Pretty Good Wall Design – Maybe

Hello,
The attached file shows a wall design concept for a new house build near Minneapolis, Mn. I’m trying to design a wall that is both easy to build and has good performance.
I really wanted to bury the air and vapor control layers at the sheathing layer so the stud cavity only uses 2.5 inch thick rockwool batt (I’m firm on the rockwool insulation direction). Approximately 3/4 of the insulation is on the outside / cold side of the vapor barrier to prevent condensation on the sheathing. This also leaves 3 inches open for a utility chase. One big installation advantage is that fitting the insulation around wires and boxes is minimized since the batt is usually behind everything – no cutting needed.
The sheathing and control layers could be lots of designs. One is the Huber Zip wall system. Second is taped plywood plus house wrap or roofing felt. The third is peel and stick covering over plywood. Fourth is a liquid applied over plywood. I’m leaning towards number 2 for cost reasons.
There is one layer of 3.5 inch rockwool batt. Since there are no studs here the thermal break is good and moisture can move sideways if needed.
The next layer is 2×4 studs, 3.5 inch rockwool batt, plus a high perm weather resistant barrier (ie #15 roofing felt shiplapped or house wrap). This keeps wind and rain off the insulation but allows some air and moisture passage.
Over this goes the 1×4 nailers. These create the rain screen vent behind the cladding, hold the insulation and WRB on tight, and act as a wide nailing surface for the siding.
The 2×4 studs are attached to the 2×6 wall at the top plate and sole plate – I haven’t worked that out yet. They are cantilevered off the wall and hold the siding (so only the 2×6 wall sits on the subfloor). The two outer layers of insulation (outside of the sheathing) are entirely on the outside of the walls and floors to get a good, continuous layer of insulation and air/vapor barrier.
I intend to have windows and doors attached to the 2×6 wall and sheathing just like a normal wall.
OK, so what do you think? I’m cautiously happy with this approach and how it balances performance, construction, longevity, and cost. All feedback is welcome.
Karl
GBA Detail Library
A collection of one thousand construction details organized by climate and house part
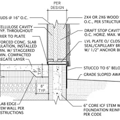
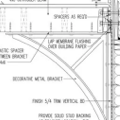
Replies
Just to clarify: Are you intending to cantilever the whole outside wall, or does it just extend down past the floor system and sit on the foundation too?
Build it.
You mention both 2.5 and 3.5 rockwool. Where are you going to get 2.5" rockwool? If you custom order it from Thermafiber, you'll pay a lot (and people have told me their product is not fun compared to Roxul). If you are talking about using the Safe N Sound, my understanding from comments made by others on GBA is that these non-thermal rated batts probably insulate at around R-3.3 instead of R-4.2 for the comfortbatts. Also, last time I ordered both, the SnS cost me more than the comfortbatt. Or was the 2.5" note a mistake?
Malcolm Taylor - I could do either one. Do you have any thoughts on those options? It is a single story house with a crawlspace and a standard foundation at 48 inches depth. I plan on insulating the outside of the crawlspace foundation anyway. Otherwise I was thinking of attaching the siding studs to the rafters with metal nailing plates (takes the vertical and horizontal loads) and attaching at the foundation wall with a pressure treated 2x4 on edge. That would be the bottom of the siding and below that would be XPS insulation on the outside of the foundation wall. If that's confusing I'll make a drawing.
AJ Builder - Thanks, I'll take that as a thumbs up! Much appreciated.
Keith H - Good question. I plan to use the Roxul Comfort Batts. According to the Roxul website the Comfort Batt insulation is available in 2.5 inch thickness for steel stud walls. I'm sure it is a special order but I'm OK with that. I would have to trim down the sides by 1.5 inches to fit in the wood stud wall.
The reason for using 2.5 inch is to maintain 1/4 of the insulation value on the inside of the air/vapor control layer to prevent condensation on the sheathing during very cold conditions. I'd rather use the 3.5 inch thickness but then I'm at 1/3 inside and 2/3 outside and I'm not sure that would be OK.
I could also split some 5.5 inch thick batts down to 2.75 inches (I've worked with foam sheets before so it's no big deal). That may end up being what I do if the 2.5 inch is hard to obtain.
Thanks all,
Karl
Karl,
I'd work hard to try and get both walls to bear on the foundation and avoid any gymnastics hanging all that outside it. - although not if it meant that the foundation wall width had to be increased (there's a puzzle for you!)
