and I shook the crap out of those tanks continuously. List time is used it was last month on our project very similar in size to yours. I too had a number of spots that were not as deep as others but my minimum hit the 2" which is required for my zone. Probably hit a min of 3 inches. I did fill some voids with great stuff. I am not 100% sure but I think it is closed cell phone.
As for the air sealing of the unvented assembly, that's key. Less about glueing to the studs and more about no penetrations and caulking the hell out of the perimeter.
good luck
Thanks for the reply David. Somehow I missed it when you posted it a couple of weeks ago. When you say "caulking the hell out of the perimeter" what are you referring to? The perimeter of the drywall or the exterior?
As for my experiments in spray foam- it's definitely been a hassle. I filled voids in the first layer with cans of Great stuff but of course that just created new peaks. So there are still high and low spots. I've got between 2 and 4 inches of foam everywhere at this point. Most of it is around 3" which is a little less than what I was shooting for.
The specifications are a little confusing but as far as I can tell, in climate zone 5, I should be shooting for R20 in foam, and the rest can be Roxul. If closed cell foam is R-6.5 per inch, 3 inches would give me R-19.5. My total square footage for this addition is less than 50sq. ft. which is way below the limit for the "work around" detailed in Section 402.2.2 ( Section N1102.2.2).
So if I have R19.5 of foam and R23 of Mineral wool that will bring me up to R-42.5 which should be ok for a space this size that will only be heated by a space heater and is separate from the main house's living space and not connected to the basement in any way.
Of course, I'm paranoid about moisture problems so I'm second guessing myself every step of the way. Any further advice would be appreciated.
Joseph,
Yes, the perimeter of the drywall. Basically, anyplace where heat could sneak through a gap. So, where the ceiling and wall meet. With the situation as you described it in your response, I can't imagine ever hitting dew point at your sheathing even if you drywall was not totally airtight.
David,
Thanks for the clarification about the perimeter sealing.
I just measured a few spots of the spray foam layer that are as shallow as 2 inches. It's hard to get anything even with this method. If the kit had worked better for me, and I had only had a few voids to fill with canned foam, that would have been one thing.
But I ended up beefing the foam layer up quite a bit with the canned stuff. I bought these Foam Beak attachments that helped some. But all in all, it's a pretty inconsistent layer.
The dew point factor and potential for condensation is exactly what's stressing me out.