Potential vapor issues within wall assembly

I am planning on building this wall assembly in zone 4. My concern is the assembly’s ability to dry. I have already installed the kraft faced insulation on the interior, so it will be quite costly to replace that. I should’ve went with unfaced here.
We are about to put up the zip sheathing with continuous 2″ aluminum faced polyiso in front. Will this create a vapor sandwich with the kraft faced batts on the interior side?
We are providing an air space in front of the polyiso, and the polyiso is at R-13. Code gives a minimum of R-5 continuous insulation with R-20 in the studs, or R-10 continuous insulation with R-13 in the studs. As you can see in the attached wall section, we are well above that.
GBA Detail Library
A collection of one thousand construction details organized by climate and house part
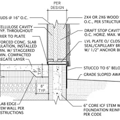
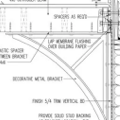
Replies
newbie718,
Kraft faced batts have a perm rating of 1 which is twice that of a coat of latex paint. I think your real problem lies in the air conditioned parts of your year. I have not worked in your CZ, so I think it best for others to weigh in on the sandwich potential of your lay up. I am guessing that you will need to be very attentive to sealing all air gaps from the interior to the stud bays.
You got that backwards--Kraft facing is about 1 perm, but latex paint is 2-10 perms. Or maybe you meant that Kraft facing is twice as tight against moisture as latex paint?
In your climate zone, your design should meet code, which requires a class 1 or class 2 vapor retarder when you don't have a good ratio of exterior to interior insulation. When using latex paint, which is 2-10 perms, over drywall on the interior alone, which is a good proxy for a safe assembly in the heating season, you need at least 15% of the total R-value in the foam layer to control the dewpoint and keep the assembly safe.
While air leaks cause many more problems, after writing an article in 2011 about flash-and-batt, a similar approach, I receive many calls and emails from people who were experiencing heavy condensation, and a lot of assemblies don't show signs of failure for many years, so it's something I am cautious about.
You have about R-30 in interior insulation (moisture can move readily through bricks) so you would need at least R-5.3 in the foam layer for cold-weather dewpoint control. 2" of polyiso easily exceeds that so I think you should be safe. Just make everything as airtight as you can.
As for cooling, the polyiso should block most vapor from driving toward the interior, and any moisture that does make it through should be able to dry through the 1-perm Kraft facing and the 2-10 perm latex paint. Just don't use impervious interior coatings such as vinyl wallpaper, and don't add anything more impervious than you already have.
Michael,
I think we may both be correct about the perm rating of latex paint. See the two charts on this link.
https://insulationinstitute.org/im-a-building-or-facility-professional/residential/installation-guidance-2/moisture-management/vapor-retarders/?cn-reloaded=1
Not sure how one knows which version of latex film is at play. I date back to oil base paints.
My main reason for deferring to others to guide Newbie is the presence of the brick wall (?) or nogging. A term I have never encountered. A potential moisture reservoir and thermal issue, particularly at the brick ledge would seem to be at play. I remain hesitant to judge the potential for concealed moisture build up. A CZ 4 could be a high humidity and cooling dominant on or a drier one.
Molding on the back of drywall in higher humidity extended AC regions is a real concern. Worse still Kraft perm rating goes up in higher humidity, so depending on the actual performance of the latex paint one could effectively have the dreaded vinyl wall paper disaster down the road.
Good point; in my specifications I always write, "standard latex paint," and sometimes even add, "not vapor-barrier paint" unless it might be desired in a specific situation. I have also heard that multiple coats can drop the perm rating of standard latex paint. I prefer using variable permeance membranes because they are more predictably consistent.
Nogging is an old term for rough brick infill, such as you might have with half-timbering, or sometimes used in older homes as a fire stop or air barrier at bottom plates. It is a reservoir material. This chart shows that 4" of brick is 0.8 perms: https://images.greenbuildingadvisor.com/app/uploads/2019/06/21054247/U_AK_EXT_EEM-00259-1.pdf. But other sources say it varies widely so who knows. I know that brick is vapor permeable, and figure that in the center of the wall it's pretty well isolated. But you're right about the perimeter conditions.
That looks like a lot of ideas thrown at a wall. In zone 4 do you really need an almost R45 wall?
Either go with all batts and the two walls and skip the exterior rigid or eliminate one of the 2x4 walls and use the exterior rigid.
Even building a simple exterior 2x6 wall and only strapping the original brick/wood wall with 2x2 on the inside for drywall and wires is good enough.
The all batt options will need a warm side vapor retarder (ie faced batts). You can skip this with the exterior rigid option as long as you have sufficient rigid/fluffy ratio for condensation control.
Any of the above options will barely budge your overall energy use and won't effect how well the wall works as long as the masonry is not exposed to weather (ie behind some insulation and a WRB).