Proposed double stud wall assembly– looking for feedback

I’ve decided to DIY the performance upgrades to my house. It is a 120 year old balloon-framed house in Zone 5 (Massachusetts). I’d prefer not to use spray foam or foam panels, if possible. From a DIY perspective, a double stud wall makes the most sense to me. I understand the risk with double stud wall is cold exterior sheathing and condensation if water vapor infiltrates, so I’ve come up with an assembly that I think would minimize this risk.
Existing condition (from outside in):
Cedar shingles
Rosin paper (I think)
3/4″ thick barn board
Studs 24″ o.c. (actual 4″ studs)
Unfaced fiber glass bats
Blueboard and plaster
Proposed assembly:
Siding (TBD)
Rain screen
Building wrap/membrane
3/4″ boards (existing)
5.5″ mineral wool batts, compressed to fit 4″ cavities.
1 inch Gutex multi-therm; fastened to the studs to eliminate thermal bridging and to keep the 5.5″ batts compressed
Smart vapor membrane over rigid insulation, taped
16 o.c. 2×4 non-bearing stud wall/service cavity with another 3.5″ mineral wool batts
Finished drywall
This would give me ~ R 40, at the cost of losing about 5″ of floor space. The combo of multitherm and smart vapor barrier should minimize moisture risk and eliminate thermal bridging. The interior wall allows for a service cavity to maintain the integrity of the air barrier.
One thing that seems unusual is the use of Gutex board on the interior, but I think I might need something stronger than mineral wool panels to hold in the compressed batts. Expensive product, but the money I save by DIY I’m willing to put towards materials, as long as they make it easier to get a quality end result.
Thoughts on this assembly?
If I have rigid insulation panels on the inboard side of the exterior wall with seams taped, is a smart membrane still needed?
Should I just use 3.5″ mineral wool in the 4″ stud cavity and use mineral wool panels as thermal break, or will 3.5″ batts create an air gap that would decrease overall performance?
Any feedback is greatly appreciated.
Thank you.
Steve
GBA Detail Library
A collection of one thousand construction details organized by climate and house part
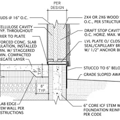
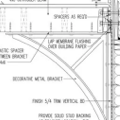
Replies
If I had a dollar for everyone who has asked here about a better way to build double stud walls! Similar questions have been posted weekly for the last ten years, if you're interested in doing some digging. Here are a few to get you started: https://www.greenbuildingadvisor.com/tag/double-stud-walls.
My answer is to not fix something that isn't broken. The beauty of the double stud approach is its simplicity--build two walls, make the sheathing airtight and water-tight, consider an interior membrane (which may be required by code and makes walls more resilient but they aren't always necessary) and fill the bays with moisture-buffering insulation (i.e., cellulose.) Once you start making it more complicated, other wall construction methods start to look attractive because they can perform better and use other types of insulation.
Fair enough Michael Maines-- I know it is has been a frequently discussed topic over the years, but I don't recall seeing an assembly with my choice of materials. From what i can gather after extensive reading, my approach will not create a problem, it's just another way to get at the same solution.
FWIW, I would prefer exterior insulation. I've been trying to get that done for years now, but no one in my area is willing to do that unless I wanted to use foam, and even then it is just a few boutique builders and the premium that comes with them.
A double stud wall is more DIY-able for me, as I can go room by room and won't need to be outside on scaffolding. I'm just one guy doing this part time after my day job. I know dense packed cellulose is the most common way to insulate a double stud wall, but again, DIYing this over a period of time and do not have the equipment.
I appreciate your reply, but questions remain that I am hoping to get some feedback on:
Is Gutex OK on interior and if so, would a smart membrane be redundant?
