Choosing a Wall Assembly

In the attached image I’m showing 3 wall design options (A, B, & C) that I’m trying to evaluate and select from. My criteria are listed below. Please let me know what you think of these 3 options and whether I’ve overlooked anything important, especially in terms of performance and risk. Thanks!
The design is for stock house plans that might be built in any North American climate zone. So I want details that require minimal tweaking, particularly with regard to dimensions. I’m working within the IRC 2021.
I’m looking for an optimal wall design that doesn’t stray too far from what most average builders are comfortable with building. Option B ranks best, followed by C.
I want to use low GWP materials, so I prefer cellulose insulation over mineral wool and rigid foams. Options B & C rank over A.
In terms of vapor control Option A seems to offer the least risk. But is it significantly different from B and C? On a side note, in Option C is there any advantage to putting the retarder between the 2 layers of insulation, as shown, or should I keep it simple and have it just behind the gypsum board?
Complexity: Complexity usually correlates with higher cost and more possibilities for construction mistakes. Option A definitely is the most complex. The rainscreen and cladding has to attach through 2″ of insulation. Flashing of openings is substantially more complicated and labor intensive (and probably costs more). Option B is closest to what builders are used to. Option C is only slightly more complicated than B and offers savings in lumber costs.
Notes:
All framing would be 24″ o.c. except Option A 2-story applications, where 16″ is required by code. Option A single story designs would have 24″ o.c. framing.
I based the insulation requirements on U-values (IRC2021 Table N1102.1.2), not R-values, and all 3 options have “whole wall” insulation values between R23-24. So the amount of insulation is not a factor in my choice between the 3.
Where Class II vapor retarders are shown, I’d welcome suggestions for products you consider suitable.
GBA Detail Library
A collection of one thousand construction details organized by climate and house part
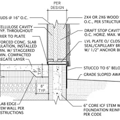
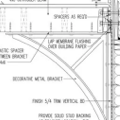
Replies
I have built option A and find it a pretty simple wall. This won't be the case in any place where exterior rigid is not part of code, so might not work in warmer climate.
Wall B and C are about the same to me, I think B is simpler to build but trades might complain that you can't get precut 2x8.
In either case, I would make sure the wall can be built with bits from a box store, so 1.5" cellulose batts might be nice but you want to be able to use fiberglass batts or rolls that fit in there as an option. Putting the VR inside the wall does work better but it is too far from standard build work flow. I think in climates that need interior VR, it is simplest right behind drywall.
That was helpful, thanks.
I'm not a builder, so I was wondering if a builder ordering for a whole house might be able to get a lumber supplier to precut the 2x8s as a special order. That would cost, of course, but might be cheaper than doing it on site. Is that sort of thing done?
I definitely want to favor materials that are readily available. But I do also want to introduce more "green" materials to the extent that I can. That's why I thought about using cellulose instead of fiberglass or rigid foam. Nu-Wool makes batts in 1.5, 2.5, 3.5 and 5.5" thicknesses. So it is available at least through them. But no, it wouldn't be available at a big box store. I'm going to include dense packed cellulose as an alternative. That should help.
I like the simplicity of the concept of 2x8s. But I've inquired here on GBA before and people seem to shoot it down, suggesting double walls instead, which seems to me like a lot more labor, building 2 walls instead of one and introducing a host of additional work with fireblocking, bucks at door and window openings, etc.
I think maybe I'll stick with 2x8. People in zones 1-3 can simply use a 5.5" batt insulation and in zones 4-8 they can go full depth with batts or more easily with dense pack. The only potential drawback is cold sheathing.
Thanks again.
jgsg,
I'm struggling with the original premise. I wouldn't use the same wall assembly here in coastal BC as I would on Mount Washington 200 kms away - nor would our building code allow me to. Isn't an assembly designed for every climate zone in North America optimized for none?
