Plan Review – Zone 5a, ~800sqft

Hello everyone, I am here for a general plan review and a specific roof question.
The county has approved my plans, but I think you all might have a more keen eye than them.
I am in Zone 5a, Taos County.
Plans are attached. Site plan and title blocks omitted so I don’t dox myself.
I have an issue with these plans currently, my roof system. 1/12 pitch roof, and spec’d 7/8″corrugated roofing, which is not compatible per manufacturer specs. The standard choice for 1/12 low slope metal roofing appears to be standing seam. Another option, the “7.2 panel”, is also corrugated and has exposed fasteners, apparently its OK to use on low slope because of the profile shape.
The idea was to use corrugated for the roof and siding since it is the cheapest profile by a considerable amount.
The roof is an unvented shed roof: 5/8ply, 40mil peel& stick WRB, 4″ Polyiso (2 – 2″ layers, taped), 2×4 rainscreen, metal roofing installed over that.
The obvious answer is to convert to something within manufacturer guidelines.
Am I insane for thinking that I can get away with using 7/8″ corrugated without ill effects in this low slope assembly?
My reasoning is that the assembly behind the metal roofing is good (40mil peel& stick WRB, 2 layers taped foil faced poly, large rainscreen). I can definitively see how installing corrugated on a 1/12 roof over housewrap and OSB in an unvented assembly would be bad, so am I wrong for thinking this other assembly would be better?
Looking forward to your responses!
Mason
GBA Detail Library
A collection of one thousand construction details organized by climate and house part
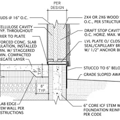
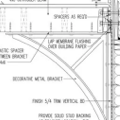
Replies
I would go with at least a 2:12 pitch for visual aesthetics. - it will just look nicer.
One big problem with corrugated metal roofing is that as the panels expand and contract during the day from the heat of the sun, the screws can be worked loose from the sheathing. There is a lot of info on the Metal Roofing Learning Channel - here are two videos to start you off.
Metal Roofing Learning Channel.
https://www.youtube.com/watch?v=-4i8UZQ07X0
https://www.youtube.com/watch?v=jlJpVabNAQY
And one from Exterior Pro Roofing.
https://www.youtube.com/watch?v=fdn6tAjemYg
Your plan is quite nice, although I think you should add some overhangs to help protect the windows (they can be "added on" after the main building envelope is sheathed and air-sealed).
The front door in particular needs a roof over it - have you thought of adding a shed roofed mudroom extending from left of the front door to the right edge of the house? It would only have to be 6 feet wide (north to south) and part of the shed addition could have access just from the outside for tools or patio furniture.
Loose screws would definitely be a problem.
I should reconsider 2/12 it seems, or commit to standing seam on the roof.
I've considered more overhang and settled on it as it shows for the plan, with the caveat of adding porches on later. A mudroom would be even better.
Maybe some ladder-style overhang out to a foot or so all around is called for.
I like your plan and most specifications. Taos Co. is CZ5B. FYI, I think Taos permits after 12/14/23 go to IRC 2021. Specs:
1. I’m pretty sure your footing needs to be 24” deep frost depth below grade. Recalculate rebars to soil condition or slope.
2. There should be a 12” 45° sloped joint between footing and slab to avoid concrete breakage.
3. I would use standing seam roofing @ 2/12 pitch, and I would add at least 24” overhangs to help protect windows.
4. Your drawings appear to show the fascia blocking the 2x4 vents. Make sure you use screens to protect vents from animal nesting.
I would suggest a few things I would do if this were my place:
1. I would consider framing at 24” o.c.
2. I would install a slider door in the Mechanical closet for easier access to your WH for maintenance and repair.
3. I would consider a TWH with the kitchen sink behind the wall. Any clothes washer?
4. I would install a taller door (8’?) to match the top of header of the door to the window headers on the front. It's just a pet peeve or mine. I think it would look better.
5. I would add a shed canopy over the front door and windows to protect them from snow and rain. Same reason, I would extend roof over back door and windows.
