Preventing Racking and Improving Envelope

Hi all – I’m Neil and I’m a long time listener, first time caller… I am as of recently the owner of split-level house ‘installed’ in Gibsons, BC (Climate Zone 4) in 1955 (brought over on a barge, but constructed at some unknown date in the lower mainland – the pinstripe detailing of the hardwood flooring hints to me at 1940s or earlier).
The walls are constructed of (in to out)
-16” horizontal drywall strip with plaster scratch and smooth coat
-fibreglass batt insulation
-2×4 stud wall
-horizontal (not diagonal) 1×6 sheathing
-Stucco
In the lowest level of the house, there is just normal drywall, and poly vapour barrier (just stapled on) on the inside of the insulation.
There are 2 chimneys, one of which is connected to a ‘high efficiency’ (i.e. sealed) methane/butane fireplace. The other is an artefact. Windows are okay – about 15 year old 2x pane.
I have been working on sealing gaps and and have added poly in the places I’ve replaced the drywall (for bathroom renovations – fortunately no asbestos to be found). There used to be rats in the house, but in closing holes we seem to have excluded them, though they had nests and tunnels in places where insulation was exposed (basement, attic), but no evidence seen where it was covered by wood or drywall.
The stucco is in pretty bad shape. Likely from ’55. Lots of fissures throughout. Also I hate stucco. But it is not visibly delaminating from the structure that I can see at least.
The house has shifted a lot since summer, with some interior doors becoming uncloseable. No doubt some of this is due to humidity increase (it rains most days from mid-sept to March), but I think that this is combining with racking due to the weakened stucco and poor racking resistance of horizontal board sheathing.
In the summer I would like to put a new envelope on, and getting rid of the functionless chimney. I am thinking a peel and stick vapour permeable membrane, and 80 mm dense mineral wool over top, and a rainscreen with a aluminum sheet and siding mix as cladding.
My questions are these:
1. Does the above seem like a good idea, or will I run into condensation issues due to the lack of interior poly? I can’t really rip up all the interior walls, as we are living in it.
2. If I do the plan above, should I do something to beef up the racking resistance a bit over the existing board sheathing (e.g. 1/4 or 3/8 plywood over the whole, or maybe just corner reinforcements)?
Thanks for your input!
Neil
GBA Detail Library
A collection of one thousand construction details organized by climate and house part
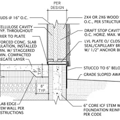
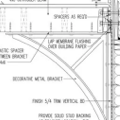
Replies
I got to ask if you really want a high performance house I am sure with enough time and money you could get there more or less.
I think you should sharpen your pencil and make a realistic budget my guess is if you put any value on your time you would have less money in a new build and end up with a better home, if you must strip both the interior and exterior to the studs.
I am afraid when you open the wall you will find more than unpleasant surprised.
Walta
Neil,
I think that sounds like a good plan, and the lack of an interior vapour-barrier shouldn't cause any moisture problems. While the walls are open I'd suggest re-nailing the existing sheathing. That will stiffen it up quite a bit.
Short of removing all the boards and replacing them with plywood or OSB, and dealing with the connections between the walls and the foundation below, you aren't going to get a sufficient increase in shear resistance to be much use in a seismic event, but new fasteners and perhaps a single sheet of plywood at the corners will probably make a big difference to the movement you have noticed in the structure.
I understand where Walta is coming from, but given that new construction is somewhere around $300 a sq ft, I'd stick with renovating.
Construction of that vintage typically used bright, smooth shank nails to attach the sheathing. Over time they get a layer of rust which acts as a lubricant and they loosen easily. You can stiffen things a lot by taking a nail gun and a few thousand ring shank nails and tacking everything together.
If things are out of square you may want to try and get them square first. Or you may not. A lot depends on how much of a can of worms you want to open.
Thanks for the heads up, Malcolm. Seems our paths have crossed a few times here. I suspect they will continue to! :)
Neil,
Good luck with your project. It's always hard to know where to draw the line with renovations like that.