Has anyone compressed 5.5 inch mineral wool batts into a 4 inch deep stud bay? I'm guessing it won't be hard to do that, but assumed the rigid insulation board would be a good way to hold it back in addition to functioning as the thermal break.
steveoneil,
I'm not sure the Glutex buys you. Any gap between the two walls is a thermal break. Let me suggest yet another variant to drive Michael to drink on this Friday afternoon:
Rather than compress the batts, why not let them extend out and bridge the 1 1/2" gap between the two stud walls? This will leave you with strips at each stud and the wall plates which are not insulated. You can use foam board, Glutex, or any other insulation to fill them.
Steve, I didn't mean to sound flip (or at least not TOO flip...); it really is amusing to me how much time people spend on this topic. I have spent many hours trying to find a better approach as well.
Have you worked with mineral wool batts before? The ones I have used would not compress from 5.5-6" to 4", at least not without a lot of effort. Gutex is a great product but I don't think it's rigid enough to compress mineral wool by 25+% and it has lower R per inch than mineral wool. You could compress typical fiberglass batts that much. If you're doing your own framing and insulating you could do the separate layers out of sequence as you propose. Having an insulated service cavity on the interior of the vapor control membrane is good for a few reasons. I like Malcolm's suggestion to let the mineral wool batts project into the space, then fill the gaps with other insulation.
Gutex is vapor-open, as is mineral wool, so neither make a variable permeance membrane redundant. When using high-R assemblies in cold climates, using a membrane helps keep the sheathing dry. The more insulation you add, the less heat energy there is to push moisture through the wall and the more vulnerable it is to moisture-related problems, so the more important it is to limit how much moisture can get into the assembly. I might consider eliminating the membrane with cellulose insulation since it protects everything it touches, but I definitely would not skip it when using a moisture-phobic material like mineral wool because any moisture in the assembly will soak into the framing and sheathing and if it stays there long enough it will result in microbial action.
I'm not aware of any parts of Massachusetts that are in climate zone 6; I believe it's all climate zone 5.
Michael,
I think your comment brought up a pretty salient point. The endless proliferation of variants, where each project invents it's own bespoke building assemblies, is great for high-end one-off projects. But I think it's also what stops high performance building from moving into the mainstream where most projects occur.
Until this shakes out, and one or two appropriate assemblies for each climate zone become the norm, and everyone is familiar with them and how they interact with the work of the rest of the trades, high-performace building is going to remain a boutique niche.
I think for DIY, your best bet is this:
https://www.finehomebuilding.com/membership/pdf/9750/021250059.pdf
You can make the foam any thickness you want to fit even bigger batts. 1x3s tend to split, 3/4" plywood strips would work better.
R40 walls makes sense in a new build where the walls are insulated with very inexpensive insulation, even there the ROI is extremely long. Once you start adding complicating the assembly, your ROI is pretty much never.
In zone 6 an R25 assembly (ie 2x6+R5 rigid, or in case of the Bonfig wall, 4" stud plus 2.5" foam with R28 batts) gets you most of your energy savings. You can also substitute wood fiberboard for the foam strip behind the strapping.
I agree with Michael that you're likely to have problems trying to compress mineral wool batts that much. A major advantage to mineral wool is that it has "form", and it's more solid-like compared to fiberglass, which makes it easier to install well since it has less tendency to bunch up and leave voids. The downside is that if you DO want to compress the batt, mineral wool us much less compressible.
I don't see that the gutex gains you anything here. You don't have to worry about thermal bridging in a double stud wall like you're building, since you can just stagger the studs (or air gap them) to achieve the same thing without any special material being used for a thermal break. If you stagger the studs significantly, that does complicate insulating the outer cavities, assuming you're working from the interior side of the wall. You could use the staggered studs to help hold the outer wall batts in place though. You could potentially offset the interior side studs a few inches, but not "all the way" to the usual centered-with-respect-to-the-other-side position normally used with a double stud wall.
I would use an interior side smart vapor retarder to help minimize the chances of moisture issues inside the wall. MemBrain is good for this, since it's the cheapest of the commonly available smart vapor retarders, and it works fine in applications that don't benefit from the higher performance membranes.
