Proposed wall system for climate zone 6a, with focus on energy efficiency.

We are planning on building a small (~ 1350 sq ft) house in climate zone 6a, specific location is Jackson NH 03846. The location is colder, more wind, more snow than other locations in 6a like Maine coast and southern NH. We have a limited budget (who doesn’t?), but are initially sacrificing some things for energy efficiency. We are inspired by Passive House and “Net Zero” building. Some general specs/ideas/goals:
-heat with solar gain (great southern exposure), wood stove, electric backup
-insulated slab on grade, ICF frost walls
-approx 5 kw PV if budget allows
-leaning Intus windows
We have a great builder who we trust and is “on board” with energy efficiency, but this project is pushing the insulation specs of his previous builds. There are obviously lots of other details to consider, but would love some feedback/advice on the proposed wall system, from inside to out:
-drywall
-2×8 with dense pack cellulose
-for sheathing, 10″x7/8″ shiplap white pine (our builder likes this for strength, natural wood)
-Typar
-approx 3″ reclaimed polyiso, some type of foam to glue/insulate seams
-perlins or furring strips
-leaning towards vertical cedar siding, maybe mixing in some horizontal
I don’t have building experience, just interested future homeowner involved in the project, please excuse if my terms are off.
A few notes:
-our builder is open to but not totally sold on the Zip system for sheathing alternative, seems like it’s used on many superinsulated houses these days and has been recommended by others, I do see the benefit of this airtight barrier at the sheathing level
-we’ve talked about two layers of rigid foam for more depth and staggered seams, but seems like one layer is easier to work with and 3″ more available
Would love to hear thoughts from others, with our biggest concern being airtightness. Should we ditch the shiplap pine sheathing for the Zip system for better air tightness? Stick with the shiplap pine, but specify staggered layers of polyiso?
Thanks so much for any help,
Brian
GBA Detail Library
A collection of one thousand construction details organized by climate and house part
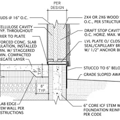
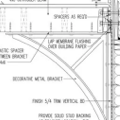
Replies
Brian,
Your proposed wall assembly will work, but it has a few quirks that I wouldn't have chosen.
2x8 wall framing is unusual. Because of the thermal bridging problem through the studs, few designers or builders use 2x8s for walls. I would advise you to stick with 2x6s -- or to skip the exterior rigid foam and go all the way to a double-stud wall.
If your builder wants to use board sheathing, you don't need the shiplap joint. (This layer won't be airtight, and it won't see any weather.) When I use board sheathing, I always install it diagonally, to provide bracing. Here in Vermont, rough boards straight from the mill -- usually spruce and fir, not pine -- of random widths are a lot cheaper than shiplap 1x10 pine.
Of course Zip System sheathing is more airtight than board sheathing. If you stick with board sheathing, you need to create your air barrier elsewhere -- using the Airtight Drywall Approach, or a taped European membrane, or taped housewrap, or two layers of staggered rigid foam with taped joints.
It sounds like you are wavering between vertical cedar siding and horizontal cedar siding. If you are installing the siding over furring strips, horizontal siding makes a lot more sense. And don't try to mix-and-match horizontal and vertical siding, for two reasons: to simplify water management details, and for aesthetic reasons. And whatever you do, don't be tempted to install diagonal siding.
At a 20% framing fraction (24" o.c. framing is usually necessary to get it that low) and R3.7/inch a 2x8 studwall using R1.2/inch fir or hemlock framing comes in at about R20. With R5.5/inch iso (derated for density & temp) that's adding about another R16-17 for ~R36-37 whole-wall performance .
But at the same framing fraction an easier to manage & frame (and fewer board-feet) 2x6 studwall comes in at about R15 whole wall, and adding a layer of virgin stock foil-faced iso on the exterior of your 3" roofing iso would bring you to a similar, slightly higher R value. And by staggering the seams between the two iso layer and sealing the seams & edges of both you can end up with measurably tighter wall. (On a DER I was involved with last year the exterior wall foam retrofitted onto a 2x4 balloon-framed plank sheathed house was 3" reclaimed iso + 1" virgin foil-faced goods- this is a stackup I know!)
On any type of plank sheathing you're going to get better air tightness out of open cell spray polyurethane than dense-packed cellulose, for a similar whole-wall R, and possibly for less cash outlay (if recent quotes in central MA are indicative of what they might be "way up north" in NH.) While I'm a big fan of dense pack (especially in retrofits where gutting the walls would be prohibitively costly, and half-pound foam pours risky), at even-money you'd be more air tight, and if it's less money there may be better places to spend it.
Thanks for the input Martin and Dana.
You have us convinced to scale back to 2x6 wall framing (it will be 24" o.c.). We're now thinking of proposing this to our builder:
-drywall
-2x6 with dense pack cellulose
-Zip system sheathing
-layer of ~ 3" salvaged polyiso, then layer of 1" or 2" new or excellent condition foil faced polyiso, sealed/taped seams
-vertical furring strips
-horizontal cedar siding
Dana, I'm guessing you specify new foil faced polyiso because it will be in good shape and easier to tape?
Would it be good to put some kind of house wrap over the foam or would that be overkill with this setup?
Brian
There are a few advantages of going with a foil faced exterior layer, and ease of air-sealing the seams with FSK tape is one. When it's behind a 3/4" rainscreen gap you get another ~R1-2 of average performance from the foil-facer's low-E/high reflectance characteristics, and there will be fewer dings & holes in it, making air sealing to near-perfection easier than with the reclaimed foam.