Pretty Good House in Iowa

I am planning on building a “pretty good house” in the MidWest (Des Moines). After throwing around ideas on different wall structures (double stud, 2×6 with wet blown cellulose and rigid foam exterior), I’m curious what the prevailing thoughts are on building a 2×4 wall (16″ o.c.) with 1/2″ exterior plywood sheathing. 2″ rigid EPS would go exterior, with WRB being Tyvek, then furring strips and hardi-plank siding.
My questions truly relates to interior cavity insulation. I desire to fill the cavity with closed-cell spray foam for high R-vale and air sealing qualities. Many articles on this site state to refrain from having a vapor barrier (the closed cell, in this case) in the wall cavity. However, I note that most building examples include foil-faced polyiso instead of EPS. I ran across a comment stating spray foam would be acceptable in the cavity if rigid foam was not foil-faced or greater than 3″.
In this case would closed cell foam be acceptable as moisture would still be allowed to permeate the semi-permeable EPS with exterior vapor barrier?
Thank your for your responses.
GBA Detail Library
A collection of one thousand construction details organized by climate and house part
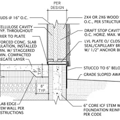
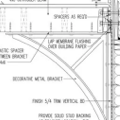
Replies
Thomas,
First of all, I commend you for your plan to install a layer of rigid foam insulation on the exterior side of your wall sheathing. That's an excellent way to reduce thermal bridging through the studs.
If you are building in Iowa, you are either in Climate Zone 5 or Climate Zone 6. (See map below.)
Here is a link to an article that explains the rules governing exterior rigid foam insulation: Calculating the Minimum Thickness of Rigid Foam Sheathing. If you go ahead with your plan to use 2x4 framing, the minimum R-value for the exterior rigid foam will be R-5 in Zone 5 or R-7.5 in Zone 6.
If you go this route, your wall needs to dry to the interior. That means that any insulation you install between your studs should be vapor-permeable. Options include fiberglass batts, blown-in fiberglass, cellulose, or open-cell spray foam.
I'm not a fan of wall assemblies that break these simple rules. It's true that if you install closed-cell spray foam between the studs -- a type of insulation that stops inward drying -- you can reduce the risk by choosing a rigid foam that is (a little bit) permeable like unfaced EPS. But (as Dana Dorsett will probably explain in a soon-to-be-posted comment) using closed-cell spray foam between the studs is wasteful. The thermal bridging through the studs reduces the whole-wall performance to the point where the added investment in closed-cell spray foam is hardly worth it. Moreover, this type of spray foam has a high global warming potential, so it harms the environment.
Martin-
Thank you for the feedback. We aren't set in stone what walls we are building yet, but there are a few interesting factors at play. The largest one is that Des Moines is an absolutely crazy period of growth, and all of the builders seem to be focused on churning out inefficient homes.
I've gotten a few to sit down to the table and talk exterior foam, but it has taken a lot of talking to get a builder to agree to 2" or more. We initially wanted 2x6 walls with exterior foam, but nearly every builder has had difficulty envisioning how a "wall that thick" would go up. 2x4 with spray foam was a potential solution to smaller wall with high performance foam, but it sounds like I need to just go to the mat with the builders on 2" rigid foam and a 2x6 wall with wet blown cellulose.
Being from your area I believe termites should be on your mind as well. Termites love eating through foam. I have used mineral wool to great effect and have used interior foam. I was going to use some foam on the exterior of a basement but have decided againt it because the termite issues are so bad around here.
-Your number one focus should be air sealing. Means that its part of the building contract. Gets rid of a lot of bad builders right away. Near complete air sealing will give more performance than more inches of any insulation.
-Second use mineral wool and/or cellouse insulation as much as possible. I love foam, but with the termites around here you have to be very careful with it.
With how shotty of workmanship I've seen around Iowa I would lean towards premanufactured homes. They can be customized and takes around a month to put up on site. Also when the pieces are put together you can air seal and do the continious insulation then. Lot less hassle, customizable, cost less and more consistent quality (not perfect - but better.)
A close second would be the post and frame construction. The longest lasting structures in Iowa are the Barns and Balloon framed houses. You can do a whole build with post and frame without foam, have the thickness and air sealing. Around Iowa construction crews know how to build these really well. Post and Frame allows for thermal breaks just like a foam board does. Wet cellouse the cavities and enjoy. Also air seal between the roof cavity and the interior ceiling - gets forgotton most of the time.
A 2x4 wall with 3.25" / R20 of closed cell foam (3.25" is the practical limit, since you can't trim it) is only about R1- R1.5 better performance than a 2x4 wall with 3.5" /R13) of open cell foam (which air-seals better than closed cell foam) due to the severe thermal bridging of the 25% framing fraction. Without the exterior foam that would be about R11-R11.5 "whole wall" vs. ~R10 "whole wall", after factoring in the thermal bridging. That's a ridiculously expensive R1-R1.5! Add in 2" of EPS and you're still just shy of R20 whole-wall.
If you want to buy that performance back without resorting to thicker foam, use 1" of foil-faced polyiso tight to the sheathing, with an overcoat of 1" of EPS (to keep the polyiso warm enough to stay in it's high performance range in your climate.) That gives you R10+ on the exterior (as opposed to R8-R8.4 with EPS), and would have equivalent or slightly better thermal performance to the ccSPF + 2" EPS proposal.
But it would have MUCH higher moisture resilience, since it can be left vapor-open to the interior (with 3-5 perm standard latex paint as the only interior vapor retarder), and has HUGE dew point margin from wintertime interior moisture drives, now that it's R10 on the outside of R23, rather than R8.4 on the outside of R20 ccSPF, with only a 1.5 perm drying path through the EPS the exterior, and only a ~0.3 perm drying path to the interior. With 2" of extrerior polyiso you'd have a higher labeled R, but slightly lower mid-winter performance due to the performance hit the outer inch of polyiso would take during cold weather. That outer-inch of EPS increases in performance at lower temps, balancing the lesser hit the warmer intermediate layer of polyiso would take. It's still an R-20 whole-wall, which at R13+ 10 meets IRC 2012 code min in Zone 6.
If you caulk the framing to the sheathing and detail the sheathing as an air barrier you'd do as well with damp-sprayed cellulose as you would with open cell foam, and slightly higher R using R15 rock wool, provided they are installed perfectly/obsessively.
If you bump that out to 2x6 with cellulose or ocSPF it adds another ~R4 to the whole-wall R, but you're then a bit marginal on exterior-R for dew-point control- you'd have to add another half-inch of foam (on either layer) or more to bring it above R11.25. All-polyiso would get you there at just 2" from a labeled-R, point of view, but it would be very marginal indeed on a performance basis due to the cold temp derating problem of polyiso as the outermost layer.