6. Windows 6, 7 & 8, I would use 2-2x10 header so I can insulate all headers.
7. A front porch would be nice too.
I'll ask them next time i stop at the county, I just bought the physical copies of the 2015 codes, so thats great. Time for a new set.
(1)based on AFI from 2015 irc and/or from revised builders guide to FPSF is how I got 16" below grade for monolithic slabs. But I will ask about it.
(2) Okay, i might have to retrofit the forms to accomodate that, since the manufacturer shows the detail like that. Definitely seems like a concentrated stress area.
(3) Okay, I definitely need to reconsider 2/12. Might make the nice metal roof more visible from the ground as well.
(4) completely overlooked that detail until now, thanks.
(1a) So did I, i chose 16's simply because its more common but have definitely considered advanced framing.
(2a) i was considering between bi-fold and a regular door. I thought about a pocket door but have never enjoyed using them. it does fit the space best.
(3a)What is a TWH? Stack washer dryer on wheels is next to the water heater in mech.
(4a)I'll consider it! It would look better. I made the window sills at 40" since wqe are a tall family. I'll model it and see how it works out.
(5a) I should add it to the plans now, because I was already thinking about adding it after-the-fact.
(6a)good point, I will do so.
(7a) Yes it would be, i was thinking of adding items around the house after the fact, but would make my life easier to add it now.
Deleted
For whatever reason I'm unable to reply directly to you Armando:
I'll ask them next time i stop at the county, I just bought the physical copies of the 2015 codes, so thats great. Time for a new set.
(1)based on AFI from 2015 irc and/or from revised builders guide to FPSF is how I got 16" below grade for monolithic slabs. But I will ask about it.
(2) Okay, i might have to retrofit the forms to accomodate that, since the manufacturer shows the detail like that. Definitely seems like a concentrated stress area.
(3) Okay, I definitely need to reconsider 2/12. Might make the nice metal roof more visible from the ground as well.
(4) completely overlooked that detail until now, thanks.
(1a) So did I, i chose 16's simply because its more common but have definitely considered advanced framing.
(2a) i was considering between bi-fold and a regular door. I thought about a pocket door but have never enjoyed using them. it does fit the space best.
(3a)What is a TWH? Stack washer dryer on wheels is next to the water heater in mech.
(4a)I'll consider it! It would look better. I made the window sills at 40" since wqe are a tall family. I'll model it and see how it works out.
(5a) I should add it to the plans now, because I was already thinking about adding it after-the-fact.
(6a)good point, I will do so.
(7a) Yes it would be, i was thinking of adding items around the house after the fact, but would make my life easier to add it now.
- TWH - Tankless water heater
- "Stack washer dryer on wheels is next to the water heater in mech." - More reason to use bifold, french or slider door.
- What are you installing for HVAC system?
- Any plans for Solar PV? Going all electric?
The house is all electric, plans are to hook it up to shore power initially and have the ability to go solar with it. I have a 2kw ground mount array nearby that it can hook up to, I've not looked into what I need to do to prepare the house panel or anything yet.
Two minisplits, one in the living area and one in the bedroom.
Make sure you have a ventilation strategy like an HRV and a humidity controled fan in the bathroom.
I plan on installing an ERV for bathroom ventilation, with a flat ceiling as noted by another user.
The foundation detail seems like it has some peculiar things.
1) I have never seen rebar in a footing placed like that. It is normally top and bottom
2) I would not use wire mesh in a slab like this. You should use rebar (probably #3) in an 18” grid.
3) your excavating the whole area? That doesn’t make much sense. You should just excavate where you need for the footings and if you need to get your slab height correct. Excavating the whole thing just to put the dirt back in (which now needs to be compacted is not smart).
4) already mentioned but the 45
5)you should at least overhang the front ( I would do a deep overhang there, but past 3’ you should probably get an engineer to ok cantilever). You could leave the back but make that and the roof standing seem for a nice look. Or you could also overhang that, different styles.