I'm also wondering whether the small advantage gained using the 2"x6" inner framing is really worth the extra 2" of wall width and heavier framing just to minimize cutting insulation around the few electrical boxes and what little plumbing generally needs to be run in exterior walls. Especially as both the services remain safely inside the protected plywood air barrier. I'd be inclined to use 2"x4s and get my utility knife out.
As far as going with no sheathing on the exterior, Lucas Durant has done it on the house he has frequently posted here, and perhaps it is just the result of seeing the onerous flashing requirements necessary to keep walls dry here in the PNW, but I think it might take more forethought to get things right than most builders have.
Karl,
You want a wall that is "easy to build," and this one is unconventional. Do you want it to be "easy to build" for you -- the owner/builder -- or for a hired framing crew? If you are hiring a framing crew, "easy to build" usually means something more conventional.
The most unconventional aspects of this wall are (a) the sheathing layer in the middle of your double-stud wall, and (b) the lack of exterior sheathing. This wall can be built, but some of the workers on your site are going to be scratching their heads.
You have to think carefully about siding fastening requirements and the attachment of exterior trim (corner boards, window casing, door casing, etc.) if you don't have any sheathing to nail these elements to.
It can also be challenging to flash penetrations (hose bibs, exterior electrical receptacles, light fixtures) if you don't have any sheathing to attach your flashing to.
As usually happens to me, I found the answers that I needed after asking the question - but not in the way that I thought (there is something buddhist or zen in there). One of the sites listed on the blogroll called nbsuperinsulatedhouse.blogspot.com has the details that I want in amazingly well done drawings. I'm going with the Larsen Truss approach shown in the construction details section. I just happened to click on that link an there it all is.
I also really like a lot of what is written in that blog. So there it is. Thanks for the input everyone - I'm off to do floor plan , etc. Gonna revive the Larsen Truss because maybe that Canadian carpenter did it right back in the days of disco.
Karl
Karl,
For more information on Larsen trusses, see All About Larsen Trusses.
Can someone comment on the effect of convective loops in a wall half filled with insulation? In general insulation performs better when encapsulated in all six sides. I would imagine a lot depends on the density of the material, so using a spectrum going from fiberglass batts to rigid foam, how much of a problem would this be with mineral wool? Even if there was no air movement within the insulation, is there a significant reduction in its performance having the surface washed by the convective movement of air between it and the drywall? Finally, given the inner wall has so much insulation outside it, would there even be any convective loops, or would the cavity really act like part of the interior?
Martin - Many thanks for your help. You and everyone here have been great. GBA is a fantastic resource.
I have been looking through some of the Canadian research into wall condensation and it shows that the barrier layer can be much closer to the cold side than the 1/4 - 3/4. One recent paper is "Heat, air and moisture control strategies for managing condensation in walls" (archive.nrc-cnrc.gc.ca/obj/irc/doc/pubs/nrcc46734/nrcc46734.pdf) and if I'm reading table 2 correctly the control layer can be a lot closer to the cold side.
Malcolm - I will make a guess that since the temperature difference of all the surfaces in the cavity is very small then the convective looping is also very small and the wind wash effect is a negligable loss.
One other thing is that the open area might help drying the insulation. The moisture has a big open area to vent into instead of sitting in the insulation and captured between the drywall, sheathing and studs.
Also, the rockwool insulation is hydophobic. That might help keep vapor out of the insulation.
Part of the house will be 2 stories and to use 24" OC framing the 2x6 studs are required. That's part of the reason for the large open cavity - but I would like to use 3.5" insulation in the cavity if possible.
I would be very skeptical of the longevity of the house wrap or felt attached to studs 24" oc and unsupported by any form of sheathing. I plan a very similar wall design, with both walls 2x4 24" OC, but I'll use fiberboard under the house wrap. I also agree with the suggestion that the outer wall sit on the "foundation", obviously this requires that the "foundation" be of adequate width. (which is why I plan on a "double" walled wood basement) You'll need to "box" around windows and doors and carefully plan the "flashing" around them even though the actual attachment is to the inner wall. To minimize condensation risk it is best to keep the inner and outer walls studs inline
Karl,
Here is a link to Lucas Durand's blog which you may find useful:
http://ourhouseuponmoosehill.blogspot.ca/p/details.html
I second the motion, Lucas Durand has a great blog and great build.
