Polyiso and WRB questions for old/new home in New England

Hi there-
New to this site- i appreciate the wealth of information.
Thanks in advance for any guidance.
I am preparing to apply cement fiber siding to my under-renovation 2 family home in the Boston area.
Remaining portion of original home is from 1895. first floor consists of true 2 x 4, 7/8″ pine sheathing. This portion will get open cell spray foam insulation due to the code requirements (foam will provide R18 out of R19 required)
2nd and 3 rd floor were added this summer – new 2 x 6 construction, 3/4 inch CDX sheathing. These levels will likely get R19 or R21 fiberglass insulation.
New construction windows and doors were added, and all openings were properly flashed. House wrap applied.
In the process now of adding 1/2 inch polyiso to assist with R value and quiet noise of busy road over the house wrap. I understand now that this type of insulation doesnt handle moisture very well.
Exterior trim kits for windows already built- and trying to avoid any changes to windows that would make those useless.
Looking for recommendations that (hopefully!) dont incorporate a rain screen and dont require me to make changes to window trims already built. Would doing entire interior in sprayfoam reduce the risk of moisture developing behind the cement fiber siding due to minimizing air movement from interior to exterior?
Thanks for reading!
GBA Detail Library
A collection of one thousand construction details organized by climate and house part
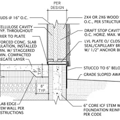
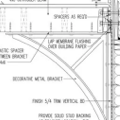
Replies
Frank,
If you want to add rigid foam insulation to the exterior side of a fiberglass-insulated wall, you have to follow certain rules. You can find out what those rules are in this article: Calculating the Minimum Thickness of Rigid Foam Sheathing.
In Boston, you are in Climate Zone 5. If you want to add exterior rigid foam to a fiberglass-insulated wall in your climate zone, the rigid foam needs to have a minimum R-value of R-7.5. That means that you need about 1 1/2 inches of polyiso, not 1/2 inch of polyiso.
Here are some suggestions:
1. Instead of using fiberglass insulation in the 2x6 walls, you could use open-cell spray foam. Because open-cell spray foam is not air-permeable, that type of insulation lessens the chance that interior moisture will reach your wall sheathing. It also allows the wall assembly to dry to the interior (because it is vapor-permeable).
2. Instead of using foil-faced polyiso on the exterior of the wall, you could use 1/2-inch EPS (another type of rigid foam). Look for a brand without a facing -- one that is vapor-permeable. If you do that, your wall assembly will be able to dry (slowly) to the exterior, reducing the risk.
You've learned that you need to think through your wall assembly details before beginning construction. Your statement that you are "looking for recommendations that (hopefully!) don't incorporate a rainscreen" is understandable (because you are facing these issues in the middle of your project) but a little sad -- because a rainscreen gap is a good thing.
Martin: Would he be better off skipping the 1/2 foam outside the wrap and instead installing 1/2 rain screen? Or, what about using Home Slicker or a similar rain screen that doesn't take up much space?
Stephen,
Your two suggestions would also work (and in fact would be safer from a moisture-accumulation perspective).
Martin and Stephen- thanks for your insight and ideas.
I am approx 7 sq out of 24 sq installed on the polyiso (rear of home non gable) . I will shed one single tear if I have to remove what i have done thus far in error.
Please correct me if I am wrong - but from reading your responses I have the following 3 options:
Option 1-- I can remove the polyiso, and instead install a 1/2 inch or 5/8 inch raingap over the existing WRB forgoing any additional exterior insulation- and keeping my 40+ window trims usable.
Option 2-- Continue with Polyiso, adding a rain screen product that is a 1/4 inch thickness - in this instance if the screen product doesn't incorporate a WRB, i would need to use either tar paper or similar to direct moisture down with gravity.
Option 3. remove polyiso and replace with eps, unfaced. in this instance do I need a rainscreen as well?
Again, thanks.
Frank,
By far the safest approach is to remove the existing rigid foam and to install 1/2-inch-thick vertical furring strips (or a three-dimensional plastic mesh product with the same thickness) to create a rainscreen gap.
The approaches that I suggested -- switching to unfaced EPS and switching from fiberglass insulation to open-cell spray foam -- move you away from the risky cliff in the direction of safety, but even both of these measures (implemented together) still leave you with a wall that isn't really recommended. Whether this wall will work depends in part on your future indoor relative humidity levels. The safety can be estimated by using WUFI, but I don't trust WUFI one bit. I prefer conservative walls to uncertain walls.
So the best advice was Stephen's: go with the rainscreen gap.
Martin- Thanks again for your time and advice- Stephen- thank you as well. Going w 1/2 inch rain gap. At least demo-ing polyiso is easy! Confused about rain gaps around windows, but I will figure it out. Thanks again.
Frank,
To address your concerns -- "confused about rain gaps around windows, but I will figure it out" -- I suggest that you read this article: All About Rainscreens.