Polyethylene is already installed inside. Is it good advice to install Blueskin VP 100 on outside?

We took on to finish a half-done catastrophic renovation, done by an array of different contractors who did not know what they were doing. The building sits on a cliff on B.C.’s Pacific coast, exposed to extreme winds with driving rain.
The Canadian building inspector demanded installation of a polyethylene vapour barrier on the inside over batt insulation siting in 2×6 wall. All walls inside are finished. Sheathing is plywood. Half of the outside is covered with Blueskin VP 100. Client insists on stucco as finish.
We want to built very well top and bottom vented rain-screen with 1 1/2″ cavity space behind the stucco.
Should we pull the Blueskin VP 100 off first and use something different as wind/moisture barrier on the sheathing or continue with the Blueskin on the remainder of the house?
We thought the product was good and suitable for this application and we spoke with the manufacturer about our situation. But I am not sure if we trap moisture with this assembly?
Christian Schimert, Dipl. Ing. (MSc) MARB (U.K.)
GBA Detail Library
A collection of one thousand construction details organized by climate and house part
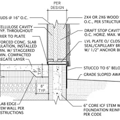
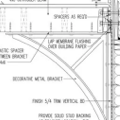
Replies
Christian,
Blueskin VP 100 is a self-adhered membrane that acts as both a water-resistive barrier (WRB) and an air barrier. One unusual (and useful) feature of the product is that is is vapor-permeable; it is rated at 33 perms.
This product will allow your wall assembly to dry to the exterior. So go ahead and install your vented rainscreen gap followed by the stucco cladding; you are good to go.
This is a fairly expensive wall assembly that will do an excellent job of water management. It's too bad that it is so poorly insulated, with only batt insulation between the 2x6 studs. You'd think that anyone building such an expensive wall could afford better insulation.
Martin,
Thank you, this is helpful. Yes the bad insulation is frustrating, but unfortunately nothing we can do about at this point in time. I was following some of the great discussions ongoing on your website. I became nervous about some comments in one of your discussions where some people seem to doubt that Blueskin VP is really vapour permeable enough to let any moisture, which made it into the insulation somehow dry out again. Others recommend Blueskin VP, but emphasized not yo use any vapour barrier on the inside of the wall. But maybe the latter recommendation is meant for walls with insulation on the outside of the sheathing and Blueskin VP?
Anyway, I am an Architect registered in the U.K. who grew up, studied and worked in Germany and also in the U.K. I have now 17 years local experience here in BC running large complex projects and in charge of detailing and working drawings for a renown architectural firm. I am just in the process to start my own business and have not that much experience with wood-frame construction. However, during this time I was astonished again and again about how things are done here in North America. In Germany I was trained to stick to the following fundamentals, which I see violated over and over again here:
- Insulation should always be on the outside face of the structural wall, wherever possible.
- Wall cavities have to be fully vented with 2" air space to make sure after building tolerances a minimum of 1 1/2" is kept at all times.
- Vent opening at the top must be slightly larger and designed such that the wind creates suction and that water cannot be blown in.
- This venting also applies to brick veneer. Why only make weep holes at the bottom??? why not go through the little extra expense and fully went??
- Try to use a vented cold roof for a pitched roof wherever possible. Air cavity minimum 5" to 6" unobstructed below the roof shingles or sheet metal. Continuous ridge vent with upstands and overhangs. Again opening at the top larger than air intake at the soffits.
- Wall assemblies should breathe. With brick or concrete walls, wherever large roof overhangs are possible and walls can dry off, use permeable outer finishes and delete the vapour barrier on the inside altogether. Use vapour barrier on inside only below the roof or where you have to seal the outside face of wall.
- It is an illusion to think one can create 100% vapour barrier in the field.
- Never ever rely on caulking or sealants. Detail with durable materials overlapping and leading the water to the outside.
- The flashing itself should be the waterproofing, not the underlying membrane. That one is only a second defense. Hire well trained, well paid master craftsmen to do the flashing (I know I am dreaming here with the local situation....). Good flashing is the key for the building to last. It is expensive, but in Europe people know and nobody complains....
- Flashing has to overhang and create drips. Any overlaps or upstands at vent openings etc minimum 4" and 6 to 8" at edges exposed to high wind speeds.
- Windows should be recessed into the wall. They should be sitting on a pan with upturned edges leading any water to the outside. Insulation should connect to the window frame to avoid any cold bridging.
- One should not use stucco ever in a wet environment like BC. The proper finish material for this region is a extremely high fired brick with closed pores (some of the clay turns into glass, this brick is called "Klinker" in Germany). This combined with large roof overhangs was used successfully for centuries in Northern Europe.
- When designing and Building use your common sense.....
Anyway I could go on and on and one has to adapt to the local market, but I am still scratching my head sometimes on what vast amounts people spend here on luxurious interior finishes and how little they are interested in spending on modern heating systems or building envelopes which will last. What an utter waste of precious resources.....
After many years of thinking I came up with the following theory: The problem is that we largely have a British style real estate market here in North America. In Great Briton for centuries most houses were built by developers on leasehold land. Therefore people are not attached to their homes and buy and sell and move to better locations as they rise through the ranks. Also people use there home as an investment for retirement. So when they buy or build or improve a house from beginning on the main question is how well they can sell it. With energy prices still low compared to Europe, this way of thinking puts the emphasis on flashy kitchens and bathrooms...you cannot sell value which is hidden in the walls. Developers only follow along with the market. I believe for instance that about 60% of the people who buy a so called Craftsman Style Home only buy it because there is a large market segment who loves those and therefore they think they can sell it easier. And they are right off course because so many think like that. In continental Europe people build a house for generations to come. They want their grandchildren to inherit the house and to live in the same community. This will probably change now in this global world...
Anyway: The people are the market and only changing their way of thinking can change the market.
Christian,
Most of us who read GBA regularly scratch our heads about the way houses are built in the US as well. Lucy