Pole building wall insulation

I’m having an 800 square foot shop built using post frame construction in Bellingham, WA (Climate Zone 4 Marine). It’ll be sort of an evenings-and-weekends space, so it’s potentially a bit less of an energy hog than the same building would be as a residence.
The walls are mostly horizontal 2×6 girts on 24″ centers (“bookshelf” style). Plan A (before I really did enough research) was T1-11 on the outside, housewrap, fiberglass batts between the girts and then interior drywall.
A couple of the walls are fire-rated, an so there’s a layer of 5/8″ GWB between the girts and the housewrap, the girts are on 12″ centers, and every other one is a so-called L-girt, where a 2×6 under the outside edge (vertical cross section), helps support the girt (picture attached).
Furring out the framing another 2″ would actually make for a smoother interior finish, as it would match up with the corner building posts and overhead door frames.
I’m open to suggestions, but in terms of specific questions:
1. Is there a commercial furring product that provides a thermal break that would work well for this application?
2. If I go with batts in the wall, should I worry about the depth variation from the L-girts? Should I maybe cut-and-cobble some 1.5″ foam in the “low spots” to even it out before installing the batts?
GBA Detail Library
A collection of one thousand construction details organized by climate and house part
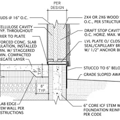
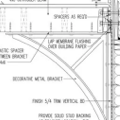
Replies
Frank,
Is the pole barn built? (I couldn't tell from the description.) Are you open to installing sheathing under the T111? That would enable you to air seal the structure and improve performance.
Steve,
It's *mostly* built. There is already housewrap and T1-11 on the outside (both over GWB where the walls are fire-rated), but the inside is still open.
That's one of the reasons I'm considering doing a cut-and-cobble and some air sealing before installing insulation between the girts.
Frank,
As you probably know, the big problem with trying to insulate a post frame building is establishing an air barrier. T-111 isn't a great choice for siding, because (lacking sheathing) it is hard to air seal.
If you have the patience for a cut-and-cobble job, you are likely to have less air leakage than an approach that just uses batts. Although I generally try to avoid the use of spray foam, there is no doubt that spray foam would do the best job of air sealing. (If you go this route, you should specify open-cell spray foam or one of the newer environmentally friendly varieties of closed-cell spray foam.)
For more information on these options, see these three articles:
Cut-and-Cobble Insulation
Flash-and-Batt Insulation
Next Generation Spray Foams Trickle into the Market
I would urge you to fur out the stud space to bring everything even with the posts. The easiest approach would probably be to run some 2x6s through a table saw, ripping each 2x6 into two studs, each 2 inches wide. Install these new studs vertically, to reduce thermal bridging.
Frank,
It appears that you have a gravel floor. Do you plan to add a poured concrete slab?
Steve,
Good catch!
Frank,
Steve is right to ask the question. It's particularly hard to air seal a wall if the building has a gravel floor.
.
These buildings typically get a slab poured as one of the last steps.
It's getting 2" of XPS over the entire base and perimeter (unfortunately the XPS was ordered before I learned about the awful GWP of the blowing agent).
I'm going to try and find a local source of 1.5" EPS and I'm planning on building a hot wire cutter. I was going to cut-and-cobble and seal the ceiling (unvented cathedral) anyway, so this will just be a bit of extra practice before I have to do it up high :).