6)Even if your tall I would keep your windows at 3’ and just get a slightly bigger window if your tall. Unless of course they are behind counter or for some other reason.
7) having lived in a small house like this, one thing people often underestimate the value of blank wall space. I would carefully consider if every window is providing benefit.
8)If you do standing seam on wall especially without overhang, study the standing seam manufacturer details library and detail your windows perfectly. Also if you are not installing, make sure those installing are following your details. Standing seam is uncommon and is often installed and ordered wrong.
9) I would not do corrugated even on a 2/12 roof. The screws backing out is not unusual, especially I would assume in your environment.
10) If you do any oversize triple glaze glass doors and you are framing with advanced framing techniques, make sure you beef up your door king studs as these doors are heavy.
I didnt really look at your floor plan but I think the outside needs some work to make it look interesting. Right now it looks like a modular shed.
Oh also if you are going gas I would also recommend a tankless in this situation.
(1) Okay, I put it there based on how I read the code, "two #4 rebar in middle third of footing" but I'll look into proper placement.
(2) Okay, I will look into changing to a rebar grid, certainly more stiff.
(3)No, but it is worded as such. My first plan had the whole area being excavated, now I only plan to excavate where needed like youve said. I should have changed that. However, it is a prarie dog town, and there is certainly tunnels where the slab is going, which has me concerned.
(4) I might omit the interior insulation forms, that way the dug trench will have a radius/chamfer like that.
(5) I think I'm willing to consider up to 2' aesthetically on the front, and will likely match the back to it.
(6) Why? For aesthetics or some other reason? I have 3' window sills in the house im in, and even this 4' tall window feels like some of the view is cut off the top. Additionally all the 40" sills are on the south wall which will be 9-10' interior (1/12 or 2/12 pitch)
(7) I have been considering omitting either the hallway window or the transom window above the TV.
(8) If I do choose standing seam im unlikely to use it on the siding since detailing around them looks finicky, I might change to Hardie siding or stick to corrugated
(9)Okay, I'm definitely not doing corrugated anymore unless stepping up to 3/12 which I think is off the table.
(10) Only planning on dual pane at the moment, but understood
All electric currently, gas is out at the road, but having experienced gas and power outages here more frequently than anywhere else I've been, I'm strongly considering solar. I currently have 2kw with plans to expand.
1) other middle third direction
2) I don’t really know much about prairie dogs or local solutions but I would consider running large compactor over it. I would also consider upsizing and adding second rebar to bottom of footing. This can help span some voiding, we do this in CA in certain soils for added protection from voiding and soil expansion/ contraction. Lastly is you are anticipating possible voids under slab I may even do a 12” grid to help the slab span voids without cracking.
6) for a number of reasons: upsizing height of the window is minimal in the overall window costs. The lower sill height will look better, make your house feel way bigger, and you can still put desk in front of it.
8) standing seam is way more bomber than corrugated if detailed correctly, even on a wall. But yes you do need to learn how to do it properly.
The small house I lived in was fully off grid. It had a 3 kw power system but all heating and cooking was gas and it still ran the generator in winter occasionally. Definitely do an energy analysis to understand your needs if you are considering some sort of backup power system.
Edit: also don’t use titen bolts on your exterior walls just use standard j bolts. There is no reason for those. You can use them on interior if you don’t want to deal with j bolts in middle of slab.
mason,
I agree with the others about going to a 2/12 roof, and adding overhangs for both practical and aesthetic reasons. Right now it's looking pretty close to a single wide trailer. I would also suggest framing down a flat ceiling over the bathroom as a mechanical loft for equipment and ducts.
I notice you have shown the strapping for both the roof and walls as running vertically, but the corrugated needs horizontal strapping for attachment and support. That's not a problem, as the profile of the cladding allows good venting.
Yes, having added 12" overhangs and making the roof 2/12 to my model there was a significant aesthetic improvement.
I was worried about horizontal strapping but it makes sense that the corrugated has its own channels as well. Thanks
Edit: planning on a flat ceiling in the bathroom with ERV