Pressure-treated lumber reuse
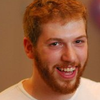
I have a fairly large deck, ~600 sq. ft., that I am replacing. The old deck was built in the 80s, and I suspect from pressure treated lumber. It seems you can’t take this stuff to the recycle plants or to the reuse shops. What are some ways to reuse the wood?
GBA Detail Library
A collection of one thousand construction details organized by climate and house part
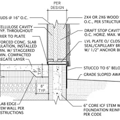
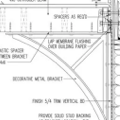
Replies
Its prob better than the new stuff you get, as they changed the formula. build a new deck, sell it, or burn it to keep warm (just stay upwind lol)
Funny you say this, the reuse shops will take newer wood..
The old stuff was CCA, which contained arsenic. The new stuff is usually ACQ or MPS, both of which are heavy in copper.
You can re-use it for the same things PT wood is always used for. It is much better for ground contact than the newer formulations, but people generally avoid using it where it might leach into garden beds, or in areas where children might have contact with it like play structures or picnic tables.
I made knock down saw horses out of the last deck we took down. Can also use it for shelving and sill plates. I'd look at it more for non structural applications though.
You may be able to use them for the new deck. The bottom side of the boards have not been exposed to the sun, which is what does most damage to the deck. Flip them over, clean them, and see if you can just nail them down again. I've doubled the life of several decks that way. If you're not changing the layout, the deck structure may also still be OK. It is often possible to change the metal hangers, possibly bolts and other structural fasteners, etc. Sometimes it's just the ground contact pieces that need replacement. CCA treated lumber is surprisingly durable, and reuse is certainly worth it.
That said, you need to pay attention to doing this right. Poorly built decks can be a significant safety hazard. The higher they are, the more dangerous. Use appropriate caution. If you are re-using the existing structures, you should pay careful attention to the connections between the deck and the house and other primary supporting structures. If you are designing the deck and/or doing the work yourself, get a copy of the DCA-6 deck construction manual.
Hi Ryan -
A bit of an aside but: if you are rebuilding your deck, one of the most important durability details is to either:
1. NOT attach your deck to the main structure, or,
2. use deck spacers (https://www.deck2wallspacer.com) or Maine deck brackets (https://deckbracket.com/product/deck-bracket/) to pull the deckl ledger away from the main structure and allow flow-through drainage at the deck ledger.
Peter,
Properly flashed, a ledger would never allow water to get into the wall. I like to channel water to the outside, as we do with all other cladding details, rather than make a largely inaccessible space between the ledger and wall.
I’d be concerned in my area with leaves building up in the gap between the ledger and the deck. I have a lot of oak trees, and decomposing oak leaves make an acidic slop that rots and rusts things more than you’d expect.
There seem to be two schools of thought when attaching a deck to a house: flash it great, or put a gap. I think flashing is better in many cases than a gap since stuff can build up in a gap and cause problems that you aren’t expecting because you think the gap is protecting you.
It’s always best to design things so that they don’t need maintenance whenever you can. Doing this avoids all the problems that come up from people not doing proper maintenance.
Bill
Bill,
I remember when the standard detail for deck ledgers was a caulked joint, and the ledger was seldom pressure treated. It wasn't a surprise that there was a spate of deck collapses due to rot, and the absence of any horizontal restraint on the ledger/deck connection.
One thing I find really helps with water management is to set the deck joists one inch higher than the ledger. This leaves a gap between the decking and the ledger that allows water and debris to drain onto the cap flashing above the ledger, rather than accumulate.
It's definitely a belt-and-suspenders approach, but Hammer & Hand's detail for this uses Deck2Wall spacers, and flashes over the top, which would prevent issues with leaves and such: https://hammerandhand.com/best-practices/manual/9-structure/9-1-deck-ledgers/
Brendan,
I you look at their detail you can see what I was getting at about the decking creating a dam for debris and water. What typically happens is it works it's way along to the ends and rots the cladding there. Lifting the joists solves that problem. End dams on the flashing help too.
Instead of raising the joists, why not just start the decking out a little from the ledger to leave a small gap for drainage? Even a 1/4” would probably be enough for water to drain ok. I’d still be concerned about rotten leaves and the like sitting on the flashing though.
Bill