Plywood floor on-grade

Can anyone give me advice on an on-grade plywood floor? This would be used in a cold climate, and would be built in lieu of a concrete slab on grade, in conjunction with a shallow frost-protected foundation. As I understand it, this is the material sequence, from the top down:
finished floor
plywood subfloor
plastic vapor barrier
4″ XPS foam
(another vapor barrier?)
coarse gravel for leveling and radon collection
undisturbed subsoil.
This assembly would be floating inside of the concrete SFPF. Would any special detail need to be used to support a non-load-bearing wall. What details would be needed for an interior load-bearing wall? Would the plywood need to be pressure-treated, or would standard exterior grade plywood be satisfactory?
If this system really works, I see it as being faster and cheaper than a concrete slab over foam, and much warmer underfoot.
GBA Detail Library
A collection of one thousand construction details organized by climate and house part
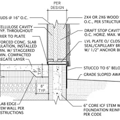
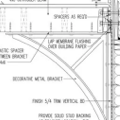
Replies
Jack,
Load-bearing walls need concrete footings.
If there are no load-bearing posts or load-bearing walls, it might work, but I wouldn't want to use the system in my house.
A grand piano? A floor-to-ceiling bookcase? I dunno ... just makes me nervous.
I agree with Martin, a typical slab is going to have a compressive strength of at least 2,500 to 3,000 psi. I'm not sure that 3/4" plywood and 4" of rigid foam is going to come even close to being able to bear what you're going to need it to bear. I would also consider the fact that plywood is unitized and will create weak spots in the assembly everywhere there is a join, also allowing areas for moisture migration etc. Overall this seems like a bad idea. However, if you decide to do it, post some pictures in a year or two. I'd like to see how it holds up.
Jack,
When you consider the cost of treated t&g 3/4" plywood, treated sleepers, some kind of treated or rot resistant underlayment, and the labor to install it all, you might as well do it right and pour a slab. The system you suggest will be nothing but trouble over the long term.
Martin: Your blog about putting foam under foundations (https://www.greenbuildingadvisor.com/blogs/dept/musings/foam-under-footings) first gave me the idea that such a system might be feasible. You noted that common blue Styrofoam had a compressive strength of 3600 lbs/sq ft, which is greater than an acceptable soil loading of 3000 lbs/sq ft. And there are Styrofoams available with compression strengths up to 14,000 lbs/sq ft. However, the point loadings that you mention do make me wonder. Presumably a 3/4" subfloor supported on 16" centers would support one leg of a grand piano, so if that same subfloor were evenly supported to the tune of 3600 lbs over 1 sq ft, would that be sufficient support? Perhaps two layers of 5/8" or 3/4" plywood would be advisable?
I was also curious why you said load-bearing walls need concrete footers. The Permenant Wood Foundation people think that 2x8 and 2x10 PT planks can be used as footings on a gravel base.
http://www.southernpine.com/applications_permanent-wood-foundations.asp
http://www.southernpine.com/downloadpdf.asp?filename=ref400.pdf
Alex: I agree that one might want to take care in placing the joints of the plywood relative to any internal walls. Do you think that there will be a moisture migration problem if there is a layer of coarse gravel, 4" of foam, and a sheet of plastic for a vapor barrier?
Peter: I'm wondering if pressure-treated plywood will be needed at all, since it is not in contact with either soil or gravel. I can understand why sleepers might be needed under a load bearing wall, but I'm less sure if they would be needed under a non-load bearing wall? I'm not a building engineer, so I was hoping someone with those skills could analysis this assembly.
As far as "doing it right", this forum specializes in finding alternative ways of doing it right. :) I can see a number of benefits to this floor system -- if it works. Lower embodied energy in plywood, vs concrete. A warmer, softer floor for those, like me, who go barefoot or in stocking feet indoors. Easier for an owner-builder to make. Easier to modify the sub-floor plumbing if something should go wrong. What's not to like?
Jack: Bear in mind that the "100 psi foam" is 100 psi at 10% deformation, if I recall correctly. Here is some data on EPS; I did not dig into this for XPS because I decided to use EPS, but I think you'll find that XPS is similar. 1% and 5% deformation are within the elastic limits of EPS and the foam will return to normal when the load is removed. 10% deformation will be permanent. Here are the numbers for a high density EPS: at 10% def, 50 psi. At 5% def, 43.5 psi. At 1% def, 18.6 psi. I believe the Dow web site says to use a 3:1 ratio to avoid creeping for XPS. I'm not comfortable with 5%, so an advertised 60 psi EPS is 20 psi in use. Good luck w/ the floor idea. I've looked at it, too, and long ago discarded it. A shed? Fine. A house? No. john
John, thanks for pointing out the deformation problems. From the Dow web site I found the following for their HighLoad XPS Styrofoams (40, 60, and 100 psi). 5% deformation of 4" of foam is almost 1/4", which is a lot. It looks like it would indeed be prudent to either use a thick plywood floor to spread any loads, or else use the higher-rated Styrofoam, or both.
http://www.dow.com/webapps/lit/litorder.asp?filepath=styrofoam/pdfs/noreg/179-02548.pdf
A little bit on a tangent, but an fyi ... Advantech (Huber Inc) is a water resistant subfloor OSB. Their installation instructions for the product over a slab require it to be on furring sleepers in addition to an added poly vapor barrier on the interior of the slab.
My take: They seem pretty cautious about even the accidental exposure of the treated subfloor to moisture for long term use.
Hope the tangent isn't off topic.
Joe
Good luck deciding which foam to use, too. Blue foam is "standard normal", but after a lot of reading, I decided to go w/ EPS instead. Cheaper, "greener" (as it were), and less water absorbent. Debatable, but that seems to be the latest consensus. I wrapped a small piece of each in lead and they have been sitting on my window sill, submerged in water, for a few months. In a year or two I'll take them out and check them out.