Plans for radon mitigation in new home construction?

Lots of general info online but few details available.
It is suggested to rough-in a vent pipe to roofline and to function as a passive system (via stack effect) then check radon levels after occupancy to determine if an inline fan is necessary.
Each area (if sectioned off by footings ) should be vented.
Retrofit examples simply put a pipe into subslab pit area which is cleared of soil and suck out air with an inline fan
For new construction how much subslab perforated pipe should be run in each area?
Do you run a continous line around perimeter or at intervals across entire area? (or just a few feet at each area?)
If running much subslab pipe in the gravel layer won’t this create faults and cracks, the nemisis of a radon mitigation system?
Any suggestions?
GBA Detail Library
A collection of one thousand construction details organized by climate and house part
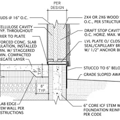
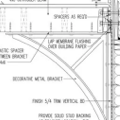
Replies
Most radon mitigation systems here in MN use a sealed sump basket so the perforated pipe serves double duty. The radon is vented passively through the roof, an inline fan could be added if needed.
First of all, same size gravel is porous, so use it. I run both sides of foundation with pipe. Pipe is in gravel and run toward sealed sump, and up through roof. No worry about cracks at pipe, level, tamp, prep, and pour slab.
As far as radon goes, low levels of radiation, by some studies, is good for you. Do you know anyone that radon has killed? I don't. Back when I was a kid butter and eggs were supposed to kill us, now they are good for you which I have proven by my own half dozen egg breakfast all these years. Lol
Doug, As I understand 4" pipe running vertically up to roof like a plbg vent goes into a length of perforated pipe under the slab in the gravel layer.('big O' we call it.) What does the sump do? Is it to join several dif. pipes? Why not just vent passively or if necessary w/ an inline fan? In new construction I don't see the need for the sump.
To AJ. We call it 'the big 'C' here. and yes I do know several people effected by it. Don't know for certain if radon played a part in it.
So this is what happens when you have more than a few hens, and the eggs just pile up? All things in moderation, remember.
Richard,
I note that you posted this question on two different GBA pages. Other readers may be interested in the answer that Peter Yost provided on that other page: namely, that radon mitigation system details are available in this online EPA document: Building Radon Out.
I am posting a relevant section from page 38 of the document.
Thanks Martin. I did put the question forward on someone elses 'Q&A' researched some more and decided I needed to ask it in my own.
Thanks also for the link. Now I need to figure out why I didn't find it in my searching.
It is the info I needed though.
Many thanks.
Richard,
The sump basket is for the sump pump, to keep the basement dry. The sealed sump basket is also serving as the collection area for radon with the 4" pipe extending through the roof. This may or may not be the correct method for radon gas control, to work in combination with drain tile.
OK. Using a well sealed sump basket , that looks good. The EPA document Martin recomended has filled in the remaining pieces.
First of all......over 20,000 people die each year from Radiation/Radon gas....!!
If you look to Europe, you will quickly learn that the best way to deal with Radon gas....is to install a Radon proof plastic membrane across the whole home area.
Radon gas that rises out in the open, dissipates quickly and does no harm, unfortunately during winter when homes tend to be sealed up to save on heating costs, Radon gas builds up. It tends to concentrate in corners and cupboards where the radioactivity it passed onto the dust that accumulates in these areas, it is especially dangerous to children who tend to play on the flour.
Cancer due to Radon gas, look it up!
Roger. Canada's CMHC in their publication emphasises the use of a plastic membrane and thorough caulking and sealing. They 'seem' to say that in most cases this would probably be enough,(because it can do the job of keeping the gases from infiltrating the house.) But they recomend at least laying the underground piping and stubbing a pipe out of the slab or going passive with 4"pipe all the way to the roofline then testing after occupancy. They just didn't give enough of the actual construction details as the EPA publication.