"optimized for none"
True. This is one of the challenges of designing stock plans. I have to try to find a good balance, the best that I can anyway. Surely you are familiar with the many companies that offer stock house plans. This is not a new problem. A lot of builders and diy homeowners look to stock plans. I'd like to try to improve the product based on the kind of knowledge we find here at GBA.
The majority of the the new housing starts in the USA are in climate zones 3-4, with zones 5-6 following. So if I can do something that needs only minor adjustments to reach 1 and 8 I've done better than what is generally available.
Anyhow, the options I've shown in the image all meet or exceed IRC2021 for insulation values and vapor retarders.
By the way, my old architecture professors would be turning in their graves if they knew I was doing this. I should be designing Minimalist Modern Mansions for the wealthy, replete with all the latest "green" tech to make them feel better. But the reality is that most Americans don't live in "architect designed custom homes". I'd like to do what I can to make a positive difference. So most of my designs are between 1000-2500 square feet, planned for aging in place, with a focus on traditional styles that fit into existing communities. I'd like to detail them as well as I can so that builders who aren't up on all the latest in building science are challenged to do better than they're accustomed to. But I also need to balance that with detailing that doesn't break the bank.
Please excuse me if this sounds like a rant. I thought to use this opportunity to clarify in my own mind my goals here, my so-called elevator pitch.
I like that you are trying to do that. It's a niche area still, many home buyers want the most square footage they can afford... Do you have a website with your current pojects you would share?
I'm sorry I don't have a website yet. I will by the end of the year but I need a minimal catalog to start with. I'll also be approaching some of the existing house plan sites and hopefully be selling through them. Thanks for your interest!
Tim, I do have a channel on Youtube where I've been working out some of my ideas, in video form. You may find some bits and pieces of it interesting.
https://www.youtube.com/channel/UCoog_kGySiu9_fcHzG4iGmw
Jgsg,
I've spend a fair amount of time modifying stock plans clients have bought to meet our building code, and optimize them for our climate. My experience is clients usually don't know the plans need work until they submit them for approval and they are rejected. They then contact the supplier who directs them to the disclaimer buried somewhere on their website that says such modifications may be necessary. The changes often fundamentally affect the design, and often necessitate the input of structural engineers.
I don't want to be discouraging, but I just don't think stock designs that include contract documents work - and I think you are bumping up against the issues already. What would be the point of framing walls with an unusual dimension material (2"x8"s) if you are only going to put 5 1/2" of insulation in them? How will the designs deal with energy codes that limit the percentage of windows in the envelope, or regional requirements related to high winds or seismic? There are just so many variables when you try and cover a continent with disparate demands and varied climates.
My first impulse was to leave a snarky response but I'm not going to. I've learned a lot from you on this forum over the last year. So, thank you.
I will say this. The plans that cross your desk are the ones that don't work. But the plans that do work don't cross your desk. You don't see them. I'm trying to put mine in that category.
jgsg,
I'm sorry if my comments aren't supportive, I have just tried to point out what I see as the shortcomings of your plan. You have not responded to any of the practical problems I have brought up in this thread or your other one. I'll bow out and let those with more constructive ideas to weigh in.
Malcolm, regarding some of the practical problems you raised - I have solutions to some and I am working towards solutions to others, in part thanks to you and others here at GBA. I'm not going into it further here because it's not relevant to my original post. In general I try to avoid going off topic because there's a tendency for things to go that way anyway. It doesn't need encouraging.
I have personally constructed option A and find it not complicated. You could even show details with varying levels of exterior insulation to meet different criteria: anything from one layer of 1" to 2 layers of 2" say. Wrapping the WRB into the widows and doors takes about a minute longer per window and uses wider material. I've used siding materials that can span 4' so fewer strapping is needed.
Thanks. A was actually my starting point and I've got flashing details for entry doors, patio doors and windows all worked out with various exterior siding options. I ended up questioning it because I got curious to see if I could develop solutions that used lower GWP insulation materials.