Insulation Material for Conditioned Basement

Having recently purchased the Pretty Good House book, I’m impressed with everything it but have recently come up against a question. I’m in the process of detailing a to be built new conditioned basement and I found the basement insulation detail on page 98 to be a great foam free way to insulate from the interior. A discussion with another professional recently made me wonder about letting the concrete dry to the inside with all the insulation on the exterior. Typically I like the idea of keeping the concrete on the outside of the vapor control layer, especially with the detail found in the PGH book in which any inward moisture drive would just hit the back of the Stegowrap. This professional was wanting to allow concrete to dry to the interior for multiple years. I’m not opposed to insulating on the exterior but it just shifts other details in the design.
Curious to hear thoughts.
GBA Detail Library
A collection of one thousand construction details organized by climate and house part
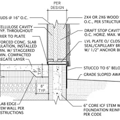
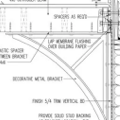
Replies
Concrete doesn't need to dry, and you don't want whatever moisture is in to enter your house. In basements in particular the whole game is keeping moisture out.
Thats exactly my thought and understanding as well, hence the sweet detailing of the poured walls with Stego continuous from the sub slab all the way to the top plate. These particular clients are especially mold phobic so my thinking is even more hydro sensitive than my usual PGH techniques.
Two years is silly but it is a good idea to give it some time.
1 month with a working HVAC system and a real dehumidifier is usually the minimum before I start a basement.
I looked at page 98 of PGH. Cellulose makes me nervous in a basement but I might just be old fashioned!
Feel like describing the detail you refer to on pg. 98?
From outside in: EPS foam, foundation waterproofing, concrete foundation wall, Stego sub-slab vapor retarder extended up the full height of the foundation wall, dense-packed cellulose, 2x4 wall held off the concrete, variable permeance membrane, drywall.
To be clear, it's not foam-free; there is exterior EPS that helps keep the concrete warm enough that there shouldn't be condensation in the cellulose. If you eliminate the EPS, or the foundation waterproofing (NOT damp-proofing), or the interior polyethylene vapor retarder at the wall, it would be a risky assembly.
In high-humidity Washington, DC that would be a risky assembly. The problem with insulated basement walls is that there is no drying vapor drive -- the interior is always warmer than the exterior, so the vapor drive is from interior to exterior, but there's no ability to dry to the exterior. The variable permeance membrane won't keep vapor out because it's open when humidity is high and closed when it's low, and with no drying it's never low. With interior conditions of 72F and 50% the dew point is in the low 50's, which the interior of that assembly could reach even with exterior insulation. It's could be a moisture trap.
I want to expand on my answer.
In a basement, the wall will never have less moisture than the interior air, and can have more. The most that it can ever dry is to the point where the wall and the interior are at the same dew point. It's possible that the wall is at a higher dew point than the interior, if heat vapor drive is preventing drying to the interior, or if there is a vapor trap.
When looking at basement assemblies, condensation is the wrong measure. While condensation is bad, mold can form at lower humidities than the dew point. The thing you have to look at is the moisture content of the wood, if that exceeds 15% you start seeing problems. The moisture content of the wood will reach equilibrium with the surrounding air, depending on the temperature and humidity. It's a complicated relationship best summarized by a chart like the one here:
https://www.woodworkerssource.com/wood-moisture-content.html
So let's say inside the house it's 72F and 50% RH. That's a dew point of 52.5 and at 60F that would be a RH of 77%. Looking at the chart and interpolating between 75 and 80, at 60F and 77%RH the wood moisture content is about 15.2%. That puts you in the danger zone.
Now, here in DC, interior conditions in the summer are probably going to be more like 78F and 60%. That will be upstairs, the basement will be cooler but probably the same dew point. That's a dew point of 63F. At 60F you'd be seeing condensation, but even at 65F you'd be at 94% RH and your wood moisture content would be in the 20's.
Our soil temperatures are in the 50's so it's entirely reasonable to expect basement walls would be in the mid-60's in the summer.
I believe in my climate that no permeable basement assembly is safe.
"It's possible that the wall is at a higher dew point than the interior, if heat vapor drive is preventing drying to the interior"
If the wall has a higher vapor pressure than the interior room, it will have a net flow of vapor from the wall to the room.
It seems all the principles involved (with the exception of any capillary wetting from ground contact) are the same as any foam clad wall. Do foam clad walls rely entirely on vapor drive shifting directions seasonally?