Jerry - Agreed about the outer sheathing - I've added that now and thank you for pointing that out. I'm curious about lining up the studs and why that would minimize condensation - could you clarify that for me?
I went with the 2x6 because Wisconsin code only allows 2x4 at 24" OC for a one story and part of the house will be 2 levels. I thought that incorporating the open utility chase would be a good thing - any thoughts on that?
After further research it appears that I could go with 3.5" insulation in the cavity and 7.0" minimum on the outside ( 1/3 interior - 2/3 exterior). I will have to get an OK by the inspector (which code allows) since the vapor barrier is buried. If the inspector says no then I will have to find another way.
My current plan is for 100% plywood sheathing with taped / caulked seams and good quality house wrap. That should take care of the structural, air control, vapor retarding, and water resistance requirements. Any thoughts? Am I missing anything or a better way? I thought about 6 mil poly but current direction seems be be vapor open especially with a buried vapor retarder layer.
Malcolm and AJ - Thanks and I am looking at that blog now. I am continually amazed by the great work so many people are doing - very inspiring. His envelope design is very much what I was trying to do.
Karl,
I'll try to explain why aligned studs have lower risk of condensation on the sheathing. Consider the outer wall and inter wall insulation, the studs will be colder than the insulated spaces between them. With the cold strips of sheathing created by the outer wall studs faced by the warmest strips of the inner wall created by the inner wall's stud there is least risk of condensation but maximum heat transfer (a very small penalty, well worth the reduced risk of condensation).
FWIW, My plan is to sheath the inner wall with plywood applied over beads of acoustic sealant to the wall framing before the wall is "erected". Also a bead of acoustic sealant will be placed on the sub floor before the wall is erected. Wall corners will be caulked with acoustic sealant as well. With this method I see no reason for tapes or house wrap on the inner wall, the plywood itself is the intelligent vapor retarder and air barrier.
Jerry - Thank you, I understand your explaination.
The house wrap over the structural sheathing is in the code here and I would rather just put it on than fight. It seems like cheap insurance against water damage and provides a good drainage plane around window and door openings. The crews are accustomed to installing something over the sheathing.
I think I've found the wall design that I've been looking for in Alaska. The Arctic Wall design by Thorsten Chlupp (I know he has been posting here) is exactly what I'm looking for. I plan to replace the blown in cellulose with rockwool batts and thin down the insulation amounts for my climate. I like the vapor open design.
Karl,
I guess that I'm operating on a different set of assumptions. My primary WRB is outside of all the insulation and framing and under the rain screen gap that is under my exterior finish material. This means all my flashing connects to this WRB. While the sheathing on the outer face of the inner stud wall is structural and my primary air barrier but not the WRB. I don't want wet framing due to rain etc. I can see that your approach will make flashing easier but can result in wet framing in the outer wall. I would have a serious discussion with the code officials as the code is not about the kind of wall you are building. however if they insisted another layer of house wrap wont do any harm but I'd still implement the primary WRB on the outside of the outer wall.
Karl,
Why are you so set on using rockwool? It might be a semantics issue, but I usually associate that stuff with old insulation that is akin to asbestos. I won't even use fiberglass anymore, and dread having to even be around it in existing attics and wall remodels. All of that spun inorganic material is very bad for lungs, eyes and skin, and has a high embodied energy to manufacture, and is usually not very reusable. Why not use cellulose or blown in foam?
Curt:
https://www.greenbuildingadvisor.com/blogs/dept/guest-blogs/mineral-wool-insulation-isn-t-fiberglass
Jerry - Yes, I may not have been clear but there will be a WRB over the insulation (inside surface of the vented rain screen). I was thinking of having a second vapor open WRB over the structural sheathing but I'm not sure if that's needed - I suppose the outer WRB should take care of that.
Curt - I like the combo of fire and water resistance plus vapor openness and DIY friendly installation. Placed properly it should last 100 years or more and perform just as well as the day it was installed. It can also be easily removed and reused - remodeling friendly. I haven't seen any other insulation with that combination at a decent price and easy availability.
Rockwool may not be the best in any one category but it scores high across the board and it has a century long track record for proof. Most of the other insulations have at least one big downside that need to be accepted (or ignored by the advertising department). Rockwool seems like that old, reliable material that just can't get the respect it deserves in the noisy world of selling the latest, greatest, whizz bang insulation material.