Proper use of various rigid polyiso facers?

I’ve come across a few different facers on rigid polyiso:
– foil
– trilaminate (foil-kraft-foil)
– glass fiber
– reflective vs non-reflective
Based on the manufacturers guidelines, I’ve seen recommendations based on wall construction and siding materials, but I don’t understand the reasoning behind these guidelines.
How important is it to match the facer to your building context?. What’s the difference, performance-wise? In what situations would you use one over another?
Any help will be greatly appreciated.
Cheers,
Andrew
GBA Detail Library
A collection of one thousand construction details organized by climate and house part
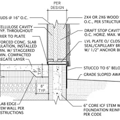
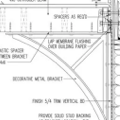
Replies
The vapor permeance of the facers and where they are placed in the assembly can be critical in the moisture handling peformance of the building. Facers with foils block pretty much all moisture transfer, so you must be careful to use them in the proper placement to not create humidity traps. The climate, insulation R values, and vapor permeance of the other elements in the assembly stackup all play important roles on how it needs to work.
This is a very wide subject, with entire books written on it- hard to answer in a paragraph or two.
Thanks for the reply Dana. OK, what if we narrow it down to the situation I am facing? What would be the recommendation?
Here's the hypothetical wall from the inside out:
- 1/2" drywall
- 2x4 wall framing, cavities filled with OC spray foam or dense cellulose
- 1/2" osb
- 2 layers of 2" polyiso or 4-1/2" polyiso nailbase
- wrb (could be inside polyiso instead no?)
- rainscreen
- wood, engineered wood or cement siding
Climate zone is 3, Dallas, TX.
Cheers,
Andrew
Andrew,
In the application you are contemplating, the type of facer you choose is irrelevant. Choose polyiso with any kind of facer.
Is that because my proposed wall could dry to the inside? Or is there more to it?
Andrew,
In residential construction, I can't think of any application where the permeance of the polyiso facer would make much of a difference. That's because it's important for the polyiso to be thick enough to keep the wall sheathing or roof sheathing above the dew point in winter. Once you have specified polyiso of such a thickness, you can't really depend on on drying through the polyiso; it's generally too thick for that to happen.
Polyiso-sheathed walls are designed to dry in two directions: they dry outward from the outermost face of the polyiso, and they dry inward from the innermost face of the polyiso. Even if the polyiso facings are made of aluminum foil, and are therefore vapor-impermeable, these walls perform well.
I appreciate the explanation. Thank you.
That makes sense. But what happens if the foam gets wet behind/between the facers? How does it dry? Polyiso is absorbent, so will it just slowly dry via the exposed edges? To prevent water from getting into the foam from above (a roof failure) seems easy enough to tape/seal the top edges of the foam. Does anyone do this?
Cheers,
Andrew,
It's always possible to come up with a scenario that leads to wall rot, I suppose. My own reaction to your scenario is that it is unlikely. If you pay attention to best practices for flashing, and you install a ventilated rainscreen gap between your siding and your polyiso, your wall should stay dry.
If you want to tape the edges of your polyiso boards (especially those facing up), I suppose that there is no harm in doing so.
Martin- glass faced poly iso is typically a higher-perm class-II vapor retarder, and in a single-layered application could still offer more seasonal drying capacity than a kraft facer on a batt. In dual-layers it's similar to a kraft facer, which is still not nothing. The iso itself is something like 30-50 perms @ 1" without the facers, which is why the vast majority of sheet goods out there comes with vapor-retardent facers.
But I agree that in Andrew's stackup the facer is the least of it.
Nailbase iso is also usually semi permeablle with fiber facers, but I'm reluctant to put the OSB nailbase under any random masonry or stucco cladding in a Dallas TX climate without something to protect the nailbase from the high moisture drives from the masonry. While a simple 3/8" rainscreen gap would be adquate for wood siding, an inch would be the minimum safe ventilation gap behind stucco or brick, and using a ~1 perm vapor retarder such as fan-fold underlayment/drain-plane might be preferable to roofing felt on the OSB.
That's a fairly high wall-R for that climate zone too, hitting the low to mid 30s, which might not have even a 100year economic rationale in that location. See table 2, p 10 of this document:
http://www.buildingscience.com/documents/reports/rr-1005-building-america-high-r-value-high-performance-residential-buildings-all-climate-zones
If you have access to reclaimed roofing iso from commercial demolition it might "pay back" though, since it's usually at ~1/4 -1/3 the cost of virgin stock.