Richard - I used the EPA guideline that Martin mentioned for new construction just finished in Northeast Ohio. I wanted to have a passive system with the option to activate it . I consulted with a very kind and helpful radon system designer (two hours phone time - no cost) and the plumber that put in the system. Lesson learned: find a radon abatement system designer versus just a radon mitigation specialist. You do not need to hire a radon specialist for a passive system in OH. This gave me a superior designed-in approach to vent through the 2nd floor attic roof, but I had to show the builder the OH administrative code that applied to get his OK. The designer recommended an "X" pattern under the slab for my installation - I have one large open square approx 50'W X 45'D. The "X" is approx. 25' X 25' with one leg used to evacuate the sub-slab. He stated the peripheral approach was overkill, and he recommended rigid perforated pipe vs. EPA flexible for better installation and performance. He also stated that the "dual" use approach for the sump crock was *not* acceptable. If you needed to activate the system, you simply cannot get dependable performance. I wanted to use 4" pipe, because it has considerably more capacity to draw air. I found it was quite challenging to design the 4" through the walls with minimum sharp bends because of the open floor plan! I ended up specifying one 2X6 wall that also created more space for plumbing and HVAC feeding the second floor. Sharp bends increase the size of fan needed (and therefore the background noise) if you have to activate the system. After succeeding, we then downsized the floor plan. "Murphy's Law" happened: "failure to communicate" between builder, plumber, when siting the 4" sub-slab radon pipe coming through the slab forced us to switch to 3" through the walls to get minimum sharp bends. I learned that the sub-slab ventilation pipe, installed *above* the level of the drain tile, required 5-6" additional excavation plus gravel for the entire sub-slab for proper installation. This is not spelled out in the guide, although it is diagrammed. More cost, but it did the job to properly increase the passive sub-slab ventilation. I also insisted on getting gravel to grade all around the house to increase the opportunity for passive ventilation even more. A quick sidebar: In my high-efficiency build, we also put four inches of XPS under the slab for additional thermal break (next time, I'd reduce to 2"). The required code plastic vapor barrier was installed over the XPS directly under the slab. To be happy with passive installation "insurance," make sure to take simple measures to sound-isolate the radon stack. The plumber knew to insulate around the holes through the floors to prevent sound transmission, but we added foam gasketing around the hangers and sloping horizontal hangers. Total cost of passive installation was 1,000.00-$1,200.00 not counting the gravel to grade. This is compared with approx $650.00 and up that local radon remediation specialists wanted, and they typically just bored a hole in the slab and then connected a pipe to that - and offered little design assistance. Thanks for reading - I hope you find this helpful.
Lawrence
Thanks alot. Reading someone elses real life and extensive experience is very helpful. Sometimes guides leave out detail a builder is going to come upon(like the extra excavation) and experts either talk over my head or in a language I don't yet know .
We have a large chute w/ several mechanicals running up to attic so we should be able to fit it in .
The sound isolation is a good detail to keep in mind.
Q...Why only 2" of sub slab insul next time? Maybe it is just sufficient for your build, but I understand that experienced Energy Efficient builders are putting in R10-15 minimum these days.
Concerning sub-slab insulation for our *next* build, the *real* answer will be "it depends." I sought to balance energy efficiency with "sensible comfort." So we worked to eliminate any weak spots for the money. I'd love to see more trade-off analyses discussed in GBA.
In our current build, we have a nearly due south rear elevation and aimed for solar passive design. The south side *basement* windows have nearly 34 square feet of net free glazing due to our terraced garden view lot. Lovely view, happy place to work and play and great solar gain year round. The current XPS R-20 sub-slab insulation radically reduces the thermal loss plus provides that thermal and vapor/water barrier. In our first winter here, with *no* HVAC heating to the basement for Nov-Dec because I covered all vents due to basement construction, the day temperature was 68-69 F! In harsh Feb-Mar, with seven uncovered basement windows and thermostat at 68 F, daytime temperatures still inched into low 70s F on sunny days!