Bill
@Michael-- yes, Zone 5. Was thinking of planting zones when I wrote 6 😉
Thanks everyone for the feedback with this FAQ. I guess it comes up often because there are a lot of double stud wall options and none are particularly wrong, as long as one pays attention to the basic principles.
I'm not trying to re-invent the wheel, just trying to adapt it to my particular circumstances. New construction can follow a more defined approach, retrofits like mine have to work with what is there, to an extent.
My existing framing is 24 in o.c., but in most cases not really 24" o.c. and not particularly straight and plumb, so the installation of an interior non-load bearing wall to true things up for later finishes is a positive. Instead I suppose I could sister each stud to true things up at the cost of a slightly lower R value overall, which is acceptable too.
I came across a discussion a while back about Joe L's moisture concern with double stud walls, which if I understood correctly, could be eliminated with the use of internal sheathing like plywood on the inner stud wall. This is why I thought that instead of taped plywood, I could use a product like Gutex as the sheathing, and have the benefit of an added thermal break. Yes, the whole point of double stud wall is to provide that thermal break, but I was thinking to save floor space I would butt the new wall right up against the old one (in contact with the Gutex or other thermal break along the existing studs). Having not handled the gutex product myself, i was wondering if it would be stiff enough to hold back the mineral wool. Sounds like it might not be unless provided with additional support (which adds complexity again).
Compressing 5.5" mineral wool, if an option, seems better than using the 3.5" product and having to fix the air space some other way-- balloon framing, so lots of potential for air flow unless things are packed really tight. I think cellulose would solve a lot of problems, but staging installation as I go could get complicated vs. just stuffing batts in there when I'm ready.
In general, I think some version of the double stud wall would be easiest and most effective for me. I'll continue to think about materials and construction details some more. One thing I did not mention is that while I expect to have new siding with rain gap eventually, it will not be installed before I do the interior work, so in my case it seems to be important to get the interior layer correct in terms of vapor transport. So seems like a smart membrane is a must.
Steve, Gutex (and similar wood-fiber insulation boards) are vapor-open and air-permeable; the only thing they slow down is heat flow. I'm not sure what article by Lstiburek you're referring to but the location of each item within the wall makes a big difference. He might have been suggesting plywood or OSB on the interior side as a vapor retarder and/or air barrier; it can work for both of those things but wood fiber insulation cannot.
A lot of--perhaps most--existing wall assemblies depend on the energy from heat flowing through the walls to dry them out. If you don't have a rain screen already and/or if you don't know for certain that rain is not getting through your siding, I would not overly insulate the interior. People often blame rot and peeling paint on insulation or the house being "too tight," when it's usually just not detailed well enough on the exterior.
Thanks Michael. Yes, I could have dug deeper on Gutex and learned is not the same as OSB or plywood in terms of permeability. I suppose the use of smart membrane on top of it would fix that, but as others have pointed out-- things start to get unnecessarily complicated as I add layers...
I've seen a lot of this house's outer sheathing from the inside-- no sign of rot or mold at all, which I attribute to how leaky and fast-drying the entire building envelope is. As I tighten it up, definitely don't want to create new problems whether it be through choice of materials or sequence with which they are installed.
With random stud spacing, I would look at a dense packed Mooney wall as an option:
https://builditsolar.com/Projects/Conservation/MooneyWall/MooneyWall.htm
You can shim the cross strapping to get it level and install it at 16 OC. You can also build it with 2x3 on edge for a bit more R value.
Akos,
Are 2"x3"s on edge a workable wall? You can't install them with most nail guns, or hang cabinets without blocking down to the floor.
I haven't tried it on a wall but done it on a roof and it is very solid. Used long screws though so a much more labour than a nailer. A bit of blocking won't hurt in the kitchen area but even drywall by itself does a very good job.