Preventing insulation spill-over into soffit?

Q1) When installing eave chutes (aka ventilation baffles) is it still standard practice to tuck unfaced fiberglass between the rafters (in the rafter bays without chutes) at the perimeter to prevent insulation from spilling over into the soffit? Is there a better alternative?
Q2) I’m planning on adding cellulose to the attic – what’s the best material for keeping the cellulose away from the brick chimney? The chimney doesn’t get very warm – it’s only used as a raceway for the B-vent on the gas water heater. However, I imagine code officials still want an approved material next to the chimney in case some future owner vents a furnace through it in the future. (The current 90%+ furnace vents via plastic.)
Thanks.
Jon
GBA Detail Library
A collection of one thousand construction details organized by climate and house part
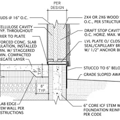
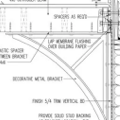
Replies
Why aren't all the rafter bays getting ventilation baffles? And I hope you're not talking about those worthless, flimsy PropaVents. There are a lot of much better baffles on the market, made of coated cardboard or semi-rigid plastic, some of which are made to staple down to the wall top plate as well as the rafter sides to close off the soffits and provide full-width venting to each rafter bay.
If you need to seal the wall plate area better, then use spray foam.
You can make a chimney shield out of any stiff material, spaced 1" from the brick. But make sure there is a good fire block and air seal where the chimney passes through the ceiling or otherwise blow the cellulose tight to the chimney.
Jonathon,
You need to install a wind-washing dam between each pair of rafters. As Robert pointed out, you can do this yourself with lumber, cardboard, or rigid foam -- remember to seal three sides of the perimeter with caulk or canned foam -- or you can use a commercial product like the AccuVent from Brentwood Industries ( http://www.brentwoodindustries.com/spg/building-products/index.aspx ). The Accuvent is made from vinyl.
Robert:
I hadn't planned on baffles in every bay because the person who did my Home Performance w/ Energy Star inspection only called for doing every third one, the theory being you only need to provide enough net free area to connect the soffit vents w/ the roof vents. What are the benefits of a baffle in every bay? I couldn't get the coated cardboard baffles easily, so went w/ the plastic ones from ADO, except where the bays are less than 14" wide, due to boards sistered onto the rafter tails. (I haven't figured out why the 1938 builders did so.) For those bays, the only baffles narrow enough were foam, but they at least have "egg crate" dimples to prevent collapse.
Martin,
I plan on contracting for spray foam 2' out around the perimeter, so wind washing shouldn't be an issue.
Jonathan,
I'm confused. You wrote, "I plan on contracting for spray foam 2' out around the perimeter, so wind washing shouldn't be an issue." That seems to contradict the concern expressed in your original question -- your concern about the best way "to prevent insulation from spilling over into the soffit."
If you are blowing cellulose on your attic floor, and you are concerned about insulation spilling over into the soffit, it seems to me that you have a gap under your ventilation chutes. So where are you installing spray foam?
Sorry, Martin, I should have made it clearer. I was mainly concerned about overspray from the foam getting into the soffits. Now that I think about it, however, the foam contractor wants to only do 5" of foam, and the joists are 2x6s. , which would leave some room for add'l cellulose. The foam contractor cites the diminishing return curve as the reason for only doing 5" of foam, but maybe I should tell him I want the max. depth possible at the perimeter?
Here's a picture of my 2" wide perforated soffit. I doubt it's capable of letting enough wind in to do much washing? In some places it doesn't even let light in, but taking it apart would dent the aluminum badly.
http://picasaweb.google.com/iceonwingra/BathFanSoffit?authkey=Gv1sRgCO6L2-yD3M5I#
I'm still not clear on the benefits of a baffle in every bay. Thanks for all the help.
Jon
Jonathan,
Roof venting has many functions, including evacuating stray moisture, evacuating summer radiant heat gain, preventing ice dams by keeping the roof cold in winter. And there has been much dispute about the relative impact on each of those functions (with many builders going to "hot" unvented roofs). But the most overlooked and perhaps most important function is to quickly dry roof sheathing and framing should there be a leak in the roofing, from roofing failure or poor installation or wind-driven rain. This becomes an "insurance policy" against premature roof assembly deterioration.
Each of those functions, however, benefit from fully "washing" each rafter bay with moving air from soffit to ridge. For this reason, the only effective roof venting system includes continuous soffit vents with a minimum net vent area of 9 square inches per linear foot and continuous ridge vents with a minimum net vent area of 18 square inches per linear foot and exterior wind baffles to lift wind over the vent, creating negative pressure to assist exhaust flow (rather than positive pressure to reverse it).
The best insulation/vent baffles are not any of the products on the market, but ones you make yourself from any rigid material (plywood, hardboard, MDF, foam board) that is cut to fit between each rafter pair and attached to 2x2 nailing strips that keep it below the roof deck 1½".
I'm so tired of hearing this "diminishing returns" nonsense. Conductive heat loss is directly proportional to R-value, which is directly proportional to the thickness of any insulating material.
The only "diminishing returns" are the loss of income for the foam installers who lose jobs if they price them for the code-required R-value because of the high cost of spray foam.
"diminishing returns" and "equivalent R-value"
Care to add "water blown and zero-VOC"
That kool-aid must be tasty. I'm sick of it too.
But its the "trade secret" all over the MSDS sheet that really ticks me off. Take a look at "bio-based" foams B-side MSDS, it looks like it might possibly be 20% bio-polyols or 2.5 ounces per cubic foot but what exactly are they using for a flame retardant? Is there even one foam producer selling in America who is willing to disclose their flame retardant?
Is any company willing to commit to using a bio-degradable non-bioaccumulative non-toxic flame retardant in the American market? It would be a much more compelling reason for me to switch to that foam than the potential of saving 2.5 oz of oil per cubic foot.
Just sayin' no biggy I'm not planning on having any more children anyway so why should I care? Sort of a sore spot for me I guess.