Not necessarily seasonally, but there has to be some ability to dry. For example, a wall in Miami is going to dry to the interior year-round. But in most of North America all the drying force is toward the exterior in the winter and toward the interior in the summer -- the side that is colder is also drier. Basements are a special case because the exterior is always the cold side and usually the wet side. It's very common here to open up a basement wall and find soggy insulation, you can't count on there being enough drying to the interior to be effective.
"In high-humidity Washington, DC that would be a risky assembly"
Which specific part, the use of a stud wall?
Conceptually is seems much the same as the idea of using interior foam, then building a stud wall in front of that foam. Is that a NO-GO is the D.C. area as well?
I don't like any permeable materials below ground.
Are the studs in front of the blown insulation, or surrounded by? If there was a barrier on the back of the studs I might feel a little better.
DC,
I'm referring to Assembly #2 described here by Martin:
https://www.greenbuildingadvisor.com/article/three-ways-to-insulate-a-basement-wall#:~:text=For%20interior%20insulation%2C%20you'll,boards%20or%20spray%20polyurethane%20foam&text=If%20you're%20insulating%20a,use%20of%20R%2D16%20polyisocyanurate.
He states:
"Your rigid foam layer needs to be thick enough to prevent condensation problems. A conservative approach calls for at least R-2.5 of rigid foam in Climate Zone 3, at least R-5 of rigid foam in Zones 4 or 5, at least R-7.5 of rigid foam in Zone 6, and at least R-10 of rigid foam in Zone 7 or 8."
I'm just wondering how this approach is any different (hygrothermally) than the foam being on the outside, in terms of dewpoint/RH calculations and such.
I'm not saying it's the wall I would build, just trying to understand what set's things apart here.
Deleted
Yes but at least the foam is not inside the conditioned living space. Would an appropriate amount of rock wool on the exterior serve the same purpose? When you refer to waterproofing, do you mean some form of applied WRB above and beyond standard detailing even with a dimple mat?
In this situation, yes, rigid mineral wool could be used in place of the EPS.
One of the other PGH authors drew that detail; it's not one I have used or would likely design, as it would be risky if everything wasn't designed and implemented correctly. The author uses WUFI Passiv and can assess hygro-thermal safety using their software. If you don't have that capability or can hire someone you trust, I would stick with more conventionally accepted assemblies.
For below-grade foundation walls, I insulate the interior with foil-faced polyiso and leave the exterior concrete exposed, as it's a nearly ideal exterior material and it's simple and safe from a building science perspective. While it does put foam on the interior, to me that is better than having an assembly that could result in mold. I usually try to talk clients out of basements so we can avoid this kind of discussion.
For waterproofing, I mean any system that is truly waterproof; there are many. In some cases it can be damp-proofing with a dimple mat; in some cases it's an elastomeric membrane with or without a dimple mat, or some other mix, depending on site and soil conditions, local practices and available contractors, and the project goals. In all cases the foundation drainage should be done well, ideally with a secondary/backup system.
The ideas in the book are for thought and inspiration; we were careful to note in many places that we are not recommending the details as universally ideal.
Michael,
"I usually try to talk clients out of basements so we can avoid this kind of discussion."
Yes.
Michael, foil faced polyiso on the interior as you described is my standard detail. Do you typically build out a stud wall beyond that to fill with cellulose?
I too like leaving concrete outside the main assembly in contact with the ground. The site is sloping so a walkout basement is something the clients are really leaning towards.
You wrote - "This professional was wanting to allow concrete to dry to the interior for multiple years."
I'm looking at a flooring industry article, which has a "rule of thumb" that a fresh slab will dry to a suitable moisture content at about 1" per month. So 4" slab on grade would be effectively fully dry after 4 months.
As a precaution you could postpone installing the interior vapor barrier, insulation and finishes for a few months while you proceed with the rest of the construction, assuming that fits your construction schedule and sequencing. Four months would see a good portion of the moisture dissipate.
I lined up the face of OSB with the face of foundation wall, applied Bituthene waterproofing to the foundation wall, and applied two layers of 1-1/2" XPS foam to the exterior from the footing to the top plate of framing. It's such a simple approach I'm surprised more houses aren't built the same way. Zone 5.
Thermally, that's a good approach. The downsides are that without a termite shield, bugs have a nicely concealed route for getting to the framing--they LOVE burrowing through XPS--and that if your concrete work is not absolutely perfect, you don't have room to adjust the framed walls. (Some foundations are perfect but some are pretty far from it.)
True. We're not in termite territory. I find the ins and outs of the foundation can be spanned by the XPS. Once a coating is applied where it's exposed any issues disappear.
Hey all, really grateful for all the feedback and the Q&A spotlight. Lots of options. I'm curious as to what you all would consider for fully insulating the exterior of the foundation wall?